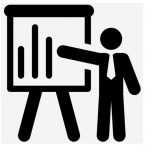
“Science is the process that takes us from confusion to understanding…” – B
Properly done, Process FMEAs should improve manufacturing and assembly processes and corresponding process controls. This article describes how PFMEAs can be used to improve process controls, which are embodied in the Process Control Plan (PCP).
What is a Process Control Plan?
A Process Control Plan (PCP) is a document that provides a “summary description” of the methods used in the manufacturing environment to minimize variation and control product and process characteristics in order to ensure capability and stability of the manufacturing process. It is a structured approach for the design, selection and implementation of control methods, and reactions to problems with the manufacturing and assembly operations when they do occur.
How do Process FMEAs improve PCPs?
The Process FMEA is a key contributor to the effectiveness of the Process Control Plan. This linkage between the PFMEA and the PCP goes two ways:
The Process FMEA team includes representation from the manufacturing controls area, in order to ensure that the team considers all needed input from process controls as part of the analysis.
When the Process FMEA team identifies failure modes and associated causes that are not currently detected or controlled in PCPs or associated procedures, the PCP and procedures can be updated and improved, so all failure modes of concern are detected and controlled during manufacturing or assembly. Any changes to PCPs or procedures that come from the PFMEA should be included in the Process FMEA recommended actions.
Why enter PCP improvements in the Recommended Actions column of the FMEA?
As covered in a previous article, the short answer is everything that the FMEA team believes needs to be done differently from what is already planned or in place should go in the Recommended Actions column of the FMEA. The reason for this is the entries in the Recommended Actions column have additional information to facilitate the execution of the task that is recommended, such as the person who is responsible for the execution of the task, the target date when the task should be completed, and other project management information.
How does the PFMEA link to the PCP?
The following is a fictitious and simplified example of a Process Control Plan for wheel-spoke installation for the front wheels of a bicycle, excerpted from chapter 6 of the book Effective FMEAs.
We’ll start with the Process Flow Diagram (PFD) and link one of the process steps 1.2.6 to the PFMEA and the PCP.
Process Step 1.2.6: “Orient and place wheel spokes in wheel rim assembly fixture.”
Here is the corresponding PFMEA excerpt, showing the process function and a single failure mode and associated cause.
In this example, we’ll use the following information from the PFD and the PFMEA to link with the PCP.
Process Function: “Orient and place wheel spokes in wheel rim assembly fixture.”
Significant Product Characteristic: “Correct number of wheel spokes.”
Significant Process Characteristic: “Correct kit of 36 spokes.”
Failure Mode: “Wheel spokes not in the correct orientation.”
Cause: “Fixture is not error-proofed to prevent incorrect orientation.”
The PFD and PFMEA can be linked to the PCP as follows:
1. The Process Function from the PFMEA (Orient and place wheel spokes in wheel rim assembly fixture) is entered in the “Process Name / Operation Description” of the PCP.
2. The Significant Product Characteristic in the Process Flow Diagram (Correct number of wheel spokes) is entered in the “Product” column of the PCP. Note, “Correct number of wheel spokes” is associated with the failure mode in the PFMEA.
3. The Significant Process Characteristic from the Process Flow Diagram (Correct kit of 36 spokes) is entered in the “Process” column of the PCP. Note, “Correct kit of 36 spokes” is associated with the cause in the PFMEA.
4. If there is an associated Significant Product Characteristic or Significant Process Characteristic in the DFMEA or PFMEA associated with the Failure mode / Cause, this is noted in the “Special Char.” column in the PCP.
5. The Current Process Controls from the PFMEA (Wheel spoke installation work instructions and Visual check of wheel assembly by an operator) are entered in the “Control Method” column of the PCP.
The process control team can enter the remaining information into the PCP.
FMEA Tips
The Design FMEA can identify Key Product Characteristics (KPCs). KPCs are input to the Process FMEA and require follow-up in the Process Control Plan. They usually have their own approval process.
The Process FMEA can identify Key Control Characteristics (KCCs). Similar to KPCs, they require follow-up in the Process Control Plan.
When the Design FMEA team identifies and communicates KPCs to the Process FMEA team, this is one of the linkages between Design and Process FMEAs.
Summary
One of the objectives of Process FMEA is to improve the Process Control Plan. Following the suggestions in this article will help Process FMEA teams accomplish this purpose.
Next Article
FMEAs are intended to anticipate potential risk and develop actions that will reduce risk to acceptable levels. Is it possible to know and anticipate all of the potential risks? The next article takes up this important topic.
Leave a Reply