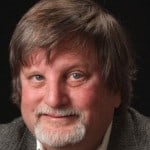
Vendors and Reliability
Abstract
Kirk and Fred discuss the value or risks of sending failed components to the vendor for failure analysis.
Your Reliability Engineering Professional Development Site
by Greg Christensen Leave a Comment
Mina Soliman joins Greg on CMMSradio for a wide-ranging discussion covering maintenance, reliability, and cultural perspectives. Mina expressed his anticipation for the Reliable Plant and Machinery Lubrication Conference in Chicago (June 3-6, 2024), emphasizing the collaborative environment it fosters.
We talked about he potential pitfalls of prioritizing asset management over reliability, stressing the interconnectedness of both aspects. He touched upon cultural differences in how organizations approach these concepts and the need for a balanced perspective.
The growing recognition of certifications in the maintenance and reliability field, noting how cultural attitudes towards certifications are evolving, is important to Mina. He highlighted the increasing value placed on certifications by companies and individuals, reflecting broader shifts in cultural perceptions within the industry.
The conversation stresses the importance of cultural understanding and collaboration in the maintenance and reliability field and throughout all of industry.
In the fun questions segment Mina shared his fondness for jazz music and his passion for fishing, particularly in the diverse waters of his region and the international fishing championship in the Red Sea!!
Keep an ear out for Mina’s perspectives on work-life balance, emphasizing the need for effective time and priority management to maintain this balance.
by Greg Christensen Leave a Comment
We had John Morris, of Club Colors, on CMMSradio to discuss his experience and insights around the importance of operational excellence and how purpose over product – and PEOPLE – are at the center of pretty much everything. Look out for the segment on error rate reduction (very CMMS and maintenance centric).
John was one of our inspirations for starting the podcast – He’s an expert-level podcaster with a passion that shines through.
Here are the main topics:
by Greg Hutchins Leave a Comment
Greg and Fred discuss how AI is changing work, careers, and jobs. Last week, Fiverr CEO warned staff: ‘AI is coming for your jobs, including mine!’ So what does this really mean for reliability and quality professionals? And importantly, what can you do about it? ᐅ Play Episode
by Dianna Deeney Leave a Comment
Have you ever watched a promising product idea slowly die in the fuzzy space between “great concept” and “actual development”? You’re not alone.
The journey from product idea to market-ready solution contains a critical yet often overlooked phase: concept development. This is where cross-functional teams must align their diverse perspectives to create a solid foundation for design. But as many product developers discover, this is precisely where communication frequently breaks down.
In this episode, we dive deep into why cross-functional teams struggle to communicate effectively during early concept development and how to fix it.
by Christopher Jackson Leave a Comment
Ever heard of the MTBF? A lot of people have. But not many people (truly) understand what it is. For example, is it possible for one product with a larger (better) MTBF to have more warranty failures than another product with a smaller (worse) MTBF? A lot of people think not. But it actually is. And not in just some weird, once in a lifetime sort of way. Lots of products with larger (better) MTBFs fail more often than those with smaller (worse) MTBFs. Confused? This webinar will help!
[Read more…]
by Greg Christensen Leave a Comment
We love conversations like this!! A total blast connecting with Sanya for this real and practical discussion about Cultural Influences and Perspectives in maintenance and reliability.
This episode features Sanya Mathura of Strategic Reliability Solutions, Ltd featuring a discussion about various aspects of maintenance and reliability practices within organizations, the implementation of computerized maintenance management software (CMMS), and the realities of sensor monitoring.
Cultural impacts and how they play out. What is STEM? Wait, there’s now an “A” in STEM? We learn about Sanya’s New Book! She has written several books and is renowned for her knowledge in the lubrication space as a path toward ultimate reliability!!
We chat about the importance of self-care! Plus, loads of fun conversation around Sonya’s journey and some fun personal insights at the “fun questions” segment.
Tune in and get some valuable insights and practical advice for individuals and organizations seeking to optimize maintenance and reliability practices while prioritizing employee well-being and engagement.
