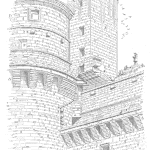
Before Norris-Landzberg’s study there was the work of Coffin and Mason.
Coffin-Manson
One way to approach accelerated life testing is to use a model for the expected dominant failure mechanism. One such model is for solder joint low-cycle fatigue originally published by Coffin (1954) and Manson (1953), independently.
Norris-Landzberg
Norris and Landzberg proposed the plastic strain range is proportional to the thermal range of the cyclic loading (ΔT). They also modified the equation to account for effects of thermal cycling frequency (f) and the maximum temperature( T). They and other than empirically fit the parameters for the equation.
$$ \large \displaystyle AF=\frac{{{N}_{field}}}{{{N}_{test}}}={{\left( \frac{{{f}_{field}}}{{{f}_{test}}} \right)}^{-m}}{{\left( \frac{\Delta {{T}_{field}}}{\Delta {{T}_{test}}} \right)}^{-n}}\left( {{e}^{\frac{{{E}_{a}}}{k}\left( \frac{1}{{{T}_{\max ,field}}}-\frac{1}{{{T}_{\max ,test}}} \right)}} \right) $$
where,
‘field’ and ‘test’ stand for use or field and test conditions respectively.
Ea is the activation energy
k is Boltzmann’s constant
Ea/k for this equation is 1414
The fitted parameters m and n have been determined for SnPb eutectic solder to be 1/3 and 1.9 respectively. [Norris-Landzberg] A recent paper suggests the same formula and parameter values applies for lead-free (SAC) solder as well. [Vasudevan and Fan]
What does it do?
Understanding the temperature range of the use conditions and setting up a suitable test condition, permits translating the testing results to predict the field lifetime for the solder joints.
The model provides a basis for test design and estimating the duration of the testing suitable to replicate the field lifetime duration of interest. While not perfect, it does build on a lot of excellent work accomplished previously and significantly shortens the time and expense to estimate the time to failure distribution for solder joint fatigue.
Coffin, Jr., L. F. Trans.ASME, 76, 931–950 (August 1954).
Manson, S. S. Proc. of Heat Transfer Symp., Univ. of Mich. Press. 9–76 (1953)
Norris, K C, and AH Landzberg. “Reliability of Controlled Collapse Interconnections.” IBM Journal of Research and Development 13, no. 3 (1969): 266-271.
Vasudevan, Vasu. and Fan, Xuejun. “An Acceleration Model for Lead-Free (SAC) Solder Joint Reliability Under Thermal Cycling.” 2008 Electronic Components and Technology Conference.
Related:
Hypothesis un-equal variance (article)
Equal variance hypothesis (article)
Reliability Growth Testing (article)
Is this equation correct ? should ‘m’ be positive
In some equation presentations the field and test are inverted for this ratio, thus m would be positive. I like having the field variables on top over the test variables… for not particular reason other than I can remember the equation that way and make fewer mistakes.
I understand the point about -m coefficient which basically “flips” the two parts of the equation.
However, I am looking at the original Norris-Landzberg article, where the (only) frequency ratio is flipped, while the temperature is not.
In some articles (e.g. Vasu Vasudevan and Xuejun Fan, “An Acceleration Model for Lead-Free (SAC) Solder Joint Reliability under Thermal Cycling “) the ratio is the same as here, while still the original Norris-Landzberg article is being quoted.
In other (e.g. Andrew E. Perkins and Suresh K. Sitaraman, “Solder Joint Reliability Prediction for Multiple Environments”) the ratio is the same as in the original article.
Any idea where this difference is coming from?
I too have noticed the different ways to express the relationship and do not know the rationale or reasons for the differences. I suspect it has to do with individual authors preferences. cheers, Fred
In the case where the accelerated value is on top with a positive exponent, the frequency portion of the equation is stated in terms of the dwell time so…f,t = 1/tdwell,t & f,f = 1/tdwell,f.
therefore the the term then becomes (tdwell,t/tdwell,f)^(1/3) which ends up being that both the frequency term and temperature term have the test value on top with a positive exponent.
also, be careful about the ratio being exponentiated… if reverse the sign of the exponent changes.
Can someone explain when you should use the Norris-Landzburg or just use the Coffin Manson?
Hi Alfred,
From what I understand Coffin Manson is a general relationship for crack propagation in metal, whereas the Norris Landzberg relationship is specific to solder joints.
hope that helps
Cheers,
Fred
Second main issue with this formula is about the factor Ea/k (1414). Why the activation energy 0.121 is taken into account (0.121/0.0000862). I have never seen any Semiconductor device failure mechanism which can give Ea as 0.121.
Even the dielectric breakdown failure can have 0.2 (not below that)
Best ask Norris or Landzberg the question, yet keep in mind that they analyzed hundreds of accelerated life tests and field failure analysis reports and empirically fit the equation finding the parameters. Form of the equation using what appears to be the Arrhenius equation is a very flexible format to fit a curve, it may not have a basis in chemistry in this case. Yet there seems to a relationship related to temperature exposure to some degree. cheers, Fred
Can the Coffin-Manson model be used to predict an adhesive joint life acceleration factor (AF)?
Hi Bill,
I would suspect the form of the equation may describe the relationship between the applied load or stress and failure, yet the constants most likely will change.
In general, for acceleration models, they were created for a specific failure mechanism and material set and range of stresses – going outside that region is likely to result in misleading results. Much better to run a multiple stress level ALT and determine the appropriate model to describe the relationship between stress and time to failure.
Cheers,
Fred
Two questions:
Have you all come across a good source for activation energies to use for different solder types (both SnPb and Pb free) that are acceptable to use for estimating AF with the Norris-Landzburg equation?
