
Leading FMEAs with Bill Leahy
We’re honored to have Bill Leahy back to talk about Failure Mode Effect Analysis. He’s a principal instructor with Eruditio, having a background in manufacturing and the military. He’s been involved with maintenance and reliability for several years.
Today, we’re tackling important points such as:
- What is an FMEA
- Why do the FMEAs
- Who should lead FMEAs
- How to perform an FMEA
… and so much more!
What is an FMEA?
It’s a tool or process used to identify all failures within a system, process, or machine assembly. It first identifies the function, and then it looks at all the ways the function can be inhibited. By identifying the specific failures that do that, we can reduce the risk posed. The risk here refers to the probability of failure and the consequence.
Why do the FMEAs?
The great thing about FMEAs is that they can be done at different life cycle stages because they are a Root Cause Analysis tool. It provides unique transparency that helps you discover things that were maybe hidden failures or that the historical data isn’t capturing. It allows you to go beyond understanding the most common failures that occur by giving you a glimpse into the rare and dire events that may also occur.
Who should lead FMEAs?
You need an FMEA expert to lead this since it takes a lot of repetition and time. So, someone familiar with the process and equipment would be the best fit, possibly one who’s done multiple FMEAs, understands the process and has adequate facilitation skills to keep the group on track.
What team should you assemble for an FMEA?
Anyone with insight into the operation and understands the functions of what’s being evaluated. That’s whether it’s a process, design, or an asset during its useful life. Operators, for instance, understand failure mechanisms better than others. Everyone doing maintenance on the equipment, designers, vendors, and reliability engineers are more examples of people who can offer insight into the machine’s function.
Also, ensure you create an environment where operators feel welcome since they often get left out of the analysis despite knowing what’s being analyzed.
How to perform an FMEA
The most critical stage of an FMEA is the preparation stage. The facilitator can be a third party that comes in and helps, but they have to understand the equipment. Check the machine part by part to understand what it needs to do to achieve its output. From there, you can ask the group additional questions to get as much information as possible.
The preparation stage is also where you’ll prepare the environment where the FMEA will occur. You can have an excel template, a whiteboard, and flip charts prepared in advance for the meeting.
How to facilitate an FMEA
The template you use features the part, the problem, the cause, and such criteria that need to get filled in. Depending on the group you’re dealing with, you can choose whether or not to show them the template since some people can get intimidated if they’re new to FMEAs. You can even have a functional block diagram that gets filled in through the facilitation by the group.
From there, functions get set up. The failures, too much, too, little, and not at all, get set up. You measure the severity of those functional failures, focusing function by function on the most severe to start with. You’ll break down each of the components there and how they could fail. A long list of failure modes will then come up, which you’ll need to evaluate based on risk and detectability.
How long should FMEA events be?
You can’t have a boundary. You continue until you complete it, depending on the facilitator, the group, and the information you have from the beginning. Individual meetings can, however, be limited to two-hour blocks with a short break in between. Some FMEAs can be quick, while others can be long, drawn-out processes.
Other criteria to set up the FMEA team for success
The facilitator needs to start by establishing boundaries. These include the level of the hierarchy or analysis that you choose. That’s the best route to avoid wasting time, and it’ll also dictate how long the meeting takes.
Establish the various roles, such as who will be recording. You can have immediate data entry into Excel sheets, so everyone understands the sheets. Laying out the meeting etiquette and communicating the process means people can keep tabs as you move along.
For the facilitator, it’s essential to note down the FMEA steps. It helps you not skip over anything. It’s also something that everyone can go through to prepare themselves.
How do you know when to stop a session?
You need to set the right expectations from the start. You can work towards a condition, or you can work with time. Having an end in sight helps the group understand what’s going on. Clear goals enable the team to work without developing any anxiety about the process.
You can also look for cues within the group, such as:
- Lack of participation
- People folding their arms
- Slouching in their seats
At that point, you can send them on a break since you’re less efficient.
In case a debate ensues about a particular failure mode, stop it. Have a parking lot, which is an area where people can note down their thoughts so you can get back to them and address them at an appropriate time.
In summary
Getting people to FMEA meetings can sometimes be difficult, especially when they don’t understand its purpose.
So, ensure that you stay organized. Have and know your process, and stick to it.
You cannot prepare enough for FMEAs. Be prepared to create your style to do it since that will determine the level of success with any FMEA you perform.
To keep things on track, always note down your processes, so they are standardized each time you do an FMEA. That will also help you refine your processes better and faster.
Eruditio Links:
Bill Leahy Links:
- Bill Leahy LinkedIn
- Laws of Leadership with Bill Leahy
- Book: Failure Modes to Failure Codes
- Past Bill Leahy Episodes
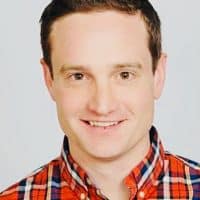
- Social:
- Link:
- Embed:
Rooted In Reliability podcast is a proud member of Reliability.fm network. We encourage you to please rate and review this podcast on iTunes and Stitcher. It ensures the podcast stays relevant and is easy to find by like-minded professionals. It is only with your ratings and reviews that the Rooted In Reliability podcast can continue to grow. Thank you for providing the small but critical support for the Rooted In Reliability podcast!
At the end of podcast, host mentioned to provide link for another podcast. I can’t find the link. Also, the page attached to “Past Bill Leahy Episodes” has no results.