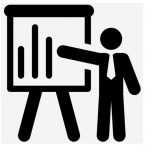
The Proper Application of Failure Mechanisms in FMEA
The rule is simple. For high-risk issues, the FMEA team needs to properly identify the cause(s) and associated failure mechanism(s). So, what exactly is a failure mechanism?
“Nature never breaks her own laws.” Leonardo da Vinci
Definition of “failure mechanism”
“Failure mechanisms are the physical, chemical, thermodynamic or other processes that result in failure. Failure mechanisms are categorized as either over-stress or wear-out mechanisms. Over-stress failure arises because of a single load (stress) condition, which exceeds a fundamental strength property. Wear-out failure arises as a result of cumulative damage related to loads (stresses) applied over an extended time.”
(Reference paper titled “Physics-of-failure-based prognostics for electronic products,” by Michael Pecht and Jie Gu)
Application of Failure Mechanisms in FMEAs
For Design FMEAs at the component level, causes can be further defined and developed by understanding the underlying failure mechanisms. Causes are the circumstances that induce or activate a failure mechanism.
Wherever possible, for high-risk issues the FMEA team should define the cause at the failure mechanism level. This means for System FMEAs or Subsystem FMEAs, the FMEA team should either proceed with a Component FMEA that can drill down to the precise failure mechanism that explains the failure mode and include it in the description in the cause column, or continue with the “Five Whys” until isolating the cause at the mechanism level. No matter how the FMEA team chooses to proceed, wherever possible the FMEA team should properly define the cause at the failure mechanism level for high-risk issues.
The FMEA team should include representatives that understand the specific underlying failure mechanisms for the type of items being analyzed.
The cause/failure mechanism description can be included in the “Cause” column of the FMEA or a separate “Failure Mechanism” column can be used.
Examples of failure mechanism categories
}Failure mechanism categories relating to metal structure components include corrosion, cracking, deformation, embrittlement, fatigue, fracture, friction, yielding, wear, etc.
}Failure mechanism categories relating to electrical components include dielectric breakdown, electro-migration, induced current, voltage drop, etc.
}Failure mechanism categories relating to elastomers include abrasive wear, compression set, extrusion, hardening, shrinking, swelling, etc.
Example of a failure mechanism in FMEA
In chapter 3 of my book, I show an illustration of the progression of failure modes and causes as the FMEA shifts from system to subsystem to component. This illustration is reprinted here.
Failure Mode and Cause progression
Notice the application of failure mechanism in the component-level Brake Cable Design FMEA. Two of the causes for the failure mode “cable breaks” are repeated below.
“Corrosion of cable wiring due to wrong material selected” In this example, the cause is “wrong material selected,” and the failure mechanism is “corrosion.”
“Fatigue cracks in cable wiring due to inadequate cable thickness” In this example, the cause is “inadequate cable thickness,” and the failure mechanism is “fatigue cracks.”
FMEA Tip
One of the common mistakes is to describe the failure mechanism without also describing the cause of failure. When we say, “the FMEA team should properly define the cause at the failure mechanism level for high-risk issues”, we mean both failure mechanism and cause are described.
FMEA Problem and Solution
Problem
A Design FMEA is being done on a burner and heating coil sub-assembly. A portion of the FMEA is shown below:
Function: Heat the burner plate to 160 F within 60 seconds
Failure Mode 1: Burner plate stays cold
Effect: no heat to container, customer dissatisfied
The team is working on the description of potential causes for the failure mode “burner plate stays cold.” They have decided to enter in the “Cause” column the root cause, as well as the associated failure mechanism. One of the Cause entries the team identified has to do with a voltage drop over the heating coil possibly because of a wrong wire specification.
Another Cause entry has to do with possible corrosion of the heating coil-to-burner plate connector resulting from moisture. For both of these Cause entries, write which portion of the description is the actual cause and which portion is the failure mechanism.
Solution
Cause 1: heating coil has voltage drop (failure mechanism) due to wrong wire specification (cause)
Cause 2: heating coil-to-burner plate connector corrodes (failure mechanism) due to moisture intrusion (cause)
FMEA Question
Reader:
Our company is in the phase to work with an updated FMEA procedure based on your course that we went to last year. I would like to have your thoughts regarding risk matrix and risk matrix ranking.
Carl:
Glad to hear your company is working on an updated FMEA procedure.
Companies can use a risk matrix, when focus is on severity and occurrence, to help identify the priority for actions. A fictitious example from chapter 7 of my book:
Example of Severity-Occurrence Risk Matrix
Companies can also use risk prioritization logic, when focus is on severity, occurrence and detection. Utilizing custom risk prioritization logic avoids the pitfalls of RPN thresholds by allowing for the possibility of establishing action prioritization for the different combinations of S, O, and D. Risk prioritization logic has the ability to highlight with colors (such as red, yellow, and green) or with numbers (such as 1, 2, and 3) the associated risk. These can be tailored to specific company priorities.
Next Article
Continuing the series of articles on special topics, the next article will be on the “Five Whys.” By continuing to ask “why,” the team will be able to discover the progression of cause-and-effect relationships behind a problem and the root cause that is below the surface.
Leave a Reply