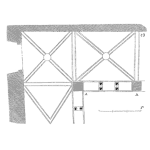
Eric Lof was born and educated in Sweden, moved to the United States in 1902, and worked for the Western Electric and General Electric Companies. Eric Lof published a series of articles on hydroelectric plants in 1913 in the Engineering Magazine. The Engineering Magazine helped spread the concepts of planning, efficiency, and scientific management. The magazine, for example, published the first Gantt charts in 1910.