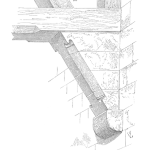
The Kaplan-Meier estimator is the maximum likelihood, nonparametric reliability estimator for censored, grouped lifetime data. It’s traditional. It’s in statistical software. Greenwood’s variance formula is well known. Could Kaplan-Meier be improved: smaller variance, better actuarial forecasts, seasonality, separate cohort variability from reliability? Could you estimate reliability without life data and preserve privacy?
[Read more…]