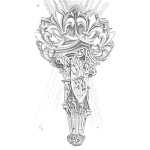
Once upon a time in my former life, I served as the Quality Manager for a $300M tier-one automotive manufacturing plant that provided components and assemblies to OEM vehicle assembly plants. You would recognize our customers – most of the big names. This assignment was a departure from my previous roles in product development and testing. To say that the job was eye-opening is an understatement. Years later, I described this three-year experience to friends as my “tour of duty on the front lines.” Anyone who has spent any time in manufacturing can certainly relate!