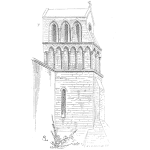
“Chance-of Success-Mapping” is probably the most revolutionary concept used in Industrial and Manufacturing Wellness. It is certainly one that will help managers most when they want the best choices for their organization
Every industrial and manufacturing business is a system. Each organization comprises interacting processes, people, knowledge, and physical assets. Figure 1 shows a simplified parts production system made up of processes. Figure 2 shows some of the sub-processes in the Manufacture step for making a mechanical machine part. Within each process are numerous tasks, each with their associated activities. The total of all activities in an operation can number in the thousands. So, how do you ensure all tasks are done ideally and every process delivers its utmost performance?


Figure 3 highlights that there are also external processes impacting on the core business. With numerous supply chain and outsourced operational processes involved in making a product.
To improve your business performance, you will need to work on the weaknesses in your own processes, and you will also need to go outside your company and work on the processes of your vendors and suppliers. You will need to make all the external processes excellent if you are to have operational excellence inside your company.
With system reliability engineering you can map the chance of success occurring anywhere in your company. Once you know the problems you have, and why you have them, you’re in the perfect position to know what solutions to use that eliminate your troubles forever.

To understand how business and work processes impact organizational success, you need to see the interconnectivity and the resulting interactions of all processes used across the business’ life cycle to engineer the plant, buy equipment and raw materials, make the product range, and run the operation. Process after process connects with others in a tangled web of interaction across time and space. There are dozens and dozens of processes containing task upon task. There are hundreds of tasks in most businesses; many companies have thousands of them. Companies with highly complex operations, such as constructing large industrial process plants, constructing big power stations, building spaceships or airplanes, have tens of thousands of activities to control.
Each activity in each task presents an opportunity for things to go wrong. Because each process feeds many other processes, any task error in one has a ripple effect that harms those downstream. A process that goes wrong that is not corrected can impact numerous others in the future. For example, a poor maintenance repair will cause a future production failure; an operator error that overloads a machine will lead to a future breakdown; the wrong choice of materials of construction by the designer of a gas-processing plant will contribute to a future explosion and possibly the death of people. That is why it is important for every step in a series process to go right every time—the future consequences are unforeseeable and can be devastating.
Like all organizations, this operation wants to make products it is proud to put its name too, as effectively and efficiently as possible. In the perfect world it makes 100% of its production right first time for the optimal least production cost. This would give the organization its largest margin and its largest profits. It would also mean it has a perfect safety record, a perfect environmental
record, a perfect employee retention history, along with perfection in all the other factors that
successful businesses want.
Perfection is a wonderful ideal. But in reality, what is the chance that any of an organization’s ideal outcomes are possible? That is where system reliability helps us. With its estimation methods you can understand what are your odds of having astounding business system success. Equally as important as knowing how close to perfection we are in what we do, we also want to know what must be changed in the business, and by how much to change it, when we want greater success.
Creating a more successful business means designing, then building, more successful processes. A successful process comprises correct inputs, effective tasks, knowledgeable people, and reliable machines working in concert. With the activities, equipment and processes in your company performing at world-class quality, world-class business results become natural. Measuring the chance of business process or work success requires statistics and probability math. Such math can be difficult, but you need only simple multiplication to see what chance you have of getting work and process success in your organization.
Reliability is formally defined as the odds that an item of equipment will last long enough to do its stated duty. It is the chance of a physical thing remaining totally usable until a particular point in time. Reliability can also be used to measure business system performance because it is simply the chance of successfully delivering a desired result. Anywhere you want a specific result in a process or a job, you can also determine the chance of the intended outcome actually happening.
The reliability of a series configuration is calculated by multiplying the reliability of each item in the arrangement. By using Formula 1 you can determine your chance of success from the steps in a process, and by using Formula 2 you can gauge the chance of success for any of the tasks done in any process step. As soon as the reliability of any item in the series drops to zero, the whole series goes to zero, and the entire system is failed, or a job is scrap. The underscore distinguishes work task reliability (R) from system reliability (R), which does not use the underscore.
Formula 1
RProcess = R1 x R2 x R3 x … Rn
Formula 2
RJob = R1 x R2 x R3 x … Rn
Formula 1 lets you identify where processes are weak, and Formula 2 lets you understand the circumstances when the tasks in a particular process has problems. With Formula 1 you can analyze the chance of success at any point in your business system, or at any point in any of your processes, or at any point in your supply chain processes, and even at any point in your suppliers’ processes. With Formula 2 you can spot the process tasks causing a problem and then dig down into them to understand why the tasks are delivering muck.
To do a job perfectly, every task must be 100% right. In a series process, such as doing a repair job, operating a production line, using a supply chain, or running a business, when there is a mistake in one step a defect is made or a problem is created, and the final outcome is wrong. This makes for a simple work reliability rule: the chance of job success is never greater than the chance of success for the worst-performed task. It’s the same with every series arrangement: “One poor, all poor; one bad, all bad” is a reliability mantra to remember. It explains why you can have constant production
quality problems—make one error anywhere in a series work process, and the finished item will be
If you want a company where great results are natural and excellence abounds, you need to ensure that your processes, jobs and machines are built to deliver excellence. Every step in every process, every task in every job, and every part in your machines need to go right all the time. That can only happen in the real world when your processes, work and equipment are designed to deliver the right outcomes every time they are used.
Based on systems engineering and system reliability improvement, Chance of Success Mapping is the ideal analysis technique for industrial operations, companies, and global enterprises, that want to design and use optimal business processes.
You can learn a lot more about Chance of Success Mapping from the Industrial and Manufacturing Wellness hardcover book. The hardcover book is available from the publisher’s website:https://books.industrialpress.com/9780831135904/industrial-and-manufacturing-wellness/ the ebook version is at https://ebooks.industrialpress.com/product/industrial-manufacturing-wellness.
The book is also at Amazon Books: https://www.amazon.com/Industrial-Manufacturing-Wellness- Mike-Sondalini/dp/0831135905/.
All the greatest chance of success to you, and to your organization,
Mike Sondalini www.plant-wellness-way.com
Leave a Reply