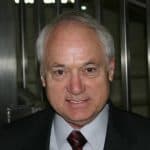
Reliability with a Best Practice Organization with Heinz Bloch, Part 2 of 2
Striving to be best in class is perhaps the ultimate goal of every organization. But what exactly does it take to get there? In the first part of this podcast, we talked about the changes seen in maintenance, reliability, and failure analysis over the years and what makes these practices successful in best in class organizations.
Another aspect to best practice reliability is the use of lubrication. Good lubrication entails improving the choice of lubricant and lubrication method, oil filtration, cooling systems, prevention and removal of water content.
Over the years there has been a greater acceptance of the merits of properly choosing synthetic lubricants. In the best of class companies, they came to understand that even the most appropriate synthetic lubricants can be contaminated by dirt and become unserviceable by dirt. Over the past decades, best performing plants have transitioned to from the conventional to a far more advanced and cost-effective methods such as air filter, desiccant breather, or closed-loop systems. The goal of using these optimum techniques of applying lubricants is to protect the lubricants from the intrusion of atmospheric moisture and from the intrusion of dirt and dust.
It’s worth mentioning that there still exists in the industry a misunderstanding as to how cost justifies oil mist. By definition, oil mist (also called oil fog) may form when high pressure fuel oil, lubricating oil, hydraulic oil, or other oil is sprayed through a narrow crack, or when leaked oil connects with a high temperature surface vaporizes and comes in contact with low air temperature. Oil mist lubrication oils are applied to rolling element (antifriction) bearings as an oil mist. Another advanced lubrication method is called oil-jet. Compared to oil rings whose amount of degradation and deterioration is limiting the bearing life, both oil-mist and oil-jet lubrication methods are far more superior and can considerably extend the bearing life.
By using these superior lubrication method and therefore extend the bearing life to say 4 years, that is a huge savings since you only have one maintenance expenditure within 4 years. Moreover, If you factor in the savings in terms of manpower for normal routine maintenance by using oil mist on both pump and driver, then you have a typically a payback period of somewhere between 8 months and 1.8 years (oil mist being used only on pump could take twice as long).
Bottom line is, in best of class companies, one is not looking for a magic bullet. Rather, to drive reliability, they systematically eradicate the potential causes of failures by using efficient and cost-effective methods and practices, data-driven decision making, and empowering their people by providing them access to the top management and to resources such as books and up-training that can enhance their skills and bring their ideas into fruition, and ultimately direct the organization to the best of class status.
Eruditio Links:
- Eruditio
- HP Reliability
- A Smarter Way of Preventative Maintenance Free eBook
- inspired Blended Learning (iBL®)
- James Kovacevic’s LinkedIn
Heinz Bloch Links:
- Personal Website
- Email: heinzpbloch@gmail.com
- Recommended Book: Petrochemical Machinery Insights
- Other Books by Heinz P. Bloch
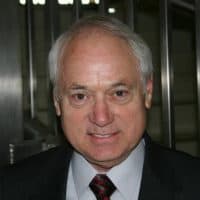
- Social:
- Link:
- Embed:
Rooted In Reliability podcast is a proud member of Reliability.fm network. We encourage you to please rate and review this podcast on iTunes and Stitcher. It ensures the podcast stays relevant and is easy to find by like-minded professionals. It is only with your ratings and reviews that the Rooted In Reliability podcast can continue to grow. Thank you for providing the small but critical support for the Rooted In Reliability podcast!
Leave a Reply