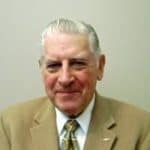
Where Did Procedure Based Maintenance Come From with Jack Nicholas
We’re excited to have Jack Nicholas with us. He started as a naval officer before becoming a senior service engineer and reserve naval officer. He’s founded companies, authored books, and helped with driving forward maintenance and reliability programs, predictive maintenance, and the other aspects that help deliver a holistic maintenance program.
In this episode, we covered:
- What is the SubSafe program?
- What is the role of training with PBM?
- What makes PBM successful?
- And much more!
What is the SubSafe program?
Also called the Submarine Safety program, this got implemented due to the USS Thresher’s loss, which happened in 1963, claiming 129 lives. The USS Thresher happened to be the most modern atomic submarine at that time. The event had a profound effect on the navy and, particularly, the submarine force.
Later that year, the navy was still designing modifications for nuclear submarines to try to prevent losses from probable causes suspected by the board of investigation into the disaster. During that year, Jack got stationed on the USS Nautilus, which had modifications mandated for it, with many more for the rest of the nuclear fleet.
Jack was assigned to study the board of investigation report by his commanding officer. This exercise was to determine whether what was mandated for the USS Nautilus was adequate. That way, they could revise their operating and maintenance procedures to accommodate the board’s findings. He took this duty seriously as they had lost four Nautilus members on the Thresher.
The SubSafe program’s centerpiece continues to be following the detailed written procedures and checklists developed to the letter. That’s by all personnel engaged in maintenance specified for components of all systems that affect submarine safety. These measures have ensured that no other US submarines have been lost due to maintenance problems involving the SubSafe program’s systems. This adjustment increased the equipment reliability and performance of the entire fleet.
In 2013, the SubSafe program received the Emerging Center of Excellence award. The award recognizes that no other program in the past 50 years has been more effective in the safety of the US Navy submarine force.
Was the SubSafe program the starting point of Procedure-based Maintenance?
The navy was already using procedures under the Maintenance, and Material Management system dubbed the 3M system. Started in the 1950s, it had two main parts.
- The Plan and Maintenance System was the first and provided detailed, time directed, preventive maintenance procedures in the form of maintenance requirements cards. The cards were mainly written by civilian contractors who employed ex-navy technicians with experience in their supporting systems.
- The Maintenance Data Collection System was the second part, and it required shipboard personnel to document repairs on the ship during operations. They would then report them to a central site for aggregation. The data would be made available to various navy ship support activities for analysis. This is where the Maintenance Study Approach, now called the Reliability Centered Maintenance Approach, came from.
Some procedures started before the SubSafe program. However, in the shipyards, the tenders or repair ships that supported the submarines saw it as a new revelation that they had to adopt. In the SubSafe program procedures, they carefully checked off one by one while taking special precautions during shift changes.
Why the emphasis on procedures from the SubSafe program?
There are many benefits to the organization and the individuals within. It enables there to be supporting policies, processes, and plans for carrying out these procedures. If you have a full set of policies, procedures, and programs, procedures represent the accumulated tribal knowledge of all past and present employees contributing to the content.
The legacy ensures the continuity of operations and sustaining functions. The accumulated knowledge in a set of procedures permits the organization to maintain tighter control of its evolution, protecting its reputation and other vital elements.
When used and followed, procedures can be the foundation that supports the employee regardless of today’s cares and concerns. Not everybody comes to the job in the same condition every day. But you want to have something to rely on that will get you satisfactory results even when you’re having a bad day.
They provide a measure of job security and confidence in what’s expected. It’s also a shield against the malicious, arbitrary actions of supervisors. Contract workers brought in through outsourcing arrangements can also make use of procedures developed by an organization.
How does the accumulated knowledge from past and present employees help drive improved reliability?
Military personnel frequently rotate from station to station. Their duties change as they get promoted. So, word of mouth, intuition, and job training was too unrealistic to meet safety and consistency in maintenance practices. Many personnel within these organizations have little or no knowledge in history or reasons for doing maintenance the same way every time. That’s why having procedures and supporting documents available makes the job of estimating costs and repairs and carrying them out on time within budget much more reliable.
What is the role of training with PBM?
There’s a perception that if you’re given a procedure, you don’t need training. However, it depends on the personnel’s skill level and experience to carry out the policies, process, plans, and procedures. And in some cases, also the work instructions that are derived from or supplementing them. This substantially reduces the cost and time of training on specific steps of the more complex tasks because systems are getting more complicated for various reasons. So properly prepared procedures are invaluable tools for training personnel new to a particular job whether they have experience with the maintained asset.
Of course, users must meet craft skill qualification requirements specified in the procedure before being expected to perform it after proper training.
Do you have to train your staff on the actual procedures?
They need to be at least briefed on the asset in advance and have the proper skillset. Personnel must also know what the policy and process are for non-deviation from a written procedure. Also, what to do if they perceive an impediment to carrying out any steps of the procedure.
Why hasn’t PBM taken hold in the private sector?
Some private-sector elements have adopted PBM. The most notable is the commercial nuclear power generation industry and some petrochemical manufacturing organizations. However, most organizations haven’t gotten the message yet on what this approach can do for them. But there’s hope with options like Prescriptive Maintenance, Virtual Reality, Artificial Intelligence, Machine Learning, and connectivity with the internet makes it possible to instruct and indoctrinate technicians on best practices.
What to do if you’re looking to implant PBM
It would be best if you adopted PBM procedures that can keep you and your organization from suffering from what other companies that don’t use PBM go through. The practices will help your organization stay more profitable than if you continue to rely on a craft’s skill with little or no procedures.
What makes PBM successful?
You can only create a PBM culture by ensuring that you have an effective compliance policy and a feedback and follow-up process that works.
Eruditio Links:
Jack Nicholas Links:
- Jack Nicholas LinkedIn
- Secrets of Success with Procedures Book
- Managing Maintenance Error Book
- Past Jack Nicholas episodes
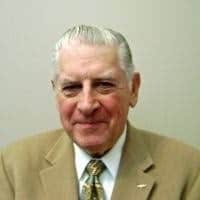
- Social:
- Link:
- Embed:
Rooted In Reliability podcast is a proud member of Reliability.fm network. We encourage you to please rate and review this podcast on iTunes and Stitcher. It ensures the podcast stays relevant and is easy to find by like-minded professionals. It is only with your ratings and reviews that the Rooted In Reliability podcast can continue to grow. Thank you for providing the small but critical support for the Rooted In Reliability podcast!
Leave a Reply