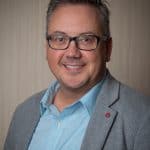
231 – Process Safety Management with Paul Daoust
We’re proud to have the Scio Asset Management founder and MD, Paul Daoust with us. He has extensive experience in the energy, oil, and gas sectors. Paul’s also on the Board of Directors at PEMAC. His more than 25 years of experience have helped in the development of Process Safety Management Systems. The approach for those was practical and pragmatic. He took it from ScottishPower’s reconsideration of their facility’s management. These were based on Process Safety practices from the North Seas.
Together we’ll take an in-depth look at:
- What is Process Safety
- Which industries or assets does Process Safety apply to more
- Are preventative and predictive programs a part of Process Safety
- Is Process Safety related to Process Safety Management (PSM)
… and so much more!
Those practices helped ScottishPower reduce the risk of major accidents. It also helped reduce their maintenance, improving their operations. That’s because they built Process Safety into an integrated operations management system. This got done in partnership with the Health and Safety Executive in the UK. As a result, their case study has been well documented.
ScottishPower then commercialized their approach. This is what Paul’s used to learn and apply over the past few years. Thus, he’ll show us pragmatic ways to get Process Safety in integrated management systems.
What is Process Safety?
Wikipedia describes it as ‘The prevention of the unintentional release of chemicals, energy or other potentially dangerous materials during the course of processes, that can have a serious effect on the plant environment, and the safety of people.’ It’s the managing of hazards from the assets and industrial processes themselves.
Process Safety must get contrasted from the more common Occupational Safety. The latter deals with the safety inherent from the work and related tasks, and the surrounding work environment. With these, safety is the common element here. But, it’s a bit different from your usual health, safety, and environmental practice.
Most of the worst industrial accidents appear as a series of unfortunate incidents. Many contributing factors should get managed individually. That helps ensure the safety of the system and the plant as a whole. Process Safety is about understanding your hazards and managing them deliberately.
Which industries or assets does Process Safety apply to more?
You must apply the correct rigour and discipline. You’ll notice that all industrial sectors have the potential for major accidents. There isn’t a single solution that applies to all industries. For instance, there are high hazard sites with explosive chemicals and such. For such a facility, a high level of rigour and discipline is needed. You’d also need formal Process Safety Management. For other industries, Process Safety can get applied with some of the same techniques but in a practical manner. For example, in the US, OSHA has requirements for Process Safety. So, you need to meet these requirements in a way that fits a particular organization’s needs.
Are preventative and predictive programs a part of Process Safety?
These programs to some extent show you have a Process Safety measure in place. But Process Safety, operations and maintenance need a different mindset. The Process Safety mindset needs to be held together with the job descriptions held. The practice of Process Safety requires lessons in leadership. You also need to teach the organization’s other practitioners what it is. Most people do risk assessments from the reliability perspective, rather than from the safety one. They forget the assets are part of a formal protective scheme.
Is Process Safety related to Process Safety Management (PSM)?
You can look at Process Safety as a practice. With PSM, it’s closer to a system of management. With any management system, particularly with safety, you have to say what you do, do what you say, and prove it. Some places have the PSM built as a self-contained management system within the operation’s broader context. But Process Safety is better when integrated within the holistic operational management system.
When you’re building a PSM, you need to draw attention to Process Safety in and of itself. The awareness is key but it doesn’t have to be a stand-alone entity. At the end of the day it’s best if it’s integrated because regardless of your role, safety is a part of it.
How do you get started with Process Safety?
There are a few ways to go about it based on a set of practices in functional safety engineering. But you need to make it practical for the organization in question.
- Assess the criticality of your asset
You can use a basic assessment scoring of 1-9 based on worst plausible consequence. Your major accidents, in terms of safety consequences, would be a 9. Major environmental consequences would be an 8. Major financial consequences would be a 7. And you continue until you get to a score of 1. This is where the failure of that asset doesn’t have a consequence other than the repair cost.
Criticality gets used in combination with other urgencies. These could be maintenance work order planning or scheduling prioritization. A simple asset criticality scheme is based on the worst plausible consequence or worst credible consequence. Reliability experts tend to assess criticality based on the most likely consequence. But you need to be able to tell the difference between the two.
- Perform a Process Hazard Analysis (PHA)
You need to know what your hazards are and what’s necessary to manage them. HAZOPs and FMEAs are a way to measure this. Another option is Bow-Tie diagrams which are visual. They highlight your major accident hazards and those events you’re trying to prevent. They also show threats and preventive and mitigative barriers. This makes it a graphical multi-linear version of James Reason’s Swiss cheese model.
- Understand the integrity of the barriers used to mitigate risks
This isn’t just a maintenance function. It also applies to engineering, operations, the supply chain, and the leadership. Everyone has to work together. Once you have a formal asset management plan, you have to apply that to safety-critical assets. You can promote that through safety asset classes. Develop management plans by a class before applying them into your CMMS or EAM systems.
