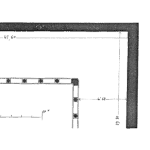
Do you need design margin in your product? A composite frac plug may need margin as a mitigation against uncertainty in material properties. Long service life products used in offshore wells are sometimes designed with structural margin as a mitigation against changing downhole conditions. But can margin be used for other parameters?
Margin mitigates against application uncertainty and is the difference between an assembly rating and operating limit, established through calculations, simulation, or lab testing. For example, the operating limit for a downhole sealing device is determined under laboratory conditions, and the result is assumed to be valid over a long service life downhole. But the downhole environment is not ideal and can reduce performance, so applying a margin to the test result is prudent. Margin may also be known as “derating.” A method of deration used by upstream operators is the “80% rule”. This reduces the OEM rating by 20%, and well operations are planned using the reduced rating.

Engineers use factors of safety (F.S.) and ASME load factors in component design, but assembly margin should still be used. Margin can also be used in these situations:
- Electronic and electro-mechanical assemblies. Use a thermal margin between the lowest component rating and the peak assembly operating temperature to increase service life, and derate service life hours or cycles to schedule repair or replacement before failure.
- Nonmetallic materials. The temperature rating of an elastomeric material is affected by different environmental factors. Using a thermal margin between the material temperature rating and the OEM rating for the elastomeric seal will increase service life.
A thorough discussion of margin requires far more than one page. Margin is not used as frequently as it should be, particularly for products in critical downhole applications. Not all products require margin, but margin helps all products survive application uncertainties.
TRUTH: Margin mitigates against application uncertainty.
This is the 4th of six articles on Design for Reality for downhole tools and systems.
Leave a Reply