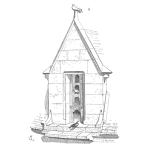
ANSI-IES TM-21 standard method may predict negative L70 LED lives. (L70 is the age at which LED lumens output has deteriorated to less than 70% of initial lumens.) Philips-Lumileds deserves credit for publishing the data that inspired an alternative L70 reliability estimation method based on geometric Brownian motion of stock prices in the Black-Scholes-Merton options price model. This gives the inverse Gauss distribution of L70 for LEDs.
[Read more…]