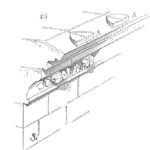
The new CRE body of knowledge goes into effect for exams starting January 2018.
The changes include topics that has been dropped, added, or altered. There also is a new structure with 5 main groups rather than the previous seven. Overall, the BoK remained pretty much the same with a reorganization of the topics.
Reading the new BoK and comparing it to the old BoK raises a few concerns or observations. Let’s take a look at the new structure and what the changes say about the reliability engineering profession. [Read more…]