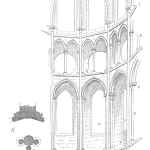
An example of an Accuracy Controlled Enterprise ACE 3T (Target – Tolerance – Test) Procedure with reliability standards to install taper spherical roller bearings on adaptor sleeves in Plummer blocks with taconite seals for 30mm-250mm diameter conveyor shafts
Machine performance is totally dependent on human beings. To address the problem of human error causing equipment failure, an Accuracy Controlled Enterprise sets best practice quality standards and uses 3T Target-Tolerance-Test work task quality control that assures high quality workmanship for high reliability results. Their work procedures are standardised so everyone follows the same methods to produce the same results, their training teaches people how to do craftsmanship work that creates outstandingly reliable plant and machinery. They create the reliability they want and as a result achieve operational excellence.