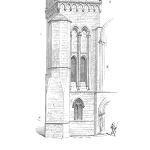
PREVENTIVE MAINTENANCE STRATEGY IN A PLANT WELLNESS WAY EAM SYSTEM-OF-RELIABILITY
IN A PWW EAM SYSTEM-OF-RELIABILITY, PREVENTIVE MAINTENANCE STRATEGY IS TO REPLACE PARTS WHEN EXCESSIVE STRESS BUILD-UPS IN THEIR MICRO-STRUCTURE
Your Reliability Engineering Professional Development Site
This Life Cycle Asset Management article series introduces and discusses life cycle asset management strategies, systems and processes for optimizing operating asset economics, reliability, performance, and return on investment.
Life Cycle Asset Management, Enterprise Asset Management (EAM), Engineering Asset Management, and Physical Asset Management (and their linguistic variations) are considered to be synonymous names. Life Cycle Asset Management is used to title this series, as it has the correct connotation of what is intended when the applicable strategies are adopted by organisations.
‘ISO 55001 Asset Management – Management systems – Requirements’ is an international standard for certification of life cycle asset management systems and posts about the ISO 55000 asset management suite of documents are included in this series.
The purpose of this Life Cycle Asset Management series is to provide reputed, useful content that brings value and improves asset performance when used in operations and organisations.
NOTE: The series does not include coverage of related commercial or vendor software or database management applications.
by Mike Sondalini Leave a Comment
PREVENTIVE MAINTENANCE STRATEGY IN A PLANT WELLNESS WAY EAM SYSTEM-OF-RELIABILITY
IN A PWW EAM SYSTEM-OF-RELIABILITY, PREVENTIVE MAINTENANCE STRATEGY IS TO REPLACE PARTS WHEN EXCESSIVE STRESS BUILD-UPS IN THEIR MICRO-STRUCTURE
by Mike Sondalini Leave a Comment
Full of new, powerful solutions, the Plant Wellness Way EAM methodology ensures operations and companies get to world class equipment reliability
Let a Plant Wellness Way EAM System-of-Reliability halve your Annual Maintenance Costs
People investigating the Plant Wellness Way enterprise asset management (PWW EAM) methodology want to know exactly what happens when they use it, especially how the analysis and implementation will be done in their own operation. A PWW EAM System-of-Reliability brings you three massive business advantages:
[Read more…]by Mike Sondalini Leave a Comment
Reliability is something that can be created. It is the result of the standards, processes, and practices that are used. By removing causes of failures and controlling the factors that allow their creation, you proactively eliminate failure events. By eliminating failures, you deliberately create reliability. The reliability creating processes in the Plant Wellness Way EAM methodology let any operation or site reach the heights of world class operating asset reliability.
[Read more…]by Mike Sondalini Leave a Comment
In the Plant Wellness Way EAM system-of-reliability methodology you set world class performance targets for every work task. You do that so the people doing the job know what world class work looks like. Then you ask them to find new, successful ways to deliver world class outcomes in the tasks they do. That way you guarantee world class success.
[Read more…][Read more…]We are facing difficulty in developing a definition of Critical Spare Part Inventory. No one is able to define it in its true essence. The situation is further confused with the difference to strategic spare parts. Any guideline or standard where we can find it ?
In the past, every Plant Manager had their own definition of Critical Inventory which changed with time. In optimization of Inventory, the first step is to establish a definition of Inventory considering all factors like production loss, redundancy, safety hazard, failure frequency, and of course, the lead time? Still I am stuck in this phase. I cannot progress, and don’t know what to do 1st, 2nd, and so forth to proceed further in this journey?
