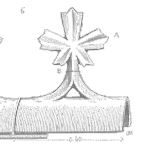
Basic Definitions
- Reliability: Ability to provide continuous and stable system/component function under defined operating conditions without failure(s).
- Mean Time Between Failures (MTBF): Average expected time interval between failures. Often a measure of reliability.
- Failure Rate is the expected no. of failures over a period of time. MTBF is the inverse of failure rate.
- Availability: Percentage of time a system or component can perform its intended function without failure.
- Key aspects involve individual component reliability, system architecture, redundancy, and implementation of control strategies to ensure uninterrupted service.
- Availability = Uptime/(Total Operation Time) = MTBF/(MTBF+MTTR), MTTR is a measure of time to repair the system/component
- For example, 99.999% (5-9’s of availability) -> 5 min downtime in one year
- Reliability Block Diagram: Reliability Block Diagram (RBD) is a graphical representation used to model reliability in complex systems. Illustrates interconnections between various components or subsystems within a system.