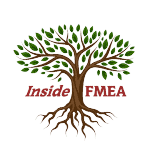
New Insights on Achieving FMEA Excellence
Do you consider yourself new to FMEA, or are you an FMEA expert?
Or somewhere in between?
I’m a great believer that knowledge of any tool such as FMEA, is a lifelong journey. In the new series of articles called Inside FMEA, my intention is to bring to life the subject of FMEA, and provide value to readers from all levels of experience.
Each week I will publish a new article on Accendo. The topics will span the full range of FMEA applications, and offer guidance to real-world challenges that FMEA teams face each and every day.
Albert Einstein once said, “The search for truth and knowledge is one of the highest qualities of man.” Having supervised or performed over two thousand FMEAs, I believe I have seen every possible way they can be done wrong. The search for FMEA excellence has been my guiding principle. Learning the fundamentals of FMEA is not difficult. Learning to achieve uniformly excellent results in the real world of limited resources and compressed time is more challenging. I wish to share my experience in helping you get excellent results in the real world.
There is a reason that FMEA is at the heart of Design for Reliability and Design for Six Sigma. Few tools have the potential to improve designs and processes as does FMEA, yet the results do not always meet expectations.
When I write about FMEA, I often begin with an introduction such as the following:
“Failure Mode and Effects Analysis (FMEA) can anticipate and prevent problems, reduce costs, shorten product development times, and achieve safe and highly reliable products and processes. The plain truth is FMEA has the potential to be a very powerful tool to achieve high reliability in products and processes; and when done well, it is remarkably effective. Yet in practice, FMEA does not always achieve the expected results. It has to be done correctly: performed on the correct parts, by the correct team, during the correct timeframe, with the correct procedure.”
Ongoing Series Structure
The pursuit of knowledge is best done with multiple learning strategies. Articles in this series will rotate between three types, which can be recognized with these icons:
1. FMEA Prinicples (reviewing definitions and fundamental concepts, real-world examples, and application insights and tips)
2. FMEA problems and solutions, and
3. FMEA questions and answers
Inside FMEA topics
All of the Inside FMEA articles will be organized into topical groupings.
The first group, “Introduction to FMEA Series,” provides an overview to the subject of FMEA, and outlines the most important factors for successful FMEA projects.
The second group, “FMEA Fundamentals Series,” takes up each of the FMEA worksheet elements, such as Functions, Failure Modes, etc., one by one. Each worksheet element is explored first by understanding the basics, followed by application information and tips, and finishing with related problems and solutions, for both beginners and advanced readers. In between the worksheet elements will be questions from readers, with my answers.
The third group, “FMEA Preparation Series,” is based on the premise that achieving high-quality FMEAs depends on proper preparation. Similar to painting a house, where the preparation steps are essential to excellent painting results, FMEA preparation is essential to FMEA success. This series is broken down into each of the essential preparation steps that need to be done before commencing with FMEA meetings.
The fourth group, “FMEA Facilitation Series,” covers different subjects that are important for success in leading FMEA teams. This is often missed, as FMEA success depends on good facilitation of FMEA teams.
The fifth group, “FMEA Special Topics Series,” takes up a wide variety of interesting, useful, and sometimes controversial topics on the subject of FMEA. Everything from application of failure mechanisms, to the most common FMEA mistakes will be explored in this series of articles.
Readers of my book, Effective FMEAs, will find the content of the Inside FMEA articles consistent with the concepts in the book.
It is my sincere desire that each and every person who reads Inside FMEA articles will discover the articles enjoyable to read and experience improved success in FMEA applications. As I say to readers of my book, “best wishes for effective FMEAs.”
Carl S. Carlson
Contacting the author
Readers are encouraged to contact me with any questions about FMEA, or feedback on Inside FMEA articles. Questions, feedback, and ideas for future articles can be sent to carl.carlson@effectivefmeas.com. I will personally respond to all questions and feedback.
You can also use the “Ask Carl a Question” button that will be loacted at the bottom of each article. Try it now, if you have a question ready.
Albert Einstein once said, “The important thing is not to stop questioning.” My interpretation: never be afraid to ask questions. It’s one of the best ways to continue learning.
Next Article
Should an FMEA result in design or manufacturing improvements? Should it ensure that tests discover the right problems? What are the objectives of FMEAs? Whether you are new to FMEA or an experienced practitioner, there is always something to learn. The next article is called simply “What is FMEA?”, and should expand the knowledge of every reader.
Failure mechanisms are the processes by which physical, electrical, chemical and mechanical stresses induce failure. Knowledge of the failure mechanisms that cause product failure is essential to design and qualify reliable products. The standard Failure Modes and Effects Analysis (FMEA) and Failure Modes, Effects and Criticality Analysis (FMECA) procedures do not identify the product failure mechanisms and models, which limits their applicability to provide a meaningful input to critical procedures such as virtual qualification, root cause analysis, accelerated test programs, and to remaining life assessment.
Failure Modes, Mechanisms and Effects Analysis (FMMEA) enhances the value of FMEA and FMECA by identifying high priority failure mechanisms and failure models. High priority failure mechanisms determine the operational stresses, and the environmental and operational parameters that need to be controlled. Models for the failure mechanisms help in the design and development of a reliable product.
CALCE ( http://www.calce.umd.edu/ ) has developed the FMMEA process and helped several organizations implement the tool in their product development process
Excellent comment, Hilaire!
I have a section in my “Effective FMEAs” book on FMMEA, and agree on the value of this type of FMEA. Design FMEAs should drill down to root causes, including failure mechanism, for all high-risk issues. By identifying and understanding the underlying mechanism of failure, and the corresponding model, the FMEA team can bring about more effective actions. Many companies add a failure mechanism column in the FMEA worksheet.
By the way, I was a reviewer for one the the articles on FMMEA, and the CALCE team published a very nice review of my book.
I’ll be writing a future “Inside FMEA” article on the application of failure mechanisms in FMEAs.
Carl; I am pleased with your work on the subject of FMEA