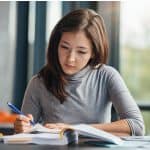
When creating a robust design, there is probably no more important consideration than identifying the correct parameters and associated values. A robust design is insensitive to anticipated variation and P-Diagram visually shows the relationship between what the system is designed to do, the anticipated noises the system will encounter and the correct parameters to achieve the desired outcome. P-Diagram can be an essential input to FMEA.
“Concern for man and his fate must always form the chief interest of all technical endeavors. Never forget this in the midst of your diagrams and equations.” Albert Einstein
parameter
The Oxford English dictionary defines “parameter” as “a numerical or other measurable factor forming one of a set that defines a system or sets the conditions of its operation.”
diagram
The Oxford English dictionary defines “diagram” as “A simplified drawing showing the appearance, structure, or workings of something; a schematic representation.”
What is a P-Diagram?
[Excerpt from Effective FMEAs]
J. M. Juran explains the concept behind P-Diagrams in his book Quality Planning and Analysis, in the chapter “Designing for Basic Functional Requirements.” Juran says, “The most basic product feature is performance, i.e. the output – the color density of a television set, the turning radius of an automobile. To create such output, engineers use principles to combine inputs of materials, parts, components, assemblies, liquids, etc. For each of these inputs, the engineer identifies parameters and specifies numerical values to achieve the required output of the final product.”
“The Parameter Diagram (P-Diagram) takes the inputs from a system/ customer and relates those inputs to desired outputs of a design that the engineer is creating, also considering non-controllable outside influences.” It is a useful tool in brainstorming and documenting input signals, noise factors, control factors, error states and ideal response, as defined below.
When is a P-Diagram used?
A P-Diagram is an optional step when preparing for a System or Subsystem FMEA. It is most useful when the item under analysis is a complex system with many system interactions, operating conditions and design parameters, and the team will benefit from seeing these elements visually. It is a time intensive step, but can provide great value in understanding and controlling the system, and identifying input to the FMEA. P-Diagram can also be used when preparing for a component FMEA, if the FMEA team believes there is sufficient value in visually representing inputs, ideal response, and noise/control factors.
What does a P-Diagram look like?
The following is an example of a P-Diagram, with an explanation for each of the elements.
P-Diagram definitions
Input Signals are a description of the energy sources required for fulfilling the system functionality, such as speed, acceleration, input torque, etc.
Control Factors are typically the system design parameters that the engineering team can change, such as shaft diameter, stiffness, density, hardness, etc.
Error States are any kind of inherent loss of energy transfer or other undesirable system outputs, such as exhaust gases, heat, vibration, leakage, unusual noise, or bad odor.
Noise Factors are things that can influence the design but are not under the direct control of the engineer, such as piece-to-piece variation, normal degradation of materials or equipment over time, intended and unintended customer usage, foreseeable environmental conditions, and system interactions. These noise factors, if not protected against, can make the design ineffective; in other words, the design is not robust against the expected noise factors.
Ideal Response is the primary intended functional output of the system, such as output torque, etc.
How do the various elements of P-Diagram map to FMEA?
The elements (boxes) of the P-Diagram can be associated with the elements (columns) of FMEA in the following manner.
Input Signals are helpful as part of System FMEA preparation. They help the FMEA team understand the nature of the system being analyzed. Individual inputs can be associated with ideal responses (intended outputs of the system).
Control Factors are the system design parameters that the engineering team can change, such as shaft diameter, stiffness, density, hardness, etc. One of the applications of control factors is to identify significant product characteristics, which are the direct output of a given manufacturing operation. Key Product Characteristics (KPCs) are a subset of significant product characteristics, and are designated by the company for highlighted attention. They require follow up in the Process Control Plan and usually have their own approval process. KPCs map to the Classification column of the FMEA. Control factors can also be used to help the FMEA team identify potential cause descriptions in the FMEA.
Error States can be considered as input to Failure Mode descriptions.
Noise Factors, by definition, are things that can influence the design but are not under the direct control of the engineer, such as piece-to-piece variation, normal degradation of materials or equipment over time, intended and unintended customer usage, foreseeable environmental conditions, and system interactions. These noise factors, if not protected against, can make the design ineffective; in other words, the design should be robust against the expected noise factors. We’ll examine the various types of noise factors to see how they map to FMEA.
Piece-to-piece variation is uncontrollable variation in parts or manufacturing process.
Recall the Inside FMEA article on Ground Rules and Assumptions.
In this article, one of the assumptions to consider is as follows:
For Design FMEAs:
Does the FMEA team assume the product will be manufactured or assembled within engineering specifications?
