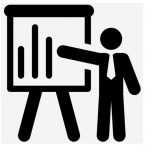
Many companies miss out on the value of System FMEA and begin with lower level sub-assemblies or components. This article explains why it is usually best to begin with a properly done System FMEA.
“Big whirls have little whirls,
That feed on their velocity;
And little whirls have lesser whirls,
And so on to viscosity.”
Lewis Fry Richardson
unique
The Oxford English Dictionary defines “unique” as “being only one of a kind; unlike anything else.”
system
The Oxford English Dictionary defines “system” as “a set of things working together as parts of a mechanism or an interconnecting network; a complex whole.”
What is a System FMEA?
System FMEA is the highest-level analysis of an entire system, made up of various subsystems. The focus is on system-related deficiencies, including system safety, system integration, interfaces or interactions between subsystems or with other systems, interactions with the surrounding environment, human interaction, service, and other issues that could cause the overall system not to work as intended. In System FMEA, the focus is on functions and relationships that are unique to the system as a whole (i.e., do not exist at lower levels). The System level FMEA includes failure modes associated with interfaces and interactions in addition to considering single-point failures (where a single component failure can result in complete failure of the entire system). Some practitioners separate out human interaction and service into their own respective FMEAs.
What is unique about System FMEA?
In my experience, 50% or more of system problems occur at interfaces between subsystems or components, or as a result of integration with adjacent systems. Understanding and addressing interfaces and integration is essential to achieving safe and reliable systems.
System FMEA is uniquely capable of making interfaces and integration issues visible, and addressing them through the FMEA procedure.
For example, if we perform a System FMEA on a bicycle, a fictitious FMEA Block Diagram may look like this.
System FMEA Block Diagram Example-All-TerrainBicycle
One of a number of system level functions might be: Bicycle must provide safe stopping distances.
One of the important system interfaces might be: Seat subsystem to frame subsystem (quick clamp and release feature that provides easy to use and mechanically stable adjustment to seat height)
The System FMEA considers the most important unique system functions and interfaces, and uses FMEA procedure to improve the system design and reduce system risk.
When to do a System FMEA
New product programs usually begin with a System FMEA. If existing designs are changed, the System FMEA may need to be updated in order to ensure the changes are safe, reliable and cost effective.
FMEA Tips
The scope of the System FMEA should be determined at the outset of the FMEA project. For example, the System FMEA team may consider including human interactions, service or software. These areas can be included within the scope of the System FMEA project or addressed with their own FMEAs.
Reader Question
I have questions about the following points.
1. DFMEA captures the risk level and the reliability estimation at design phase since it is capturing design characteristics of failure.
2. In the same way, Process FMEA captures the process related failures.
My question is can we link DFMEA and PFMEA together and come up with a reliability prediction and the risk level of product through FMEA?
My Reply
Although FMEA can provide selected information that is sometimes used in a reliability prediction model, FMEA is not intended to predict reliability. It is intended to analyze and improve designs or manufacturing processes, identify risk, and recommend actions that will reduce risk to an acceptable level.
From the design side, some people leverage the occurrence ratings for causes associated with failure modes, and use reliability system modeling to develop a reliability prediction based on the product design. This assumes that occurrence ratings are objective and can be used outside of the FMEA. However, according to FMEA standards, “The occurrence ranking number has a relative meaning rather than an absolute value.” It was designed to be used within an FMEA, as part of the risk assessment to prioritize remedial actions.
Similarly, from the process side, the occurrence ranking number has a relative meaning rather than an absolute value. Although assumptions can be made that would allow reliability calculations, that is not the intended use of occurrence ratings. I prefer to use system reliability modeling to estimate reliability.
Regarding using FMEA to understand the risk level of the product, this can definitely be done. This is one of the objectives of FMEA. Proper use of the risk rankings for severity, occurrence and detection can provide useful insight into product risk.
Next Article
More than one operational mode may have to be considered to ensure that all important failure modes are identified and analyzed in the FMEA. This next article focuses on what you need to know about modes of operation when performing FMEAs.
Leave a Reply