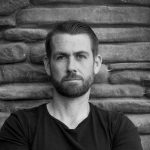
I often start teaching my reliability engineering courses … by focusing on other reliability engineering courses. Why? Because they exemplify what is wrong with how most ‘reliability experts’ go about convincing others to take reliability seriously.
A typical reliability engineering course will start with images of disaster. A Chernobyl here. A Fukushima there. A crashed airplane. The Tacoma Narrows Bridge. Lots of other atrocities that happen when we don’t do reliability engineering properly.
Reliability engineers might even talk about slightly more relatable things like company reputation. Quality. Customer expectation. Emerging technology. User demands.
The problem with all this imagery is that it is abstract. The disasters are rare enough for them to not be tangible outcomes of everyday design decisions. The catastrophes are the combination of tens or hundreds of bad decisions that make it difficult to understand how a single individual contributes to them. And things like brand reputation are great for the shareholders of your company … but what does that mean for my annual bonus when my boss looks at the hydraulic system I designed?
Reliability happens when you become impatient and selfish. And that means everyone in your organization realizes the tangible benefits of reliability that you start reaping from day one.
Reduced production costs … starting now
A common refrain is that …
… you can chose any two of ‘fast,’ ‘cheap’ or ‘reliable.’
This is rubbish.
There are a plethora of examples of companies that were able to do things like reduce recommended retail price (RRP) as the result of a reliability. Just to pick one – Hewlett Packard dropped RRP of its commercial oscilloscopes by 16 % by focusing on reliability.
How?
High reliability means fewer failures. Including ‘production team failures.’
We usually associate ‘failure’ with our product, system or service breaking in the hands of our customer or user. But failures start a lot earlier than that. Production team failures are those annoying instances of our components not aligning, selecting the wrong material, software providing the wrong output and all those other things that ruin our day when we are trying to make something new and amazing. All those little (and not so little) production team failures mean we need to go and redo stuff we already thought (or hoped) we had done. And that costs money.
Reliability engineering means we make our first design a reliable design.
Meaning we don’t throw money away during production.
Speeding everything up … also starting now
Those Hewlett Packard oscilloscopes were produced 30 % faster after their reliability improvement initiative. This is where a lot of the savings that allowed them to reduce the RRP came from.
This is not an isolated exampled. Seasoned reliability engineers who have worked in truly successful organizations could amaze you with all manners of similar stories … if only the details of each amazing success story weren’t commercial-in-confidence!
Isn’t it amazing that companies who renowned for reliability (like Toyota and Apple) are also wildly successful (largest automobile manufacturer and most valuable company respectively)?
Reducing stress. Starting yesterday.
This is not a conclusion everyone leaps to when we think about reliability engineering.
I’ll put it to you this way. Have you ever been in a project where you are involved in something significant, critical, or expensive? I’ll bet that at times throughout that project there are fits of organization-wide pandemonium when we need to check that everything is ‘OK’ or we are ‘on track.’ We might have project management meetings where we go through a 753-point check list of stuff. Or auditors that check everything including font size. Or really, really big PowerPoint presentations.
None of this is truly helpful.
Reliability engineering is all about understanding the vital few things of your product, system or service that will keep you up at night. And instead of having to check everything, we can actually focus on addressing the couple of things that matter the most.
This is a lot less stressful because it creates confidence. Confidence drives down stress. When you are all about compliance, you tend not to be confident because you are all about passing tests. When you focus on the vital few, you know why you are doing the things you do. Not running around like a headless chicken trying to make every person/boss/standard/consultant/auditor/shaman happy.
Impatience and selfishness can be useful
There are plenty more benefits from reliability engineering that you will start to benefit from immediately. There is a catch – you have to take reliability engineering seriously. If you don’t, then you simply impose a bunch of half-hearted initiatives on your people that chew up their calendar and yield little in return.
What about you? Do you have any stories of how reliability engineering started benefitting you straight away? We would love to hear from you!
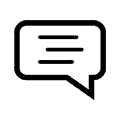
Leave a Reply