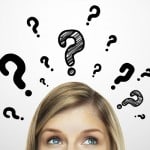
FMEA Q and A
Ponder this question: Let’s say you are an OEM and assemble parts made by various suppliers. When performing your Process FMEA, do you consider special characteristics for components in your Process FMEA? This question is discussed and answered in this edition of FMEA Q and A.
“The key to wisdom is this – constant and frequent questioning, for by doubting we are led to question, by questioning we arrive at the truth.”
Peter Abelard
Reader’s Question
I do not introduce special characteristics for components in Process FMEA because we have to consider that the component’s that we are buying have to be according with drawing specifications and we are not influencing it in our process.
Those special characteristics are treated in Design FMEA and Control Plan.
Could you tell me your opinion about this?
Answer to Reader’s Question
This is an excellent question.
You are correct that you are not influencing the specifications of a purchased part during your assembly process. In many cases, Process FMEA teams assume that supplier components are in accordance with drawing specifications. However, there are exceptions to this assumption, which I will outline with an example.
Let’s say company A manufactures fuel delivery subassemblies, and they purchase fuel line quick-connects from supplier B. Let’s further say that company A is conducting a Process FMEA on their assembly process for the fuel subassemblies. Here’s the general rule about incoming parts:
Process FMEAs typically assume the design requirements are correct and incoming parts and materials to an operation meet design intent. In addition, the PFMEA team may wish to consider an exception when historical data indicates incoming part quality issues: incoming parts or materials may have variation and do not necessarily meet engineering requirements.
With regard to the quick-connect incoming parts from supplier B, company A now has a choice. They can assume the parts they receive from supplier B meet specifications. However, they can make an exception to that assumption. If the quick-connect device is critical to their fuel subassembly and they have reason to believe that the device may not meet requirements, they can consider this exception: incoming parts or materials may have variation and do not necessarily meet engineering requirements. Historical data for quick-connects or fuel sub-assembly risk analysis may indicate this exception. If the fuel subassembly Process FMEA team wishes to make this exception and not assume the incoming quick-connect device meets specifications, they may need to add a step or two to their manufacturing process, or modify existing steps.
Let’s trace this progression from the viewpoint of special characteristics.
One possible special product characteristic for supplier B’s quick-connect is “inside diameter of the connecting device.” Supplier B would make this a special product characteristic, and identify associated special process characteristic(s) that are needed to control the inside diameter during the quick-connect manufacturing process. As you point out, those special characteristics are treated in the supplier’s DFMEA and Control Plan. The final quick-connect product should meet dimensional and performance specifications before shipping to company A for use in the fuel system assembly. If company A is concerned about this special product characteristic (inside diameter of connecting device), and if they choose to make an exception to the assumptions about this incoming part, they can consider changes to their assembly process to accommodate this exception. Changes might include measuring the inside diameter, or modifying the process controls to detect and accommodate inside diameter variation. They can also recommend action that improves the quality of supplier B’s quick-connect device. In addition, they can request that the design team consider modifications to the fuel subassembly design to be more robust to anticipated variation in quick-connect inside diameter variation.
Next Article
Failure modes and their causes can be detected in service, like tire pressure monitors on your vehicle. Is that what is assessed in the Detection column of the FMEA? The next article discusses the subject of detection risk, including examples, and answers this question.
In general, it is appropriate to consider that all upstream processes meet requirements when doing a pFMEA for a particular process step. One of the reasons is that upstream processes should have had an FMEA done on them that would have identified any failures that would affect the current step.
Hi Duke,
Thanks for offering your comments to the discussion.
I agree that in most cases, the PFMEA team considers upstream processes, such as supplier parts, meet requirements.
However, as I mention in my article, “the PFMEA team may wish to consider an exception when historical data indicates incoming part quality issues: incoming parts or materials may have variation and do not necessarily meet engineering requirements.”
This is consistent with SAE J1739, which says “ln preparation for the PFMEA, the assumption may be made that incoming part(s)/material(s) are correct. Exceptions can be made as experience dictates (e.g. known deficiencies in incoming part quality).”
