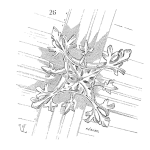
The Arrhenius Equation is widely used and accepted by reliability and validation engineers from many industries to develop accelerated life tests (ALT) for thermal aging environments.
The general form of the equation describes the reaction rate of a process as a function of temperature (K), the Boltzmann constant (8.617E-5 eV/K) and two empirical factors. It can be written as:
[Read more…]