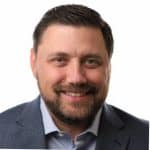
The Soft Side of Planning with Rick Clonan
We’re excited to have Rick Clonan back with us to talk about planning. He currently serves as an Implementation and Training Manager at Eruditio and as the Best Practices Chair for the SMRP. He’s been in the industry for close to 30 years as a technician, planner/scheduler, maintenance supervisor, CMS administrator.
In this episode, we will be discussing:
- What is maintenance planning
- What is the soft side of planning
- What is morale
- What’s the connection between morale and productivity
…and so much more!
What is maintenance planning?
It’s taking work from the identification side to the approval side. After it’s approved, it’s everything that happens right until the work’s scheduled for another calendar. It includes things like:
- Making sure your documentation is right
- Identifying all the steps
- Ensuring all the hazards have been mitigated
- Having all the necessary equipment for the job ready
It can be said as being the ‘What, where, and how’ of the job, with a very broad sense of the ‘Who’ referring to the skillsets required.
What is the soft side of planning?
Planning makes the workflow process more effective and efficient. However, if not done the right way, it impacts the morale, culture, and productivity of the crafts you’re planning for.
What is morale?
Everyone knows what it is. People know when they have good or bad morale. It can show up in the form of confidence, enthusiasm, or even hard work. Whatever the case, morale and productivity are directly linked.
What’s the connection between morale and productivity?
Studies have identified this relationship and people with high morale show:
- Better job satisfaction
- Better attendance
- High levels of motivation
- Collaborate and get along with co-workers better
Does the maintenance planning process impact morale positively or negatively?
It can do both. If you don’t plan correctly, you’re sending the wrong message to the crafts. There will be complaints concerning any changes to the ordinary system of doing things. However, asking the team will let you know how they feel about some of the changes. There’s common ground with this factor across different industries. If your team feels respected, then that can change the organization’s culture.
How does planning negatively impact morale?
Firstly, a good plan job consists of listed tasks being performed, and the steps needed to complete the work. Make sure all your safety hazards get listed and how to mitigate them. Make a list of:
- The asset
- Permits
- PPE
- Special tools and parts
- What you do when you run into a problem
- The expectations on how long the job should take
- Any additional documentation
- Post maintenance testing acceptance criteria
If there are no job plan instructions listed on the work order and, for instance, it says, “Replace the pump,” craftspeople need to complete the task with no standard for work quality. Some managers only care that the job gets dealt with in time. The problem with that is, although the work gets done, over time, it impacts the crew. Inexperienced workers will seek help from others around the plant, instead of their manager, which will take up other resources.
Without including the standard of the work we want to get done, it communicates that management doesn’t care how the job gets done. The lack of expectations plus the post maintenance acceptance criteria means that precision maintenance isn’t of importance. The mentality of getting things done quickly then comes about leading to laxity in following the safety guidelines. That makes reactive maintenance quite dangerous as people keep trying to cut corners. But planning ensures you don’t need to use shortcuts.
How to improve morale and productivity from a planning standpoint
During the research studies, people were asked what they liked about their jobs. Results showed that high performers had defined purposes and goals for the job they were performing. There was clear communication between individuals in the workgroup. They had confidence in completing the task since they had adequate training. So getting an improvement depends on:
- Communication
- Expectations
- Supplying the necessary skills for the job
It’s necessary to put people in positions where they’ll be successful and respected.
Is planning worth it?
Proper planning has its perks. So if you choose to plan, do it the right way. Not planning well will mean you only get some of the benefits of planning, which would still be a loss to your company. So ensure your planners get trained on best practices. Let them understand the importance of what they’re doing.
What determines success with the soft side of planning?
Start by setting those expectations of maintenance as a professional business, not just getting people to fix things after they break. Apply thoughtful effort to your assets instead of reacting to them. Also, make sure your technicians’ needs are well taken care of so that they feel valued. Avail them a feedback loop where they can report issues so that you’re always aware of the best way forward.
What to change in a typical planning process
You need to ensure all your planners get formal training to set a baseline expectation on what planning is. That way, regardless of the industry they get involved in, they’re aware of which standards have to be within a planning process.
In summary
Most of the time, the crafts see the work orders through the planning and scheduling process. So when they see a good example of what it is, they’ll be able to grasp the standard that’s expected of them. That trend goes feeding off into areas like the reliability or root cause analysis side of things, providing better failure data.
Eruditio Links:
Rick Clonan Links:
- Rick Clonan LinkedIn
- Rick’s email
- SMRP.org
- PMO with Rick Clonan
- Rick Clonan Eruditio Blogs
- Checklist Manifesto
- Making Common Sense Common Practice
- Engineer’s Guide to Preventive Maintenance
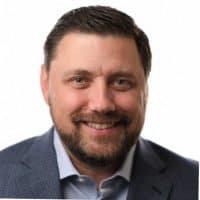
- Social:
- Link:
- Embed:
Rooted In Reliability podcast is a proud member of Reliability.fm network. We encourage you to please rate and review this podcast on iTunes and Stitcher. It ensures the podcast stays relevant and is easy to find by like-minded professionals. It is only with your ratings and reviews that the Rooted In Reliability podcast can continue to grow. Thank you for providing the small but critical support for the Rooted In Reliability podcast!
Leave a Reply