Does the FMEA team wish to consider an exception, such as that the part design may include a deficiency that could cause unacceptable variation in the manufacturing or assembly process?
Piece-to-piece variation in the P-Diagram can be input to the assumptions in the System FMEA.
Change over time identifies anticipated degradation of components or materials that are part of the system. In the FMEA, these can be useful inputs to failure mode descriptions and can help identify the specific failure mechanisms that are associated with cause descriptions.
Customer usage / duty cycle document how the customer uses the system, either intended or unintended. These are assumptions that are part of FMEA preparation.
External environment is the set of anticipated environmental conditions that the system must operate within. Similar to Customer usage / duty cycle, these are assumptions that are part of FMEA preparation.
Ideal Response is the primary intended outputs of the system. These map to the FMEA function descriptions.
FMEA Tips
One of the applications of noise factors is to be certain that the system design is robust in spite of each of the noise factors. A good suggestion is to identify a one- or two-sentence robustness strategy for each of the noise factors that you are concerned about in your p-diagram.
FMEA Q&A
“The important thing is not to stop questioning.” – Albert Einstein
Reader question:
First of all, thanks for sharing your expertise on FMEA.
My question / observation is related to the “Team Composition”. I agree with you that one big issue is that very often there are not the right experts around the table. However, in my opinion another common problem is that very often there is no good (and “independent”) facilitator leading the FMEA. I think this has a huge impact on the overall FMEA effectiveness.
Could you share your opinion/experience on that?
Answer:
I agree with your premise that lack of skilled facilitation of an FMEA team may lead to less than optimum results and the FMEA team not achieving their full objectives. I look at FMEA facilitation as a different skill set than FMEA expertise. I want a skilled facilitator leading an FMEA, where possible. If you have a copy of my book, I cover the importance of the facilitator and the specific skills of FMEA facilitation in chapter 10 of my book.
Regarding the “independence” of the FMEA facilitator, I’ll draw on the following excerpt to help illustrate this topic.
“The facilitator is not a passive position but a pro-active role also encompassing general leadership skills. Some companies have tried introducing FMEA facilitators in a passive or “neutral” role, not offering their own expertise or opinions concerning the content of the FMEA. Best practice is the FMEA team led by a trained and experienced facilitator who also brings his or her own subject matter expertise to the meetings. For example, the FMEA facilitator might be a reliability or quality engineer; in addition to facilitating the FMEA process and the team meetings, this person also brings reliability or quality expertise to the meetings and has opinions to offer on the content of the FMEA. In order to perform these dual roles, the facilitator must be well skilled in facilitation techniques.”
Next Article
One of the least understood and most important aspects of FMEA preparation is to identify and prioritize the functions that are within the scope of the FMEA project. Interface functions will be visually depicted in the FMEA Block Diagram. Basic functions will be explained in the corresponding technical specifications or identified by the FMEA team. Each function will receive a mini-FMEA, and properly identifying and prioritizing functions is a key preparation step.
Hai
In the new release of AIAG-VDA FMEA Handbook there is no mention about System FMEA.
Does this mean that DFMEA covers this aspect.
Thanks in advance
You are correct that the new AIAG/VDA handbook does not mention System FMEA as a separate type of FMEA. It includes System FMEA along with Subsystem and Component FMEAs in the category of Design FMEA.
I prefer to single out System FMEA separately from other Design FMEAs. System FMEA places special emphasis on external and internal interfaces, along with functions that are unique to the overall system. it can also include human interactions.
Quoting from my book:
“System FMEA is the highest-level analysis of an entire system, made up of various subsystems. The focus is on system-related deficiencies, including system safety, system integration, interfaces or interactions between subsystems or with other systems, interactions with the surrounding environment, human interaction, service, and other issues that could cause the overall system not to work as intended.”
Hope that helps.
Carl
Hi Carl
I am big fan of your clear thoughts about FMEA system and following you closely. I am facilitating FMEA course from last 8 years. To my understanding when we talked about DMFEA, it covers system, sub-system and component level details while i encountered one new type of FMEA called assembly FMEA. Can help to explain the difference b/w assembly and component FMEA?
Hi Raj,
I don’t have knowledge of an agreed-upon definition for the term Assembly FMEA in FMEA standards. However, in some applications it is similar to a subsystem FMEA, where it would be a Design FMEA on the assembly. I’ve also seen Assembly FMEA used as a type of Process FMEA, with the scope of the specific assembly process. I would ask the person who uses the term to explain their definition, in order to be sure.
Carl