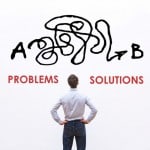
Can you find this common error in detection ranking in the intermediate problem in this article? In the advanced problem, the topic of an in-service detection scale will challenge the most experienced readers.
If you haven’t already read the article Understanding FMEA Detection Risk – Part 1, this may be a good time to read about the underlying fundamentals of assessing detection risk in FMEAs.
Beginner’s Problem
You are doing a Design FMEA and it is time to identify the detection ranking for a given failure mode/cause. One of your team members asks you to clarify the definition of detection. Identify which of the following are correct or incorrect responses to this question?
1. Detection ranking considers the likelihood that the current detection-type design controls will detect the failure mode/cause.
2. Detection ranking is associated with prevention-type design controls.
3. Detection is the likelihood that the effect of the failure mode will manifest sometime during the product life cycle.
4. Detection ranking is associated with detection-type design controls.
Beginner’s Solution
1. Detection ranking considers the likelihood that the current detection-type design controls will detect the failure mode/cause. Correct
2. Detection ranking is associated with prevention-type design controls. Incorrect.
3. Detection is the likelihood that the effect of the failure mode will manifest sometime during the product life cycle. Incorrect.
4. Detection ranking is associated with detection-type design controls. Correct
Intermediate Problem
You are doing a Design FMEA on the hand brake subsystem of an all-terrain bicycle. Review the following excerpt from this FMEA and determine the error in detection ranking.
Intermediate Solution
The team has assigned a detection ranking of “2” for the cause “cable binds due to inadequate lubrication.” Remember, the definition of detection is “a ranking number associated with the best control from the list of detection-type controls, based on the criteria from the detection scale.” Since there is no detection-type control for this cause, the detection risk would be very high.
Advanced Problem
Company X is developing a next generation sub-sea drilling system. Although it is important to detect failure modes and their causes before the new system goes into operation, it is even more important that failures be detected once the system is operating, so that mitigating action can be taken to avoid a potential catastrophe. How can a detection scale be configured to assess detection risk during operation?
Advanced Solution
In-service detection techniques can be designed-in to system operations. An example is a warning system in a nuclear power plant in which sensors detect an emerging problem, alerting personnel who can then prevent the problem or avert it before an accident or serious consequence occurs.
It is possible to define criteria for the detection scale that assesses the likelihood of the monitoring-type control to detect the problem during system operation. The nature of the application should determine the specific criteria of this unique detection scale.
Figure 2 is an example of an in-service detection scale. This scale can be configured to the unique circumstances of the operations being assessed.
Next Article
What if a production worker uses a different cleaning method for an assembly operation than was outlined in the operation work instructions, and the result is customer complaints and field issues. How could this be addressed in a Process FMEA? This question is discussed and answered in the next FMEA Q and A article.
Check out he new FMEA Resources page. It has free downloadable FMEA information and aids.
Hi Carl,
Thank you for your excellent book.
I would like to ask one question in regards to Key characteristics (KC). My doubt is if Detection can participate in the designation of KC. My reasoning is the following: There are features of a product which are easier to detect the failure modes (or the root causes causing that failure mode), e.g.: a electrical measurement it is easy to detect in case of deviation if it is measured 100%, however other parameters for instance coplanarity are more complex to be measured and thus to be detected. Does it make any sense to consider Detection also in the designation criteria for KC in that case apart from Severity and Occurrence? If the detection is “easy” is not considered a a KC, however for “difficult” detection levels can be considered, so the final designation of KC is done considering Severity, Occurrence and Detection, especially for Significant characteristics. I hope you understand the question. Thank you so much!
Hello Francisco,
This is an excellent question.
Although companies can have their own special characteristics policy, there are certain attributes of sp. char. that are important to consider. For example, they should be measurable characteristics of the finished product, and outputs of design that if nonconforming have a potential to impact the safe or proper use of the product. They can be derived from DFMEA. Some companies use Sev as the primary way to designate sp char, others use a combination of Sev and Occ. The reason Det usually does not enter into the policy is being able to measure the sp char is part of the definition. The important aspect of sp char is identifying characteristics that have the potential to impact safe and proper use of the product. If such characteristics can be addressed by robust design, that is best. If not, designating as sp char can help to control the outcome, provided they are followed up with good controls.
Please let me know if this answers your question.
Carl