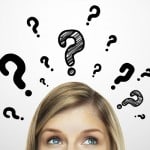
FMEA Q and A
Is it a good idea to do one generic FMEA for wiring harnesses, and use it as a reference for other FMEAs for similar applications? What about interfaces? These questions are discussed and answered in this FMEA Q and A article.
“We live in the world our questions create.”
David Cooperrider
Reader’s Question
First, let me say I am enjoying your book. We are looking at doing a DFMEA on wire harnesses for a particular type of farm equipment. We would like to do one generic FMEA on harnesses, and use it as a reference for other FMEAs, since we typically cover the signal requirements for control and feedback in the different system FMEAs. What are your thoughts?
Answer to Reader’s Question
I’m glad you are enjoying the book. Regarding your question on wiring harnesses, here are my thoughts. As you suggest, the wiring harnesses can be combined into one good Design FMEA, which can be the repository for the functions, failure modes, effects, causes, and controls for a generic wiring harness. This is provided the various wiring harnesses are similar enough to be included in one FMEA. Generic FMEAs can save time and improve FMEA effectiveness, provided they are done correctly, and provided the FMEA team pays attention to certain application issues. The interfaces between the wiring harnesses and other components and subsystems, both software and hardware, must be taken into account. The signal communications can be included (as you say) in a properly done System FMEA, or in a separate Software FMEA. The hardware interfaces must be included somewhere, either in Subsystem FMEAs or in other FMEAs. The key is to “make it visible”: FMEA Block Diagrams, P-Diagrams, Functional Block Diagrams, FMEA Interface Diagrams, as covered in chapter 5 of my book. With visible diagrams, you can be sure that all interfaces and functions are properly covered. Let me know if you have any other questions.
Next Article
Why do we limit entries into the prevention or detection control column to actions or methods that are currently planned or in place? In the next article, the essential elements of FMEA Controls are presented.
Failure mechanisms are the processes by which physical, electrical, chemical and mechanical stresses induce failure. Knowledge of the failure mechanisms that cause product failure is essential to design and qualify reliable products. The standard Failure Modes and Effects Analysis (FMEA) and Failure Modes, Effects and Criticality Analysis (FMECA) procedures do not identify the product failure mechanisms and models, which limits their applicability to provide a meaningful input to critical procedures such as virtual qualification, root cause analysis, accelerated test programs, and to remaining life assessment.
Failure Modes, Mechanisms and Effects Analysis (FMMEA) enhances the value of FMEA and FMECA by identifying high priority failure mechanisms and failure models. High priority failure mechanisms determine the operational stresses, and the environmental and operational parameters that need to be controlled. Models for the failure mechanisms help in the design and development of a reliable product.
Center for Advanced Life Cycle Engineering (CALCE) has developed the FMMEA process and helped several organizations implement the tool in their product development process
Hello Hilaire. Thanks for your well thought out comments about the value of including failure mechanisms in FMEA. I completely agree! I always teach that higher-risk issues in an FMEA must be taken to root cause and failure mechanisms. And I make this point in detail in my book. A also have a section in chapter 15 of my book on FMMEA, and have worked with colleagues at CALCE on FMMEA papers and dialog. FMMEA does exactly as you say.
One point about your comment. One of the most well-known FMEA references is AIAG 4th edition. On page 39 there is a section on “Potential Mechanism(s) of Failure Mode”, which defines failure mechanisms and how to use them in FMEA procedure. However, as you point out, the FMEA standards to not discuss the modeling of failure mechanisms, which is important.
Have you used FMMEA? I’d be interested in any comments on the application.
Carl