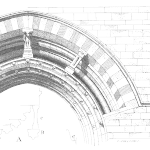
Reliability, Availability, and Maintainability (RAM) modeling overview
The concept of Reliability Block Diagrams (RBD) is also known as Reliability Modeling or Reliability, Availability, Maintainability (RAM) analysis. With RAM models, the interaction of large, complex, and multi-layered systems can be analyzed using Monte Carlo simulation methods. This help quantify the output of the entire system with greater accuracy than other estimating tools or methods.
In various industries, RAM models have proven to be effective as cost avoidance or decision-making tools. The models are also able to confirm or challenge stated assumptions by internal stakeholders. Equipment upgrades and equipment sparing decisions are often seriously debated, and costly decisions may not always be based on complete economic foundations. Rather, they are based on avoiding past negative experiences or following basic guidelines that are less than optimal. When a project or operational team needs to find an alternative, RAM modeling becomes a tool of choice to evaluate and justify the best option(s).
The fundamental purpose of RBD modeling is quantifying system performance. A system is a collection of items whose coordinated operation leads to the proper functioning of the system. The collection of items includes subsystems, components, software, human operations, etc. In RBDs, it is crucial to account for relationships between items to determine the various outputs of the system.
RAM modeling for contracts
RAM models are commonly used to establish maintenance strategies or quantify operational outputs. However, they are not the primary tool of choice when drafting a contract between two parties in industrial operations. The great advantage of RBDs is the multifaceted outputs they provide. This ranges from quantifying production losses and justifying new investments to determining min-max levels of spare parts in warehouses. And in our case here, contractual terms.
The following example highlights a situation when a contract is being established between a pipeline shipper and a pipeline operator. A shipper is typically the provider of throughput to the pipeline operator. The pipeline operator then ships the product to the agreed destination for a fee. In essence, this is an easy transaction, but in reality, mishaps occur. For example, planned maintenance or unplanned events can shut down the pipeline. Whatever the reason, a pipeline shutdown could cause the shipper to also interrupt their operation. For example, if their storage capacity is at its maximum. Likewise, if the shipper is down and runs out of product, the pipeline operator will go idle and lose revenue. Either way, there could be financial penalties based on the contractual agreements.
Let us focus on the pipeline operator in this example. If the contractual agreement states that the pipeline operator cannot be shut down for more than 10 consecutive hours, is this a realistic and achievable clause? It might not be, and if accepted as such, it exposes the pipeline operator to penalties. This could also damage customer relations with the shipper.
How does a RAM model help establish the terms in the contract?
The RAM model is able to quantify the duration of each downtime event for the system. It can also quantify the frequency of the downtime events beyond a specific threshold, say 10 hours. Using this downtime report, one can not only estimate the probability of having downtime of more than 10 hours but also the probability of having multiple instances in a specified time period (say, in 10 years in relation to the contract validity). For example, the result could read as follows: the probability of having a downtime event exceeding 10 hours in a period of 1 year is 75%. Or, the probability of having 3 downtime events exceeding 10 hours in the same year is 30%. This information can then be used by the pipeline operator to gauge the risk they are willing to take on and establish the contractual terms accordingly.
This quantified risk analysis now helps both parties negotiate within a more realistic framework regarding what is achievable and what is not. The shipper is in a better position to decide what risk they are prepared to accept. Likewise, the operator understands the risk they will be taking on. This information, and essentially the RAM model, also helps the pipeline operator investigate which assets might be causing downtime. In doing so, the areas of highest operational risk are identified and appropriate mitigation can be implemented. For example, if an asset failure is likely to bring the pipeline down for more than 10 hours, what is the mitigation plan for the asset failure? To summarize in a phrase: knowledge is key, and in this case, robust and quantified predictions are the foundation for more balanced contractual agreements.
Leave a Reply