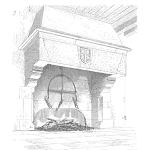
There might not ever be a better demonstration of the saying that …
… a fish rots from it’s head.
Boeing is responsible for the half-baked Maneuvering Characteristics Augmentation System (MCAS) that was forced into its new 737 Max aircraft. This involved a decidedly awful attempt to convince the Federal Aviation Administration (FAA) that there was no need to subject said aircraft through all the checks and balances that you need to go through if it is in fact a brand-new and different type of plane. Which it was. This resulted in the deaths of 346 passengers and crew (along with plenty of claims that it was pilot error). And just to be clear, Boeing has since admitted that it’s employees defrauded the FAA during the original certification process – an admission it was not required to make if it was able to complete a three-year period of increased monitoring and reporting. Which it could not.
Then there was the door plug that flew out the side of another 737 Max aircraft. The National Transportation Safety Board (NTSB) found that this was caused by a dysfunctional and chaotic manufacturing and assembly process where there was intense pressure to do things fast and for people to do things they weren’t trained to do. Boeing apparently isn’t sure which technicians were involved in bolting the door plug because there was no paperwork … at all. This is kind of a big deal in the aerospace industry.
These are two events that are very troubling in their own rights. But what is really troubling about both of these issues occurring in a relatively short period of time is that they have nothing to do with each other. The MCAS was all about design and certification. The door plug was all about manufacturing and quality control.
Then there is the ‘Starliner.’
What is the ‘Starliner?’
It is a crew capsule that is launched on a rocket that looks like that ‘flat cone’ many of us might recall from the command module of the Apollo missions. It can do things like take crews to and dock with the International Space Station (ISS) for a few months before safely returning to terra firma.
Or at least that is what it is supposed to do. The first (non-prototype) Starliner had all sorts of issues with it. Its first mission was supposed to take it to the ISS, but it never got to the right orbit and all the problems that were later uncovered meant that the mission was called a ‘high visibility close call.’ This means the Starliner was almost destroyed. The next attempt to launch was plagued with delays that lasted for over a year (with the rocket rolled out to the launch pad and back again twice) due to unexplainable issues with the propulsion system and valves. But it eventually did launch, dock with the ISS for four days (noting that two out of its twelve thrusters failed), and then returned to Earth.
The next Starliner (named the ‘Calypso’) was the first spacecraft used to take a crew up to the ISS and back again. But at the time of writing, it is only halfway to its goal. The Calypso is currently docked with the ISS with the crew on board. It was supposed to take them back to Earth after eight days, but they won’t. They will be staying there until 2025.
And that is because NASA has quite a few concerns about those thrusters that failed, and some other unexplainable helium leaks. This means that the Calypso will return to Earth without the crew, and another spacecraft (not from Boeing) will be launched to bring them safely home. This other spacecraft will be a SpaceX vehicle. Relying on a competitor to retrieve its stranded crew might be Boeing’s ultimate humiliation.
Let a few facts set in.
NASA contracted Boeing to design and build the Starliner with a 2017 deadline for its first successful crewed mission. It is now 2024, and even if the Starliner is able to take the crew back home it might not be called a ‘success’ based on the myriad of issues talked about above.
NASA signed contracts with Boeing and SpaceX to deliver very similar spacecraft. NASA paid $ 2.6 billion to SpaceX and $ 4.8 billion to Boeing. Funding has increased by $ 500 million for SpaceX and $ 600 million for Boeing. Some of the $ 500 million paid to SpaceX was to pay for more launches than originally planned. The $ 600 million paid to Boeing is … well … not for that. So there is a huge disparity between what the two companies are doing and what they are being paid.
SpaceX’s vehicle comes in two variants: the ‘Crew Dragon’ and ‘Cargo Dragon.’ As of today, they have successfully completed 13 crewed and 10 cargo missions across 7 still active spacecraft. Coincidentally, SpaceX’s oldest spacecraft (the ‘Endeavour’) is currently docked to the ISS.
But Boeing isn’t just building the Starliner. It is building the upper stage of NASA’s Space Launch System (SLS), which is an entire rocket. NASA’s Inspector General has just released a report that is both damning and becoming commonplace for Boeing. It goes through in great detail how the engineering and quality control for the SLS upper stage is nowhere near where it needs to be. There have been 71 ‘Corrective Action Requests’ issued in response to ‘deficiencies in quality,’ and Boeing has ‘generally been nonresponsive in taking corrective actions when the same quality control issues reoccur.’ To be clear, these are direct quotes.
And Boeing has also run up $ 1.5 billion in other development costs they weren’t planning on. And the SLS is likely to be much more expensive to launch than SpaceX’s Starship (which will be bigger, and reusable).
Now there are going to be some painful personalities out there who make legalistic points about the differences between what is being asked of the SpaceX and Boeing spacecraft. But that is like saying that a ‘sedan’ is different to a ‘sports utility vehicle (SUV).’ Technically this is correct, but it makes no meaningful addition to the conversation. The Starliner and Crew/Cargo Dragon are both vehicles that use the same technologies, dock with the same ISS, are about the same size, launch from the same planet and so on.
To cut a long story short … this is an embarrassing contrast between two comparable products that shows just how bad things are for Boeing and their long-suffering customers.
