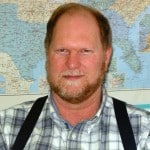
The Role of Alignment in Precision Maintenance with Alan Luedeking
In today’s episode, our guest is Alan Luedeking and the topic of discussion is alignment and precision maintenance. The first thing that pops up into the mind is that where to start with the precision maintenance. The first step can be keeping all of your equipment aligned because that really helps to avoid common problems in equipment. The alignment saves you a lot of money, increases the productivity, and efficiency. After this, we can start monitoring activities all along the way.
There has been a lot of improvement because of the laser shaft alignment and laser geometric alignment systems. They help you to identify the failures in your machinery and eliminate them easily. That’s why it is always critical to make necessary alignment activities to keep your equipment working stably and consistently with accuracy, less effort, and less training. We can also use straight edge method for rough coupling and alignment or otherwise reverse indicator method which is sometimes affected by obstacles like vibration effects can be used when the technician is experienced enough to know exactly what he is doing for accurate results. However, these methods are not as efficient and accurate as the use of the laser is.
The major types of misalignment are the offset and angular misalignment. The laser alignment is definitely faster and cost-effective but the use of this technique needs some training for good outcomes. There are couple of very common phenomenon that occur while working in the workshops are,
- Thermal growth in which some parts of the machines suffer expansion because of the over-running or heating mechanism which causes the problems of misalignment because of the change in relative positions of the parts due to the growth in the machine parts.
- The secondary cause of the misalignment is soft foot which causes the distortion in the frames of the machines that are coupled directly to each other.
Now there are some steps that you can take to resolve these alignment issues. The first step is to lock out and tag out the machines to work for safety. Then you should clean the area around the machine feed. In the end, check for soft foot and then align the machines properly and recheck them if needed for surety. You should also document these problems that you found and resolving methods for specific issues according to ISO 9000. Preventative maintenance is always better for which your bases should be strong to avoid any soft foot failures in the first place. At the best, you can do is to buy the laser alignment equipment from the best vendors who can work with you when you need them and give the workers some training for best results.
You should always check for failures and correct them on a regular basis to make sure the perfect alignment for longevity. Implementing a complete formal alignment procedure is always an edge in the field of reliability and maintenance.
Alan Luedeking, CMRP, CRL is Executive Vice President of Ludeca, Inc. in Doral, FL. He has 30+ years experience in machinery shaft alignment and training and holds an ISO level I Vibration Analyst certificate as well as a Level I Ultrasound Inspection certificate. Besides his work, Alan enjoys spending time with his family and numismatics. www.ludeca.com
References:
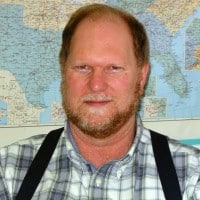
- Social:
- Link:
- Embed:
Rooted In Reliability podcast is a proud member of Reliability.fm network. We encourage you to please rate and review this podcast on iTunes and Stitcher. It ensures the podcast stays relevant and is easy to find by like-minded professionals. It is only with your ratings and reviews that the Rooted In Reliability podcast can continue to grow. Thank you for providing the small but critical support for the Rooted In Reliability podcast!
Leave a Reply