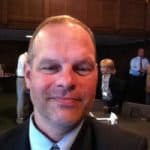
Maintenance is a Marathon, Not a Sprint with Michael Mazur
We’re glad to have Michael Mazur from Schwan’s Global Supply Chain. With 10 years at that plant, he currently holds the role of a maintenance technician. He’s previously worked as a trainer and supervisor at Schwan’s. Michael started as an electronics maintenance technician in the navy. He was there for 21 years before moving on to Kone Elevators as a customer service analyst. He then became a vocational trainer at Lincoln Technical Institute.
His knowledge will help us get more insight into:
- How easy is it to develop a maintenance program?
- Why is maintenance a marathon and not a sprint?
- How do you prepare for this marathon?
… and so much more!
How easy is it to develop a maintenance program?
It’s a difficult process. Each plant and organization have different variables that will dictate:
- The type of maintenance plan
- How it operates
- The functionality
- The coordination with the operations team, logistics teams, etc.
You have to take a long-range look at the picture, not only what you have today. That’s what’s going to dictate how you develop and install your maintenance plan.
Why is maintenance a marathon and not a sprint?
Maintenance is a marathon. If you look at it any other way, anyone can throw a wrench into a piece of equipment and get it running again. But the concept of having your plant run and your operational efficiency levels higher, before failures lower them, is that you have to be in it for the long haul. But, if you’re looking for fast solutions, you’re not going to be able to have a long-term plan running efficiently.
How do you prepare for this marathon?
When you run, there’s a lot of preparation that goes into that. So, start by breaking it into thirds. That’s for what comes before, during the first half, and in the second half of the marathon. These are all to prep you on where you’re going and how it’s all put together. It’s going to be more about logistics. On the maintenance side, you’ll consider all things about management, supervision, and what that part of the team is putting together. That way, the runner knows where they’re going. Then you need to ask yourself if you have strength. If you can do everyday activities, then you can start a marathon.
The plant is the same. You’ll have pre-existing skills, workers who have knowledge they can bring to the table. Lastly, is the mental aspect. For a marathon, you’ll start to question yourself. Are you on the right path? Do you have the right pace? The same thing happens in the maintenance realm. There’s a long-term plan. You have an idea but it’s not really working. So, you want to quit and do something different. The final stage is the most difficult because it works on intangibles. Things you can’t put your finger on, but they’re on your mind.
1 – What is the management prep?
In a marathon, you’d have a race director to put things in place. If you’re looking at a five-year plan, you need to let people know your plans in advance. They need to know the route you’re taking and how you’re planning on getting there. You’ll also need markers that could be progress reports posted on the door or sent in emails. That way, you reach your markers with enough progress to keep moving forward.
You’ll then need aid stations. So, as you move on with your plan, you keep reinvigorating your team. That’s with knowledge about how the plan is going, and how it’s implemented. This includes knowledge of the protocols and processes you have on it. You should also have updates on the progress because setbacks are always present when dealing with plants.
In a marathon, there’s food somewhere on the route. With a plant, have a barbeque or catered event once you hit one of the milestones you set. This is a great way to get people to sit and talk about what happened, what’s to come, and also get to know each other.
A medical team at a marathon event is a must. In your maintenance plan, you should have this in your thought process while you move forward changing what you have in place. What is the safety level? This could be reinvigorating existing protocols. It’s also how you carry out maintenance emergencies that deal with personnel getting hurt or stuck in machines.
2 – What are the skill sets?
In a marathon, you need to get excited about the upcoming event. The same applies to a maintenance plan. You’re standing with people who want to go in the same direction as you. It could be a maintenance person involved in electrical, refrigeration or mechanical activities. It could also be the maintainers and the operator. They also have a role in the marathon alongside you. They’ll be there as part of your support team.
People come with pre-existing skills. These could be from a company you previously worked at or that you learned at school. To continue to build on that, you need:
- Coaching – it’s your job to train the other maintenance personnel. Give them tips and ideas on how to plan a job, work through it, finish a job safely and mechanically
- Training – although management and supervision should provide training, you also need to have your own training. If you rely only on the company’s training, you’re going to fall short. You’re the one who really knows what you want
- Your knowledge – you probably came in with some knowledge. But make sure you continue to grow it
- Practice – if you don’t practice your craft and you have a machine that runs for extended periods without any input necessary, you may be out of practice. Re-introduce yourself to your knowledge often so you don’t suffer when you need to perform the action
- Your tools – once you’ve identified the tools you need, you need to look at aspects like its cost or alternatives to using it. Mechanics need a baseline of tools to do their job, and their supervisors need to oversee what’s getting done. The cleanliness of your tools also matters. Have your tools clean and arranged for easy access when they’re needed
- Recognition – there should be people that recognize the effort put in to meet milestones. This could be by your superiors or peers
- Outside help – once you make your plan, you’ll notice you either have people with the skills you need, or you have to hire people to fill in a gap you have. With a five-year plan, you’ll need certain skill sets from the onset to help guide the process. The success of the plan relies on a team effort
3 – How do you avoid negative self-talk?
Rather than avoiding it, you’re going to counter it. Believe that you will be able to make things happen for the benefit of the plant. You need to believe that there will be people to help along the way. Believe there will be support for the logistics side. Even if you’re not familiar with the task at hand, believe you can look up the information. Put in the needed effort, and bring in people to assist or coach you so you can get the job done. The workers and management must also have the same beliefs so the plan progresses systematically.
Management should also not go with knee-jerk reactions when creating a plan. Stick to the original plan and see it through. There will be setbacks, changes, and variables throughout. But don’t deviate from the original plan.
Trust, respect and inner drive also play key roles in the process. You need to trust that you’ll do your best job. When you get trust, you’ll get more help when you need it. This means you’ll get to do your job better and faster. That goes on to drive respect because your team recognizes what you bring to the table. In turn, you also realize what they bring to the table.
You have to have an inner drive toward being better. This will help you have more concise PMs, even for the person that comes after you. It’s difficult to create a marker to help someone build their inner drive. This is something that will get fostered by those around you. Some of the effort comes from you.
You’ll also need recognition from management, supervision, peers and yourself. Always recognize and appreciate it when you do a good job.
Final Words
You need to understand that this is a process and you’re going to have fears. So start by following the process of setting up the foundation before creating a new maintenance plan. Then make a list of all the tools you need such as your knowledge, training, coaching, and practice. Take an assessment of yourself, your team, and the plant to make sure you know what you have. If there are any gaps, fill them in because the biggest thing that stops a maintenance plan is the fear of failure. We’re afraid of failure. But if you take into account all the factors like logistics, skillsets, and mental game, the fear of failure reduces.
With a maintenance plan, there’s going to be missteps or a trial and error period. But if you aren’t afraid of failure, you’re going to go to the starting line and start. Believe in yourself so that your maintenance marathon continues to grow and become easier. Once you start, you’re going to run through it and get better at it. Believe that each time you follow that route, you’re going to get better, finish stronger, and bring more people on board.
Eruditio Links:
Michael Mazur Links:
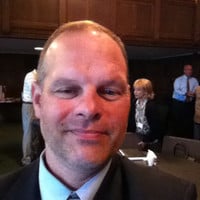
- Social:
- Link:
- Embed:
Rooted In Reliability podcast is a proud member of Reliability.fm network. We encourage you to please rate and review this podcast on iTunes and Stitcher. It ensures the podcast stays relevant and is easy to find by like-minded professionals. It is only with your ratings and reviews that the Rooted In Reliability podcast can continue to grow. Thank you for providing the small but critical support for the Rooted In Reliability podcast!
Leave a Reply