Do you agree that the PFMEA team can make an exception to the general rule when data warrants, or do you think the rule should allow no exceptions. I’d be interested in your opinion.
Thanks.
Carl
Hi Carl,
Even if the process FMEA team wishes to assume that the incoming quick-connect device meets specifications, could it be a good idea to pull special characteristics though and show them in the PFMEA to make downstream users aware of the special nature of certain features? This may help avoid things like the quick-connect being installed by inserting a tool into the critical ID and using that ID to turn or push the part into place. Supplier components may arrive within specification, but if handled incorrectly due to lack of awareness, they could be damaged.
Thanks,
Jay
Hi Jay,
I think you are making a good point.
If the supplier part has product characteristics that are significant to operation, even if the characteristic is within specification, damage to the part by the assembly plant, or downstream user, can create a failure.
My preference would be to address this type of issue with error proofing. For a critical part, if there is concern about correct handling, the process team can consider error proofing the process to ensure there is no damage due to incorrect handling. This can be considered in the PFMEA and the Process Control Plan. If the concern is with user handling, the team can consider error proofing the user operation.
Thanks.
Carl
Hi Carl,
Auditors like to ask for special characteristics that shall be taken over from Design-FMEA into Process-FMEA. For mechanical design I found many examples und understand this approach. But I am working on electrical design FMEAs and there nobody was able to tell me so far, what should be the special characteristics. Do you have any hint for me?
In EE design features of components are defined by the components we use and these components have unique part numbers. So features are determined by Design and Process can’t do anithing about it. On the other hand key features are tested 100% anyway, so there is nothing special about it.
Thanks for any replay,
H. A.
Hi H.A.,
Excellent question! Having done a number of electrical DFMEA projects that provide candidate significant product characteristics, I can say the following. The key to determining the right significant product characteristic, with the use of DFMEA, for any electrical of mechanical part is to correctly describe the cause as a potential design deficiency. Here is an example. For a thermo-statically controlled heater switch, one cause of the failure mode “switch stays open” is “thermostatic switch under-rated for the required usage (rated at 30 V DC in 65 V DC application).” The corresponding special characteristic is “switch voltage rating.” The Process FMEA would need to ensure this special characteristic is met, either by controlling the manufacturing process of the heater switch, or in the case of an assembly plant, by ensuring the incoming part meets this special requirement.
Please let me know if this answers your question.
Thanks.
Carl
Hola
What about the scope among the
Design-FMEA into Process-FMEA
In food items?
How to answering correctly each flow chart step regarding control plan?
Hello Alejandro,
FMEA procedure applies very well to food processing.
If you have a copy of my book “Effective FMEAs,” I summarize a case study which uses FMEA and Hazard Analysis for a food processing project in section 8.2 (pages 190 to 193). Essentially, you start with a Process Flow Diagram, including “Critical Control Points.” You can then use FMEA and Hazard Analysis Critical Control Point (HACCP) to generate the critical control points that are input to the Process Control Plan.
For information, this case study was published in “International Journal of Food Science and Technology,” 2007, Vol 42 pp 1156 – 1176.
Please feel free to ask any follow-up questions, or email me at carl.carlson@effectivefmeas.com.
Carl
Hi Carl,
Thanks for your replay.
Staying with your example: We would specify the rated voltage by design and design team would also choose a heater-switch that fulfills this needs. So in our drawing the heater-switch is already defined by a part number.
For the production of course they have to use the correct heater-switch with the correct part number. But my question is: What is special to the production now? They have to use the component specified by design.
Thanks for any comment.
Best regards,
H. A.
Hello H.A.
In this hypothetical example of a heater switch, we stated that the special *product* characteristic is “switch voltage rating.” The Process FMEA can identify the corresponding special *process* characteristic. What special characteristic in the manufacturing or assembly of the heater switch needs to be controlled to ensure the switch voltage rating is met? Both the special product and process characteristics are central to the Process Control Plan for the switch supplier. This is in addition to using the correct heater-switch with the correct part number, as you point out.
Hope that helps.
Carl