Boeing isn’t really in the business of making spacecraft
Boeing (as an entity) has a long history in helping make and launch spacecraft. And that probably had something to do with why they were awarded a contract by NASA.
But … that is all it is. History. Boeing’s aerospace engineers simply don’t have any experience in designing and building space stuff. The ‘long’ history Boeing predates the Apollo program which finished before most of Boeing’s current ‘senior’ engineers were even born. NASA’s Inspector General believes the issues Boeing is currently facing are …
… largely due to the lack of a sufficient number of trained and experienced aerospace workers at Boeing … The lack of a trained and qualified workforce increases the risk that Boeing will continue to manufacture parts and components that do not adhere to NASA requirements and industry standards …
Then there is SpaceX, who is manufacturing not just the Crew and Cargo Dragons, but all manners of rockets and other spacecraft. SpaceX was established with a single ‘space-centric’ mission. They recruited and built their own workforce and essentially funded many of their own projects that gave a brand-new swathe of junior engineers a whole suite of design challenges to sink their teeth into. They are now experienced and capable. SpaceX also has an approach of ‘testing to learn’ and not ‘testing to pass.’ They were only too happy to test prototypes to (sometimes catastrophic) failure to try and find out what to improve in their next design. And this daring approach (at least daring for the aerospace industry) has paid off big time.
Boeing on the other hand is very plodding and monolithic, which is something ‘big’ organizations can settle into when they don’t have much of a clue about what they are doing. Generic project management approaches and systems engineering practices simply cannot mitigate the fact that the engineers and other workers don’t know what they are doing.
Is Boeing still in the business of making aircraft?
This is actually becoming a shockingly relevant question to ask.
The issues NASA uncovered regarding the Starliner aren’t a million miles removed from the issues Boeing cultivated as it built the Boeing 737 Max. And these are two completely different lines of business with workers in different locations and hierarchies.
Perhaps the main difference between the part of Boeing that makes aircraft and the other part that makes spacecraft is that Boeing still has enough ‘aircraft savvy’ aerospace engineers that have the ability to (in theory) make good aircraft.
But … previous Boeing CEOs have openly acknowledged that Boeing has attacked, fired and otherwise punished whistle-blowers who were speaking out about issues that precipitated the 737 Max issues. The NTSB found out that Boeing still transfers ‘troublesome’ workers to a specific facility that focuses on manufacturing aircraft wings in what those workers call the ‘Boeing prison.’
Boeing has (mercifully) found a new CEO (Kelly Ortberg) to try and once again make Boeing a business that is in the business of making aircraft. And the issues we are talking about here are going to have a generational impact. The best and the brightest aerospace engineers are simply less interested in working with Boeing in its current apparition. This will leave a dearth of emerging talent for the next five to ten years, even if Boeing was somehow able to magically fix it’s culture today. There will be a much longer impact in middle management and leadership positions.
How to fix this?
This is where the patented ‘six step process’ to magnificence kicks in? Nope. The problem when the same toxic problems across an entire organization, regardless of what everyone is doing, is that it (by definition) has to be a leadership problem.
There is a pervasive culture that needs to be resolved. This is not impossible, but is going to be very challenging. It will come down to the ability of Kelly Ortberg to communicate a simple strategy that is digestible from top to bottom. This strategy needs to be unambiguous and expose poor behaviour and poor actors. Then there will be a need to remove a large portion of ineffective or toxic leaders quickly. For an organization as large as Boeing with a problem that has been festering this long, this won’t be something Ortberg can do on his own. And so his ability to quickly surround himself with a trusted cadre of like-minded leaders while being somehow able to fend off a rabid NASA, FAA, NTSB and mob of politicians will be absolutely critical.
But perhaps the best way to ‘fix’ this is to never allow it to happen in the first place. And this is where there may be a lesson that might apply to your organization.
Organizations where leaders are the ‘most important caste’ of people are doomed for failure. Of course, a positive leader can have a disproportionately large positive effect on his or her organization compared to a single lower-level employee. But it is the ‘caste’ that matters. The most important characteristic of a ‘good’ aircraft manufacturing company is the ability of its employees to be ‘good’ at designing and building aircraft. And the leaders (like Ortberg) need to make that the primary focus moving forward.
And when your organization loses its ability to do its ‘as advertised’ business, it often quickly replaces that lost ability with process, ineffective leaders (who can sometimes still look slick and imposing in suits), a focus on immediate profits at the expense of long-term profitability and lots of other bad things.
So to stay in business, keep your business in the business of whatever it is you say your business is (yes, the word ‘business’ was used four times.) Because not every business is ‘too big to fail’ like a number of people say Boeing apparently is. Admittedly, that number is being revised down each day. So watch this space …
‘testing to learn’ and not ‘testing to pass’. I like this.
I wish I could claim that I can’t up with this, but I can’t! I think Fred owns the trademark for that one. It’s a good one.
Why do we need a “testing to learn” if we need to get a type certificate (‘testing to pass’)?
… because before you can ‘pass’ a reliability test, your product needs to be reliable. And this only happens when you ‘learn’ what the weak points are that for need to design or if your products and manufacturing processes. If you only ever have tests that you need to ‘pass,’ failures are ‘pretended’ away