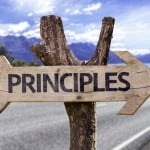
Leveraging the Value of Today
A common error in FMEA procedure is to make entries in the Controls column that the FMEA team believes need to be done, but are not currently planned or in place. Why is this error so prevalent? Maybe the question should be why do we limit entries into the prevention or detection control column to actions or methods that are currently planned or in place?
“Never mind your mistakes. One day they will become your most prized possessions.”
Abhijit Naskar
Definition of “Controls”
The Oxford English dictionary defines “Controls” as “a means of limiting or regulating something.”
What is the definition of “Controls” in an FMEA?
“Controls” are the methods or actions currently planned or already in place to reduce or eliminate risk. Controls can be the methods to prevent or detect the cause during product development, or can be actions to detect a problem during service before it becomes catastrophic.
Prevention-type design controls describe how a cause, failure mode, or effect in the product design is prevented based on current or planned actions; they are intended to reduce the likelihood that the problem will occur, and are used as input to the occurrence ranking.
Detection-type design controls describe how a failure mode or cause in the product design is detected, based on current or planned actions, before the product design is released to production, and are used as input to the detection ranking. Detection controls are intended to increase the likelihood that the problem will be detected before it reaches the end user.
Prevention-type Process Controls describe how a cause, failure mode or effect in the manufacturing or assembly process is prevented, based on current or planned actions. They are intended to reduce the likelihood that the problem will occur, and are used as input to the occurrence ranking.
Detection-type Process Controls describe how a failure mode or cause in the manufacturing or assembly process is detected, based on current or planned action, before the item is shipped from the manufacturing or assembly plant, and are used as an input to the detection ranking.
How are Controls identified in FMEAs?
The Design or Process FMEA team should consider what actions or methods are currently planned or in place that meet the definition of prevention or detection controls. Discussion should be limited to those actions or methods that will take place without anything being done differently by the FMEA team. If the FMEA team believes that something needs to be done differently, they should recommend the actions as part of the FMEA.
Why is it important to limit entries in the Controls column to currently planned actions or methods? Because the occurrence ranking depends in part on the entries in the prevention column, and the detection ranking depends on the entry in the detection controls column. Putting actions or methods in these columns that need to be done differently will skew the risk rankings, and miss out on the project-management benefits of Recommended Actions, such as person responsible and target completion date.
What is an example of Design FMEA controls
Item: Power steering pump
Function: Delivers hydraulic power for steering by transforming oil pressure at inlet [xx] psi) into higher oil pressure at outlet ([yy] psi) during engine idle speed
Failure Mode: Inadequate outlet pressure (less than [yy] psi)
Effect (Local: Pump): Low pressure fluid goes to steering gear
Effect (Next level: Steering Subsystem): Increased friction at steering gear
Effect (End user): Increased steering effort with potential accident during steering maneuvers
Cause: Fluid incorrectly specified (viscosity too low)
Prevention Control: Design guidelines for hydraulic fluid selection
Detection Control: Vehicle durability test #123
What is an example of Process FMEA controls
Process Step: Induction harden shafts using induction hardening machine
Function: Induction harden shafts using induction-hardening machine ABC, with minimum hardness Brinell Hardness Number (BHN) “X”, according to specification #123.
Failure Mode: Shaft hardness less than BHN “X”
Effect (In plant): 100% scrap
Effect (End user): Potential shaft fracture with complete loss of performance
Cause: Induction machine electrical voltage/current settings incorrect for part number
Prevention Control: Shaft hardening setup instructions
Detection Control: audit of shaft hardness
Application Tip
When identifying controls to enter into your FMEA, it is important to realize that these are the currently planned controls, not controls that have yet to be established or that will be changed. The idea is to list the controls that are in place or will be used if no changes are made to current program plans. If the FMEA team wishes to add, modify or delete design or process controls they should use the recommended action column.
If no prevention or detection controls are applicable for a given failure mode/cause, the FMEA team should leave the corresponding column blank.
Next Article
In the next article, we use problems and solutions to learn about FMEA controls. In one of the problems, we continue examining the door latch-pin failure of the DC-10 cargo door, as an example to identify FMEA controls. In the advanced problem, we analyze a fictitious FMEA relating to potential safety of someone trying to unjam a snowblower.
If I prepared work and displayed ,Can consider it as prevention control?
Hello Mahesh,
It depends on what you mean by “prepared work and displayed.” If your question is if you perform preparation tasks as part of the product design process, and the preparation tasks relate to the failure mode and associated cause in the FMEA, the answer is “yes.”
How can I link the prevention controls identified in the PFMEA with the control method column in the Control Plan?
Hi Victor,
You are correct that Prevention Controls in the PFMEA are input to Control Methods in the Process Control Plan. Same with Detection Controls. The PFMEA team uses engineering judgement to make this linkage. There may be relational database software that does this automatically; but I prefer this to be a manual linkage, to allow engineering judgment to guide the transfer of information.
Carl
Hi Carl, thank you for an informative article. I have a specific query.
A shaft is inserted in the hole with inference fit and pull out of the shaft from the hole is considered failure of severity 10, now if I change the design and include a secondary safety that can delay the failure mode but not eliminate it for example I insert a circlip to delay the pull out. In this case, can I reduce the severity of the failure mode, As I have designed a preventive mechanism to delay the failure mode.
thank you for help.
Hi Sandeep.
Thanks for your question.
As always with evaluating an FMEA, we have to begin with an understanding of the item being evaluated. I’ll assume for the purpose of answering your question that the revised design is a type of external circlip that is placed around the shaft exerting force inwards to prevent slippage of the shaft. If that is the case, the function would be described accordingly, and a possible failure mode might be shaft pulls out. If the consequence of the shaft pulling out is severe, then the severity stays high. You may have impacted (reduced) the likelihood of occurrence, by the addition of the circlip. Remember, prevention controls can affect the occurrence rating.
Let me know if I have answered your question and if there are other considerations.
Thanks.
Carl