Connect with Sanya on LinkedIn or head over to www.strategicreliabilitysolutions.com and be sure to grab Sanya’s new book (it’s in the episode and on the website).
by Mike Konrad Leave a Comment
On this episode of the Reliability Matters podcast, I left my usual studio for the IPC APEX Expo in Anaheim California.
I interviewed two subject matter experts on topics related to electronic assembly.
My guests are:
Gerald Gardner, Global Product Manager at Weller, a manufacturer of hand soldering equipment fume extraction systems, and precision tools.
Mike Young – CEO OF SASinno Americas, a manufacturer of wave and selective soldering equipment.
More information on my guest’s companies is available here:
SASinno Americas
https://www.sasinnoamericas.com
Weller
https://www.weller-tools.com/us/en
by Christopher Jackson Leave a Comment
Chris and Fred discuss talk about how to ‘rank’ reliability engineering books that are actually based on helpfulness (and perhaps not an algorithm).
ᐅ Play Episode
by Greg Christensen Leave a Comment
Here’s another awesome episode where we get to learn about Umbrava, a Facilities Management Ecosystem and CMMS, and Broadway International, with Joe Reda joining us to share the background, how it started, why it started, what this really dos for the FM and CMMS space, the people and the processes – Everything we like to hear about when it comes to journey stories to help you on your CMMS journey. Thank you, Joe Reda, for the great discussion and participating in the fun questions segment.
This is built on 30+ years of real-world experience so it’s well grounded in the right workflows with a focus on delivering outcomes. We cannot wait to see this journey continue and unfold. If you want to connect with Joe Reda, he’s on LinkedIn or connect at joe@umbrava.com to start your own journey!!
by Greg Christensen Leave a Comment
Racing Toward Electrical Excellence: Skilled Trades, Business, Winning Strategies with Doug Winston!!! #98 dropping truth bombs in this episode. Buckle up and tune in!!
Thank you, Doug, for joining CMMSradio to share these real, raw, and practical insights!
In this episode, Doug Winston, the President of D&M Electrical Contracting, Inc., shares his journey story including how it all started (several racing stories), insights into the skilled trades, the business of electrical contracting, his passion for racing cars and addressing the skilled trades gap.
Key Points:
This episode offers a unique blend of personal anecdotes, professional insights, and a passionate call to revive the skilled trades, making it a must-listen for anyone interested in the electrical contracting industry, maintenance management, business strategies, and the future of skilled labor in America. We get into the typical “fun” questions as well to shine a light on Doug’s perspectives.
D&M Electrical Contracting, Inc.: https://www.dmelectrical.com/
Bring Back the Trades: https://bringbackthetrades.org/
by Christopher Jackson Leave a Comment
Chris and Fred discuss the psychology behind (bad) reliability decisions. Humans run (and ruin) everything!
ᐅ Play Episode
by Greg Christensen Leave a Comment
WARNING Heavy Metal and Manufacturing Ahead!!!
This AWESOME episode features Hallie Haupt, Director of Marketing at IQ Manufacturing, sharing her journey into (and in) the #manufacturing industry. She joined Greg Christensen, the Host of CMMSradio, to discuss her background, and the challenges created by the skilled trades gap in the manufacturing space, and – Wait for it – Her exciting Heavy Metal experience at a #Metallica concert (2 different days) in Detroit.
Key Points:
Thank you, Hallie, for this amazing conversation and the work you do!
by Greg Hutchins Leave a Comment
Greg and Fred discuss risk management tools specifically the advantages and disadvantages of using color -coded risk matrices.
ᐅ Play Episode
by Greg Christensen Leave a Comment
In this episode, Tom Moriarty, a recognized expert in leadership, asset management, engineering, and reliability, discusses key aspects of successful asset management and maintenance practices on CMMSradio. The conversation highlights the foundational role of organizational leadership and the importance of accountability in implementing effective processes, emphasizing the challenge organizations face in sustaining positive practices and the need for continuous improvement.
We touch on the relationship between customers and CMMS vendors stressing the need for customers to be educated about good asset management and work management processes before selecting a CMMS solution.
Talking Points:
…and more.