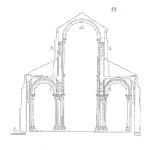
Is a logical, graphical diagram that organizes the possible element failures and combination of failures that lead to the top level fault being studied.
The converse, the success tree analysis, starts with the successful operation of a system, for example, and examines in a logical, graphical manner all the elements and combinations that have to work successfully.
With every product, there are numerous ways it can fail. Some more likely and possible than others. The FTA permits a team to think through and organize the sequences or patterns of faults that have to occur to cause a specific top level fault. The top level fault may be a specific type of failure, say the car will not start. Or it may be focused on a serious safety related failure, such as the starter motor overheats starting a fire.
A complex system may have numerous FTA that each explore a different failure mode.
The primary benefit of FTA is the analysis provides a unique insight into the operation and potential failure of a system.
This allows the development team to explore ways to eliminate or minimize the occurrence of product failure. By exploring the ways a failure mode can occur by exploring the individual failure causes and mechanisms, the changes impact the root cause of the potential failures.
The benefits include:
1. Identify failures deductively. Using the logic of a detailed failure analysis and tools like ‘5 whys’, FTA helps the team focus on the causes of each event in a logical sequence that leads to the failure.
2. Highlight the important elements of system related to system failure. The FTA process may lead to a single component or material that causes many paths to failure, thus improving that one element may minimize the possibly of many failures.
3. Create a graphical aid for system analysis and management. Apparently managers like graphics, and for complex system, it helps to focus the team on critical elements.
4. Provides an alternatively way to analysis the system. FMEA, RBD and other tools permit a way to explore system reliability, FTA provide a tool that focuses on failure modes one at a time. Sometimes a shift in the frame of reference illuminates new and important elements of the system.
5. Focus on one fault at a time. The FTA can start with an overall failure mode, like the car not starting, or it can focus on one element of the vehicle failing, like the airbag not inflating as expected within a vehicle. The team chooses the area for focus at the start of the analysis.
6. Expose system behavior and possible interactions. FTA allows the examination of the many ways a fault may occur and may expose non-obvious paths to failure that other analysis approaches miss.
7. Account for human error. FTA includes hardware, software, and human factors in the analysis as needed. The FTA approach includes the full range of causes for a failure.
Just another tool in the reliability engineering toolbox. For complex systems and with many possible ways that a significant fault may occur, FTA provides a great way to organize and manage the exploration of the causes. The value comes from the insights created that lead to design changes to avoid or minimize the fault.
Related:
Fault Tree Analysis 8 Step Process (article)
Intro to Fault Tree Analysis (article)
Deciding What Should Have Fault Tolerance (article)
Very informative and educative
Pl. arrange to provide few examples for understanding and clarity of FTA
Pls. may I request to show simple examples for quality and safety in construction industry.
This content is very informative.
Small concern;
Check on the second paragraph. I think it is a mistakenly repeating the last part of the first paragraph
thanks and you are right, and now the duplicated line is resolved