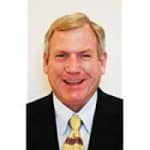
How Detailed Should a Job Plan Be with Jeff Shiver
Jeff Shiver works with People and Processes. He is heavily involved with maintenance and reliability. He has made presentations for years. He started out in Procter and Gamble doing controls and engineering. He has also worked with Mars in four different plants and also held cooperate roles. He was a maintenance and production manager. He left in 2006 and started People and Processes.
When it comes to planning and practitioning, he has 25 years of experience. Many people suffer with planning in an organization yet it is the hub of everything. So Jeff tells us more.
Jeff will help us get a look at:
- Why do Organizations need to Plan their Work
- How Detailed should Job Plans be
- How do we know if we are going too deep or not deep at all
- How do you deal with a Planner with a strong background in another Trade
… and so much more!
Why do Organizations need to Plan their Work?
What happens is that many technicians go out there and there always experiencing avoidable delays for instance not having the right information, materials or time to do the work. Question is, what is the experience level of the technician and how it be improved?
It’s not uncommon to find a planner spending more than five hours a day just trying to see that the technician gets the right tools especially if the storeroom is disorganized.
Ask yourself what you got when the piece of equipment was installed. What is it that you introduced that makes a difference that wasn’t there? Is it the bolts or did you use the incorrect spare? Planning gives us a tool to get back to the level of specification.
Defect elimination is different and happens with cases in the frontend. Here we look at how you achieve the capability of the asset.
How Detailed should Job Plans be?
Ask yourself what is the minimal qualifications of your technician? Write your plans in a way that you cover the minimal requirements. Job plans provide standardized work so how do we write them to level specification so that we can go out and achieve what we have to?
You should not introduce defects. Most of the times, people want to be told what to do and not how to do it. Work should be done to a specific level of standardization. Things should be done the same way. Do not have every technician doing things their own way.
Doing things the same way makes it easier to find out why failures occurred. Teach and train your technicians.
How do we know if we are going too deep or not deep at all?
There are a lot of variables involved. Nothing is clear cut but if we go too deep, we need some level of minimum qualifications. A planner should have craft skills so that they get into the role. A planner with technical skills will understand the kind of good balance required. The plan will be thoroughly executed.
How do you deal with a Planner with a strong background in another Trade?
Do not swop your planners. You might mess up with the pay and other things. The expectation of the technician is that the planner will give them the job while the planner is relying on the craftsmanship of the technician. The reality is that there is a process for this. The planner should give the technician a head start especially if the planner is not an expert in that particular field. The planner should get the materials and understand how long the work takes and how many people are required to get the job done then schedule it. There should be a job feedback process to see what can be improved over time. There is no perfect job plan because there is always something to improve.
What Role does a Job Plan Library Play?
In many cases, most planning functions have zero job plan libraries. Digging under the covers will reveal this. Most of them have a job history but that is not a job plan library.
The job plan library will reduce your planning time. Create a job plan template showing how you do things in your organization. The benefit is that you may be planning the job that is similar but not exactly the same. You can use what you have and custom make the rest.
The other important thing is how you name your job plans for recall and they should not be tied to a specific asset.
Plans also allow us to capture knowledge.
What makes Job Plans Successful at the Right Level?
Feedback from the technicians and actually doing something about it is the secret ingredient of making everything successful.
The minimal job plan is a start. The feedback loop is a critical piece.
The relationship between management and the technicians should be a partnership. Are you all headed in the same direction?
Have a job plan library and leverage the feedback. Fix what needs to be fixed. Organizations need to develop processes and stick to them.
If you cannot take advantage of the analytics and the skills of your technicians then you have nothing to build on. Reliability is not an everybody thing. It all starts with education, help people understand what they are supposed to do and why.
Take action. It’s one thing to talk. You have an opportunity to find out what is working and what is failing but you need to take the first step.
Eruditio Links:
Jeff Shiver Links:
- People and Processes
- People and Processes LinkedIn
- Jeff Shiver Linkedin
- Ask Jeff on Plant Services.com
- People and Processes YouTube
- Planning and Scheduling with Jeff Shiver
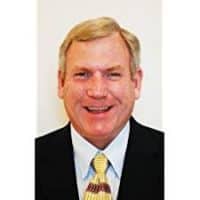
- Social:
- Link:
- Embed:
Rooted In Reliability podcast is a proud member of Reliability.fm network. We encourage you to please rate and review this podcast on iTunes and Stitcher. It ensures the podcast stays relevant and is easy to find by like-minded professionals. It is only with your ratings and reviews that the Rooted In Reliability podcast can continue to grow. Thank you for providing the small but critical support for the Rooted In Reliability podcast!
Leave a Reply