- Declare an impairment
This is where you get to work to restore integrity at the earliest opportunity.
Your safety process program needs to document all this. But you don’t need everything to be complete and perfect to get this done. There are other ways to quicken the process depending on the organization’s maturity.
Where do you get the data for this program?
It takes a lot of information and data to manage well. There’s a Process Safety lifecycle. It starts from plant design, through the operate and maintain phase, to the end of the facility life. Though it begins with the process hazard analysis, there are other forms of information that gets managed.
There are layers of protection analysis. There are safety integrity levels, or (SIL) determinations. There’s contingency planning. There are safety requirement specifications. There’s SIL verification. There’s also realtime resilience management. This is where you try to measure in realtime the integrity of those risk production measures. All these are required for a good functional safety system. But keep in mind that you build this stuff as you go, it’s not about perfection from the onset.
During a functional safety training, you may not come across terms like Safety Instrumented Systems, LOPA, or SIL. But you still need good designs that function as intended. You still need to maintain the functions of those systems and call out those tasks that are safety-related. It’s important to understand what’s Process Safety and what’s not.
Do you cut all risks or mitigate some of the risks by having this program in place?
Engineering teaches that we should always cut risks as the first option. But, most of these industries cannot operate in zero risk environments. So, it’s mainly about mitigating those risks in design, in how we operate, and in how we manage. ALARP or as low as reasonably practicable is a term used in the regulation and management of safety-critical systems. The principle here is to reduce the risk as far as is reasonably practicable, or until the risk is disproportionate. The cost to reduce the risk any further is disproportionate to any risk reduction that comes from that. That phrase makes up part of the Process Safety lexicon as it’s part of managing risk.
There’s another term that’s similar but is not the same. This is ‘so far as is reasonably practicable’ and it was developed as a result of common law court judgements. The SFAIRP term goes further than ALARP though it’s similar in concept. In a way, it says you shouldn’t bother with guessing the degree of the rareness of an event. Just do what needs to get done to ensure that event doesn’t occur. Don’t get caught up in trying to evaluate the degree of rareness to match your semblance of risk tolerance.
The organization needs to understand what its safety risk tolerance is. Don’t let the quantitative aspects stop you from doing everything that’s reasonable. There are tests to help you know what reasonable means. You also have standards and legislation that can help as well. These are all ways to test whether what you’re doing would meet the organization’s due diligence here.
What are Some of the Available Process Safety Standards?
There are lots of standards, models, and organizations to help you manage Process Safety. There’s:
- The two IEC standards 62508 which is a functional safety standard and 61511 which is the safety instrumented standard
- The API for Mechanical Integrity
- The OSHA 1910.119 with its 14 elements
- The DuPont Model
- The Center for Chemical Process Safety (CCPS) which is part of the American Institute of Chemical Engineers
- The Canadian Center for Occupational Health and Safety which even has a simple document on Process Safety
How to be Successful with Process Safety
Those in industrial facilities should know and understand their Process Safety hazards. You need to recognize what those dangers are. From there, you need to be deliberate about identifying and managing them.
Process Safety isn’t a one size fits all solution. The inherent dangers in your facility and your risk tolerance will drive you to understand what practice makes sense. That way you can put as much rigour into it as is necessary. You’ll also be more deliberate about what you say you do and prove that you’re doing what you said you’d do so that you reduce your risk.
It’s important to understand what’s appropriate for your organization. This is a conversation few many senior operational leaders are having.
Final Words
With Process Safety, a welcome advancement would be to know what your realtime risks are. That way, you’ll understand what your resilience is on a realtime basis. That’s hard to achieve but still possible. Start by deciding what the hazards are and how to manage them. From there, begin to measure the integrity of the barriers between your people and their equipment.
Eruditio Links:
Paul Daoust Links:
- ScioAM.com
- Paul Daoust Linkedin
- Scio AM Linkedin
- PEMAC.org
- Scottish Power HSE Case Study
- Black Swan Book
- PHA Book
- Bow Tie Diagram
- ACM Facility Safety
- IEC 6508
- IEC 61511
- OHSA 1910
- CCPS
- CCOHS
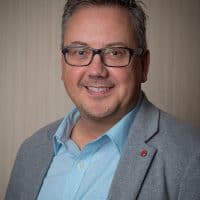
- Social:
- Link:
- Embed:
Rooted In Reliability podcast is a proud member of Reliability.fm network. We encourage you to please rate and review this podcast on iTunes and Stitcher. It ensures the podcast stays relevant and is easy to find by like-minded professionals. It is only with your ratings and reviews that the Rooted In Reliability podcast can continue to grow. Thank you for providing the small but critical support for the Rooted In Reliability podcast!
Leave a Reply