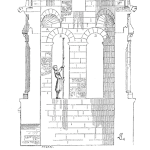
George Williams, CEO of ReliabilityX, providing insight on using Motion Amplification technology and its benefits.
[Read more…]Your Reliability Engineering Professional Development Site
by George Williams Leave a Comment
George Williams, CEO of ReliabilityX, providing insight on using Motion Amplification technology and its benefits.
[Read more…]by Nancy Regan Leave a Comment
Have you ever procrastinated? The struggle is real. I found myself in the web of fear and overwhelm…until I did this
by Sanjeev Saraf Leave a Comment
Chemical Facility Anti Terrorism Standard (CFATS) came into force on Nov. 20, 2007 as a Federal Regulation under 6 CFR 27. This set into motion the process of assessing threats to chemical plants and refineries in the U.S.
[Read more…]“I have a question,” stated the Chief Financial Officer. “The second data point from the right end of the line the drastically different than the others. How do you know that the line should be straight? Should not the cost line be curved between the last two data points?”
“Well, when we look at the correlation of the best-fit line with and without the point you reference, we obtain a nearly ideal fit when we treat the second point from the end as an anomaly,” stated the highly educated, high-brow consultant was discussing the agenda item before mine. His second sentence was equally long as he started launching into details about correlation and how the computer program cyphered through all of the data.
by Robert (Bob) J. Latino Leave a Comment
An undesirable event occurs (fancy term for unexpected failure) a Root Cause Analysis (RCA) is triggered. This usually means what occurred is a severe event as triggers are often set pretty high (i.e. – reportable injury/fatality, equipment damage in excess of x-thousands of dollars, production losses in excess of x-thousands of dollars, regulatory violation, etc.). Since there is urgency and visibility, how do I decide who will lead the investigation/RCA? Our natural tendency is to identify the technical ‘expert’ in the nature of whatever the undesirable event was. But does that typically produce the most effective outcome for the organization and its employees? This article will focus on which skills are needed most, under such conditions, and why
by Greg Hutchins Leave a Comment
Despite our collective educational establishments that purport to teach so that people can learn, ‘education’ is not necessarily learning. Mark Twain wrote disparagingly that “Education consists mainly in what we have unlearned” and also that he never let schooling interfere with his own education. Education is not necessarily knowledge and real learning comes from the application of theory tempered with experience which will make for better decisions and better outcomes. Benjamin Franklin’s words from over 200 years’ ago “Tell me, I forget. Teach me, I remember. Involve me and I learn” still ring true today.
[Read more…]by James Reyes-Picknell Leave a Comment
The gang talks about how to start building proper data, and the trials and tribulations in convincing other departments of your causes.
[Read more…]by Mike Sondalini Leave a Comment
“Chance-of Success-Mapping” is probably the most revolutionary concept used in Industrial and Manufacturing Wellness. It is certainly one that will help managers most when they want the best choices for their organization
[Read more…]I needed multivariate fragility functions for seismic risk analysis of nuclear power plants. I didn’t have any test data, so Lawrence Livermore Lab paid “experts” for their opinions! I set up the questionnaires, asked for percentiles, salted the sample to check for bias, asked for percentiles of conditional fragility functions to estimate correlations, and fixed pairwise correlations to make legitimate multivariate correlation matrixes. Subjective percentiles provide more distribution information than parameter or distribution assumptions, RPNs, ABCD, high-medium-low, or RCM risk classifications.
[Read more…]by Bryan Christiansen Leave a Comment
When designing equipment and processes, engineers leave a safety margin that ensures equipment remains functional when a fault or defect is affecting it partially or wholly. Minor defects affecting production assets should not cause immediate breakdowns. A fault-tolerant system remains operational for predetermined intervals before undertaking corrective measures. Faults affecting the operation of different systems emanate from more than a single source. [Read more…]
by George Williams Leave a Comment
by Sanjeev Saraf Leave a Comment
According to a recent report (Aug. 2008) from the Government Accountability Office (GAO), the Chemical Safety Board (CSB) is not in compliance with its statutory mandates. The CSB is an independent federal agency charged with investigating industrial chemical accidents and has been in operation since 1998. GAO report states that CSB is not investigating all chemical releases that have a fatality, serious injury, substantial property damage, or the potential for a fatality, serious injury, or substantial property damage. [Read more…]
The technician explained it to me like this: “The part costs only $5, but I need to disassemble other stuff to get to it, so my labor charge will be $300. But don’t worry, I replace lots of these.”
[Read more…]by Robert (Bob) J. Latino Leave a Comment
I used to be on Facebook many years ago in an effort to keep up with old friends. However, I began to realize the forum was often used to create an illusion that someone wanted their community to have about them. I knew many of these people creating such illusions, that is how I know they were ‘illusions’. Their ‘Facebook Family’ simply was not their reality.
This is not a paper about the pro’s and con’s of social media forums such as Facebook, but more about our propensity to create illusions, or prisms in which we want others to view our work initiatives. While I could apply this concept to many personal and business situations, I’m going to limit it to our general views of Reliability, Maintenance and to a degree Safety (as a by-product of effective Maintenance and Reliability).
[Read more…]“I just got through with a telephone call,” stated a concerned voice on the other end of the line. “We addressed the wrong issue. I am not saying you. It was collectively all of us. They wanted to sell all parts of the business unit and completely get out of that aspect. We addressed them retaining ownership but having someone else operate it.”
“That is not right,” I replied. “We solved the problem they wanted us to solve, and they bought off on it. “We can develop some solutions for the other problem, but that will take some time and effort.”
“How do you know we solved the right problem?” my client asked. “They have gone over everyone’s head and say we didn’t.”