Many articles/resources I have read refer to the same fitting parameters (m and n) as shown in this article (1/3 and 1.9). Is there a good source for alternative values for n?
Hi Jonathan,
Yes, many resources use 1/3 and 1.9 along with appropriate activation energy. The fitting parameters are based on both a compilation of test data and ongoing testing of new solders and geometries. While some papers report slight variations, overall for most systems the 1/3 and 1.9 are suitable for many situations.
A literature search may reveal alternatives for your specific situation (materials and geometries and stress patterns) or it might not. You could also conduct a more elaborate set of tests to determine the fitting parameters directly, yet that will take multiple sets of stress application conditions along with sufficient samples in order to generate enough data for the regression analysis.
For activation energy, a great source is a material scientist or chemist – second is your own detailed test data, and third is a literature search. Back when I was at HP and lead-free solders were coming to market we did a lot of solder joint fatigue testing as did many others. Over time we all found that the lead-free (SAC) and tin-lead solder of old used the same set of fitted parameters in the modified Norris Landsberg model. The two solder systems have similar yet fundamentally different paths to failure (SAC needs a longer dwell to accumulate equalivant damage per cycle, for example of just one difference that affects testing) yet the N-L model remains pretty much the same.
There has been and continues to be a lot of research into solder joint fatigue, so I suspect there is new information out there that I am not aware of at the moment. So, other than general advice I do not have a good source for alternative fitting values.
cheers,
Fred
Thank you very much for the response.
Follow up question: I have observed other sources using different signs for m and n and ratios of field to test that don’t match the formula shown here. E.g. This article and other sources show (Ffield/Ftest) w/ – n and (Tfield/Ttest) w/ -m or
(Ftest/Ffield) w/ +n and (Ttest/Tfield) w/ +m
I have now found two articles that are different. Case 1: uses (Ffield/Ftest) w/ +n and (Tfield/Ttest) w/ -m. Case 2: uses (Ffield/Ftest) w/ +n and (Ttest/Tfield) w/ +m. I recognize Case 1 and Case 2 are equivalent, however Case 1 and Case 2 are not equivalent to the primary formula shown in this article.
Is there a good explanation as to why there are different ratio/signs used for different sources? Could this be an error? Am I imagining things!!?
https://web.calce.umd.edu/lead-free/SMTAI2018-Osterman.pdf
https://www.test-navi.com/eng/research/handbook/pdf/05_2_handa_C0906_en.pdf
Thanks you very much for your insights.
Hi Jonathan,
I think you are right…I went back and checked the references you mention and the original Norris and Landsberg references and a few others. It seems the paper I pulled from [Vasudevan and Fan] did have the notation incorrect.
Good catch, thanks for letting me know.
Also, the two sites you mention provide excellent examples and detailed experimental results – thanks!
cheers,
Fred
Fred,
I guess Intel Vasudevan and Fan’s expression is correct and a correction to a typo (I guess in Norris-Landzberg’soriginal publication) with sign of n. Since f_field is less than f_test, so Norris-Landzberg’s original expression (f_field/f_t)^0.33 will be less than 1. That means higher test temp ramp rate will lead to longer solder fatigue life, which is against material physics. The expression from Vasudevan & Pan (f_field/f_t)^-0.33 gives higher than 1 value and that aligns with material physics that higher temp ramp/down rate will lead to shorter fatigue life cycle. Vasudevan&Pan was not simply changed sign of n, but tested the sign of n with Intel’s DOE data.
HI Larry,
updated – thanks for the info
cheers,
Fred
I am new to reliability evaluation in PCBs and part of my current project involves predicting service life of a PCB assembly from accelerated life testing. From what I’ve been able to gather so far, the NL model is more appropriate for SnPb solder under thermal cycling where the service life = number of test cycles * AF. I gather this is true when there is no failure after ALT.
How should one proceed with life estimation when there is a failure. For example in my case, the PCB assembly was first vibration tested before thermal cycling. Or is the NL model strictly for thermal cycling tests?
Thanks in advance for your response.
Hi Olu,
PCBs (I’m assuming you mean a circuit board with solder attached components) is a complex system and has many potential failure mechanisms. NL really only applies to solder fatigue due to thermal cycling – and the specific NL model and results may vary depending on the type of solder attach under considerations (BGA, gull wing, leadless, etc)
The components themselves may also fail internally for many reasons. The board itself has a bunch of potential failure mechanisms.
The first step is to understand what is at risk of failure in the timeframe of interest then design your ALT. Conduct ALT on specific failure mechanisms – those that are known to potentially fail during the use timeframe, or have an unknown behavior over the timeframe of interest.
ALT provides much better results if there are failures – no failure testing is risky, as you lack confirmation that the applied stress actually will lead to the expected failure mechanism. Also, keep in mind that different mechanisms may respond to applied stress in different ways and rates.
ALT on a common PCB with dozens or hundreds of components is very difficult to do in a meaningful manner. I recommend starting with either an FMEA or Fault Tree analysis to identify the specific failure mechanisms on interest before proceeding to ALT design.
cheers,
Fred
Hello Fred,
I have query wrt to the Humidity Stress (if) applied along with the temperature cycling (humidity applied during +ve temperature dwell time) then whether the above Norries Landzberg model can be modified to take into account the acceleration factor due to humidity stress also? If yes, how ?
Thank you
Pukhraj
Hi Pukhraj,
I do not know of such an acceleration factor formula. What is the failure mechanism at play here?
Humidity on its own is difficult to accelerate as you need to apply increased pressure to increase the moisture content beyond what is the normal range in one atmosphere.
You may need to design a test to create the acceleration factor formula if you don’t find anything in the literature for the specific failure mechanism of interest.
cheers,
Fred