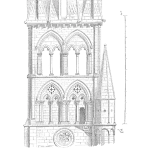
Aside from meeting specific quality system standard requirements—such as those found in ISO 9001 or IATF 16949—well-designed quality system metrics also can serve as meaningful indicators of the strengths and weaknesses of an organization’s various processes.
As a quality manager, I often consider how precisely our quality system objectives and other metrics describe the effectiveness of our systems. One metric I started using recently—overall equipment effectiveness (OEE)—has provided our management team with a composite measurable that encompasses three major branches of our operation: maintenance, production and quality.
Over the past three decades—during which standardized quality systems have taken a prominent role in manufacturing—certain metrics have risen to the top as the most common key indicators of performance in each of these three areas.
Consider this simple example to see how common key indicators work together to form OEE:
Machine availability is a common metric for measuring the effectiveness of an organization’s maintenance process. It’s calculated as the ratio of a machine’s actual run time to its scheduled run time. In some organizations, operator breaks and tardiness can reduce a machine’s run time, but unplanned outages because of maintenance problems always reduce availability.
If for instance, a machine was scheduled to run for eight hours during a given shift, but it actually ran for only 6.1 hours, this would yield an availability of:
(6.1 / 8.0) = 76.3%
For production, efficiency is a key metric calculated as a ratio of the number of parts produced in a certain amount of time to the maximum number of parts that could have been produced in the same amount of time.
If time studies demonstrate that a machine can produce 2,500 pieces per hour, but on a given day an operator produces 13,000 pieces in 6.1 hours of production, this operation ran an efficiency of:
(13,000 / 6.1) / 2,500 = 85.2%.
Quality is typically measured as a ratio of the number of good parts produced to the total number of parts produced. So, if only 12,770 of the 13,000 total parts produced meet the customer’s specifications, the measure of quality acceptance is:
(12,770 / 13,000) = 98.2%.
OEE is calculated as the product of these three metrics:
OEE = % Available x % Efficient x % Acceptable
So for our example, the OEE is:
OEE = 76.3% x 85.2% x 98.2 = 63.8%.
In his book, Overall Equipment Effectiveness, Robert Hansen details the OEE evaluation scale shown in Table 1. According to the scale, the OEE of this process is unacceptable.

OEE essentially is a measure of the total effectiveness of a manufacturing operation. When applied to the bottleneck operation in a process flow, OEE can provide a powerful indicator of the potential sales that are left on the table due to losses in the system. Business analysts refer to the sum of these losses as the effect of the hidden factory.
While the example given earlier uses OEE to measure the effectiveness of a shift, business professionals also can use OEE to compare part families, manufacturing facilities or other logical groupings. Developing and using metrics such as OEE that highlight an organization’s best opportunities for improvement have the potential to unlock the next level of profitability.
REFERENCE
1. Robert C. Hansen, Overall Equipment Effectiveness: A Powerful Production/ Maintenance Tool for Increased Profits, first edition, Industrial Press Inc., 2011.
Leave a Reply