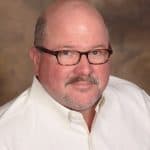
Sealing in Pulp & Paper with Chuck Tanner
Today we’re joined by Chuck Tanner, the director of market development at SEPCO. With over 25 years in the industry, he’s been helping with sealing challenges.
In this episode:
- What is sealing
- Why are pulp and paper sealing hard
- How do we overcome contamination
- Do successful organizations have good maintenance programs on the seals to improve reliability
… and so much more!
What is sealing?
Sealing provides a mechanical device to control a leakage between two joining surfaces. There are two types of sealing surfaces:
- Stationary surfaces – these use gasketing to seal them
- Dynamic surfaces – these use a device to seal two moving objects. It can be rotational or helical movement.
Sealing is preventing some fluid or gas from reaching the atmosphere using a device.
Why are pulp and paper sealing hard?
The predominant product sealed in the pulp and paper industry is slurries. There are many slurry types within a pulp and paper production facility. These are liquors such as white, black, and green liquors. Then there are the actual fiber slurries or paper stock slurries that you have to seal.
Slurries in fluid sealing don’t provide a lubricating film between the dynamic and stationary surfaces. Unfortunately, slurries are very abrasive. They damage sleeves and seal faces, among others.
Are there other sealing issues in pulp and paper?
Slurries make up 90% of their processes. The only reasonably clean products they produce are some caustics in acids. There are also condensate services and water services.
How do we overcome contamination?
The only way to do it is by providing some clean lubricating film. Without it, the lives of all sealing products become reduced. By keeping the lubricating film between the seal face and the packing in the sleeves, you can get longevity. The surfaces also need to be clean and cool. Without those, the service life reduces.
Are there seal types best suited for this application? Those to overcome the lack of clean and cool lubricant
Unfortunately, there’s no way to overcome that without the source of lubricating films. Pulp and paper have always strived to do away with flush water. But the products pumped, and the technology for sealing is abusive to fluid saving. So there’s no way to do it.
Thus, in fluid sealing, we need good practices. Also, you need to use the products as designed and find pressures rather than water flows. You can use these products and still use water. But with proper care and maintenance, water usage and consumption goes down.
Do successful organizations have good maintenance programs on the seals to improve reliability?
Most plants that do well are active in precision maintenance training. With precision maintenance training and programs, issues with fluid sealing products go away. That’s because they understand the concepts of the products, and what you’re trying to do with them. You’ll also know what you can or cannot do with the products.
Accounts with good practices and proper maintenance can even get three years. As far as mechanical seals in such accounts, four to five years of average seal life aren’t uncommon.
What does a typical pulp and paper facility get out of a seal set?
Mechanical seals cost a lot to replace. A mechanical seal failure needs a replacement of the whole pump rotating assembly. So you have to factor in the cost of the entire unit rather than only the seal. These can range anywhere from $25,000-$30,000.
The industry average on mechanical seals in pulp and paper is close to 24 months. That’s about half the service life you should get. It also doubles the amount of maintenance needed.
Mechanical sealed applications on typical plants have about 200 equipment pieces. Approximately 50 parts should get replaced each year to get four to five years of service life. Poor maintenance and care practices lead to unnecessary replacements. These affect your plant’s cost per time.
Other areas in pulp and paper, apart from slurries, that organizations should track
Another area to look at is paper machine services. From where they dry the paper, they return the condensate to the powerhouse. That’s treated water. Most organizations have tried to run mechanical seals in those applications. But, the issue becomes the water temperatures.
Hot water is a terrible lubricant. You get over 160 degrees on the velocity and heat generated to seal face. Those water molecules pass the seal face to lubricate it and can get up to flashpoint. When that happens, they expand back to steam. That causes them to take up to seven times their original space. It creates a small explosion that destroys the seal.
You’ll have short term success with mechanical seals in some of those applications. But long term, the seals won’t hold up. In such instances, it’s advisable to convert back to packing. There are packing products that leak very little, surpassing mechanical seals. The cost is also minimal when compared with utilizing mechanical seals.
What else can organizations do to improve reliability with seals and pumps in pulp and paper?
You could opt for the new air sealed technology. It’s suitable for places with heavy slurries or those with a lot of radial-axial movement. These include pulpers, agitators, and refiners. The air sealed technology is now run on stock pumps as well. It utilizes no water. An air pad seals between a floating member within the sealing device and the shaft.
Is the air sealing technology suitable for slurry sealing systems?
Air sealing works well with slurry systems. It exceeds the mechanical limitations of any mechanical seals. Repulpers, agitators, and refiners all have a lot of mechanical axial-radial movement. These are unsuitable for mechanical seals. You’re limited by what the springs will allow you to do. Air seal technology takes up to a one-quarter inch of radial movement. They also have incredible service lives. Some seals currently in the field have gone 48 months without any servicing. They may exceed the service life of mechanical seals.
What makes the most difference in being successful with sealing in pulp and paper?
It would have to be picking the right products. Look for recommended packing arrangements and braided products. With mechanical sealing technology, most organizations settle for the same seals and configurations. These apply to specific liquor applications. So you’ll find those who run double seals with hard faces on the inside. These compensate for periodic losses of flush water lubrication on those seals.
What can you change in a typical pulp and paper to get up to 60 months of service life?
You have to manage the use of the products you have. Work with a vendor that helps you select the proper product for the application. The vendor should also be able to troubleshoot in case of any issues.
The plant sites also have to commit to maintaining the products. The products are a small part of the total rebuild cost of a piece of capital equipment. But they as the first signs of problems within that equipment. It’s the weakest link. You need to commit to finding weak links, such as in the pipe’s drain or misalignments. Find what’s causing the symptoms to show up first. Also, commit to finding corrective measures that enhance reliability.
Training is another essential aspect. Everyone within the plant should understand what the products are. They also need to know how they function. It’s not only about maintenance. The production also gets affected.
How to do sealing in pulp and paper differently
Start by checking the consumption of these products. The usage will tell you all about what these products are costing you. Run storeroom reports on usage. Also, get total population accounts of mechanical seals or packing. Then look at some of the ratios and numbers. These help to figure out if your plant is where you want it to be. You’ll even know if the products are increasing operational costs. Review and set goals for where you want your facility to be. It’s a small cost in the maintenance budget that can cost you millions if mismanaged. It’s a symptom of a bigger problem.
Eruditio Links:
Chuck Tanner Links:
- Sepco.com
- Sepco Linkedin
- Chuck Tanner’s LinkedIn
- How to Choose the Correct Seal Type with Chuck Tanner
- Seal Connect Webpage (Sepco)
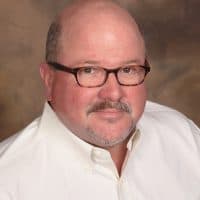
- Social:
- Link:
- Embed:
Rooted In Reliability podcast is a proud member of Reliability.fm network. We encourage you to please rate and review this podcast on iTunes and Stitcher. It ensures the podcast stays relevant and is easy to find by like-minded professionals. It is only with your ratings and reviews that the Rooted In Reliability podcast can continue to grow. Thank you for providing the small but critical support for the Rooted In Reliability podcast!
Leave a Reply