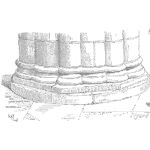
For a stable process, nothing much happens. If the stable process is producing acceptable products, we should expect to continue to produce acceptable products.
Unless something changes.
A change in material handling, equipment setup, tool breakage, sensor malfunction, etc. all can cause a formerly stable process to no longer produce acceptable products. Control charts are the tool to detect when the process becomes out of control.
Out of control by itself doesn’t mean the products produced are bad, it means the process is no longer stable. It means something has changed (most likely something has changed).
When something changes, if we catch the change and why or what caused the change, we can either make improvements or incorporate improvements. Replace a worn tool with a new one, or continue doing an improved material handling step. Not all changes are bad, some we will want to keep.
Shewhart ‘out of control’ rule
Identify an out of control condition if and only if you plot a point beyond the plus or minus 3σ control limits.
Given that the control limits only encompass 6σ of the distribution, there are about 0.3% samples from a stable process that would fall outside the control limits. We would expect 371 points on average before a ‘naturally’ occurring out of control point.
Western Electric Company rules (WECO)
- Rule 1
Any single data point outside the 3 σ limit from the center line. - Rule 2
Two our of three consecutive points fall outside the same 2 σ limit from the center line. - Rule 3
Four out of five consecutive points fall outside the same 1 σ limit from the center line. - Rule 4
Eight consecutive points fall on the same side of the center line.
Basic probability helped form the WECO rules. We know that, for a normal distribution, the probability of encountering a point outside ± 3σ is 0.3%. This is a rare event. Therefore, if we observe a point outside the control limits, we conclude the process has shifted and is unstable. Similarly, we can identify other events that are equally rare and use them as flags for instability. The probability of observing two points out of three in a row between 2σ and 3σ and the probability of observing four points out of five in a row between 1σ and 2σ are also about 0.3%.
False alarm
While the WECO rules increase a Shewhart chart’s sensitivity to trends or drifts in the mean, there is a severe downside to adding the WECO rules to an ordinary Shewhart control chart that the user should understand. When following the standard Shewhart “out of control” rule (i.e., signal if and only if you see a point beyond the plus or minus 3 σ control limits) you will have “false alarms” every 371 points on the average. Adding the WECO rules increases the frequency of false alarms to about once in every 91.75 points, on the average.
WECO rules provide additional means to detach a meaningful shift in the process. It is through detection, investigation, and improvement that control charts add value.
Related:
Statistical Process Control Overview (article)
Chance of Catching a Shift in a Control Chart (article)
Special and Common Causes of Process Variation (article)
Leave a Reply