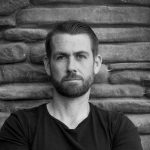
Is Maintainability Only About Repair Time?
Abstract
Chris and Fred discuss one of the most popular interpretations of maintainability which is based on how long it takes to maintain something. We see so many textbooks and guides that focus on this metric as the only maintainability measure. But is this really all that matters? What about the number of technicians required? … the number of tools required? … the training required for these technicians? … the mass of these tools? Does reliability matter? Yes to all these things. But how does they relate to the time-based definition? They don’t. Listen to this podcast to learn more.
ᐅ Play Episode