by Mike Sondalini Leave a Comment
In some industries, 40% of maintenance repairs result from original equipment manufacturing failures. And up to 35% of maintenance is traceable to design engineering mistakes. That totals 75% of maintenance costs during operation can be from prior life cycle process blunders
To get utmost operating plant and equipment reliability, you need to purposefully design and build your business processes to guarantee maximum reliability from each and every phase of the asset life cycle
[Read more…]by Mike Sondalini Leave a Comment
“Chance-of Success-Mapping” is probably the most revolutionary concept used in Industrial and Manufacturing Wellness. It is certainly one that will help managers most when they want the best choices for their organization
[Read more…]by Mike Sondalini Leave a Comment
This article outlines key concepts that an organization needs to be aware of to bring about optimal asset health by removing risks and managing their causes. The Plant Wellness Way EAM methodology focuses on the relationship between asset health and business performance. It contains the processes and analysis tools to develop a system-of-reliability that fully supports operating asset health for the greatest ROI from each asset throughout its life cycle.Risk is the total losses suffered when any asset’s components may fail. The causes of failure are the environmental and operating stresses that affect a component’s microstructure. This means that world class reliability is the effective, complete remove of the causes of failure, also known as risks, from your operations.
[Read more…]by Mike Sondalini Leave a Comment
Adopting the business strategy of intentionally tightening process and work quality standards will drive operating profits higher. You get most operating profits when process and work quality variables are sitting on their optimal cost points. The Taguchi Loss Functions of your operation show the connection between your operating costs and your process and work quality.
Keywords: Taguchi Loss Function, quality verses cost, Quality Cost Function
[Read more…]by Mike Sondalini Leave a Comment
Companies end rat-race problems fast and get world class reliability by using the simple Plant Wellness Way EAM methodology to slash operational risk and make your plant and equipment world class reliable
How to get a Plant Wellness Way EAM system-of-reliability that ends your Production and Maintenance rat race is shown in the image below. It’s a simple strategy and plan for building a truly effective life cycle asset management system that purposely replaces old production and maintenance rat-race causing systems.
[Read more…]by Mike Sondalini Leave a Comment
When calculating the replacement asset value fo items brought overseas, factor the effect of the difference in exchange rate into the calculation.
[Read more…]Ahmed asks:
How can we calculate replacement asset value (RAV) of a plant? We have 100’s of equipment in our three plants and we cannot contact 100’s of Vendors to tell us today’s equipment value. We have only the Capitalization Cost or installed historic value of assets.
The oldest plant was installed 6 yrs back (Aug 2015) for a total plant or asset value in our accounting record of 10 MMPKR. When the plant was installed 1 USD = 100 PKR and now after 6 yrs the exchange rate is 1 USD = 172 PKR. We took the capitalization cost of 10 MMPKR and calculated replacement asset value at today’s worth as 10 * 172/100 MMPKR.
by Mike Sondalini Leave a Comment
The Plant and Equipment Wellness Way lets organizations make their operating assets world class reliable so they can enjoy operational excellence success. A Plant Wellness Way EAM System- of-Reliability puts the reliability processes, skills, paradigm, and culture into companies that creates world class reliability and operational excellence.
[Read more…]by Mike Sondalini Leave a Comment
Written by Mike Sondalini as a memo to his younger self, the content has been adapted into an article format. Given the depth of detailed information contained, this article is better considered a technical document. It summarizes Mike’s key learnings from decades of research, consulting, and training in the Plant Wellness Way EAM methodology.
[Read more…]by Mike Sondalini Leave a Comment
The prime role of Maintenance is to reduce operating risk. Maintenance serves a business well when its use leads to lower production costs than using other choices that could have been taken. Too many managers think that they must maintain plant and equipment. Maybe you do and maybe you don’t. Maintenance is expensive and, as far as it is safe, use less costly answers. But if you do choose to do maintenance, then you ought to pick an operation’s maintenance strategy mix based totally on its effectiveness in delivering the least operating costs for the least maintenance cost.
[Read more…]by Mike Sondalini Leave a Comment
Making great choices that get world class reliability for your company is what you do with Plant Wellness Way Enterprise Asset Management methodology.