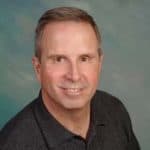
How to Get the Most Out of Your PM Program with Ricky Smith
There are a lot of companies that have their own Preventive Maintenance programs now and only a few of those are good at it. Even though they perform regular preventive maintenance but they never get the desired results. The equipment still fails frequently and they are annoyed by the fact that what they do never works. It is mostly because they do the same routine compliance over and over again without ever trying anything new or at the very least learn about new practices. This is where the Preventive Maintenance fails and companies bear the extra cost of maintenance.
The simple fact that these companies fail to grasp is that you can’t just do the compliance without ever changing your maintenance process—that should clearly be based on condition monitoring of your equipment. The goal should be to reduce the downtime not just perform and complete the compliance. There are a few things that you can do to improve your PM program and everything about it starts with educating your workforce. They need to know what kind of systems they have to handle and how they work. The assessment of your present processes and work routines should always be the first step.
When you have done a complete assessment, you need to strategize your Preventive Maintenance and design, revise, or change the practices of your reliability program. You need to get everyone in the same room and make them understand the need for change because you can’t bear the losses forever. Make them see the results of the newly designed maintenance processes and have everyone committed to it, especially the management. You need to document the whole routine processes, use graphical explanations if need be, and then get the instructions, steps, and specifics of that process published for everyone to see and follow.
The organizations need to understand that the change takes time and you can always start simple and small because you must improve your programs with time. It is the responsibility of the planners and managers to make sure the benefits are known to everyone and people need to see the results if they are ever going to accept and commit to the new processes. When you do that, everyone is going to take interest in knowing the components you have in place. They are going to assess those components, observe the failure modes in your systems, and then they can do something before the defect even occurs or at least minimize the impact.
Not everything can be achieved in a short time so you have to be patient to be actually successful. Only if you can detect the failure in time, you will be able to repair or plan for a scheduled failure. This is not to be taken lightly because some failures are catastrophic to just shut you down completely. The similar problems are easy to handle but the unknown issues can be tackled only by communicating about them. You have to believe in what you do.
Eruditio Links:
- Eruditio, LLC
- A Smarter Way of Preventative Maintenance – Free eBook
- Maintenance Planning & Scheduling: Planning for Profitability Video Course
Ricky Smith Links:
- email: askrickysmith@gmail.com
- Preventive Maintenance Made Simply by Ricky Smith and Doug Stangier
- Root Cause Analysis Made Simple by Ricky Smith and Susan Lubell
- Rules of Thumb for Maintenance & Reliability Engineers by Ricky Smith
- CRL Passport Series
- SMRP
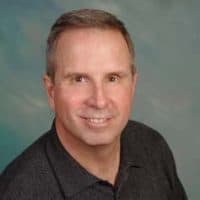
- Social:
- Link:
- Embed:
Rooted In Reliability podcast is a proud member of Reliability.fm network. We encourage you to please rate and review this podcast on iTunes and Stitcher. It ensures the podcast stays relevant and is easy to find by like-minded professionals. It is only with your ratings and reviews that the Rooted In Reliability podcast can continue to grow. Thank you for providing the small but critical support for the Rooted In Reliability podcast!
Leave a Reply