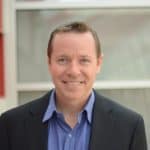
Decoding Mechanical Failures with Shane Turcott
We’re glad to have Shane Turcott to helps us understand more about decoding mechanical failures. He’s a principal metallurgist from Steel Image and is heavily involved in a lot of professional societies. Shane’s previously worked at a steel mill, a turbine company, and a failure analysis lab specializing in failure analysis. Steel Image was established in 2009 and deals with failure analysis, with a specialty in supporting reliability efforts in the refining industry, mining, energy, and heavy industries like automotive and manufacturing.
Today, we’re tackling important points such as:
- What is Fractography
- How to study failed components
- Difference between a Ductile and Brittle fracture
- How to become successful with Decoding Mechanical Failures
… and so much more!
What is Fractography?
Fractography is the science of examining fracture surfaces. When a part or metal cracks, how that crack leaves behind very distinctive features. By examining the crack features, you can find out how and why the part failed. That includes information on:
- How and why the part failed
- Where the crack starts from
- The nature of loading responsible for failure
- Clues on whether there are material or manufacturing defects
These are useful in an RCA, helping to determine the root cause of the failure.
Why study the failed component?
To solve a problem, you have to understand it. When a part fails, that failed piece of equipment has the most amount of information on why it failed. If you don’t analyze it, you’ll only be guessing how the part failed.
How to study failed components
There are two stages to this. The first is that every time a part fails, you’ll send a professional to examine the scene to get information. While talking about Fractography, it’s essential to note a gap in that stage since you could be looking more at the actual crack or fracture surface.
After triage, you can send it to a laboratory, which is the second stage. There’s a lot of lab-based equipment that gets used. These help to provide more physical evidence as to how and why a part failed.
What you can use for a visual examination
A lab staffed with trained experts will always be able to provide the most amount of information possible. However, a lot of RCAs are being completed without having access to lab support. So, if all you have is visual examination, you can still get a lot of information, with a bit of training, from studying those failed parts. In many cases, that information will prove useful in the RCA.
Main Mechanical failures with Metallurgic components
There are three main types. These are:
- Ductile overload – this is when a ductile material gets accidentally overloaded.
- Brittle – similar to glass shattering
- Fatigue – cracking that occurs over many loading cycles.
Ductile failure
Most of the metal used in structures and equipment tend to be ductile steel, which helps them absorb energy. When steel fails, it becomes a safety issue. So, one of the best clues of ductile overload is deformation. If you have a permanent shape change in the vicinity of failure, like stretching, elongation, necking, bending, twisting, or buckling, that’s a good sign that the part has had loading beyond its functional strength. Another pointer is that you may also notice a dull and fibrous fracture appearance that contrasts very well. Lastly, if you have enough tension in your failure, you’ll form 45-degree shear lips around your fracture surface.
Difference between a Ductile and Brittle fracture
These are both overload failures, but they occur due to different reasons. Steels used in structures and equipment are often selected because they’re ductile. Therefore, if it fails in a brittle manner, you have an issue very different from a failure due to ductile overload. So, for a successful RCA, you need to be able to determine that it’s brittle based on your examination of the fracture. After your diagnosis, you need a clean and systematic approach to identify what are the factors that caused a ductile material to fail in a brittle manner.
There are two primary categories of what causes brittle failures:
- Embrittlement phenomenon – during manufacture or service, something made your ductile steel permanently brittle.
- Environmental conditions – by exposing ductile steel to cold temperatures, it can become brittle.
These are also referred to as circumstantial factors. So, if you have a sharp notch, cold temperature, and impact the material very quickly, you can change a ductile material into a brittle state.
What is Fatigue failure?
Compared to the other failure modes, fatigue provides the most amount of information about how and why a component failed. It occurs from cyclic or repetitive loading, and the crack initiates and grows across. You can identify it through features like:
- Having a clearly defined initiation and crack progression, followed by the final ligament to fail or the final failure.
- Having crack arrest marks, also called beach marks.
- Having ratchet marks radiating from the initiation site, and tend to be smoother.
With a bit of training, all these things can help you identify that a failure was caused by fatigue. It can also give you a lot of clues as to where that loading source came from. Fatigue on steel only occurs if you exceed the fatigue limit, meaning your cyclic loading equipment must always stay below that limit. A fatigue diagnosis in the RCA will lead you to ask whether you passed the fatigue limit or the material was too weak. To determine this, you’ll use the clues on the fracture surface.
Do you need special equipment to analyze these failures?
There’s a lot of information you can get in the field or close to the field. The primary step is just using your eyes to examine. You can also get affordable tools like:
- A stereomicroscope, which gives a magnification of 5 – 30 times.
- A magnifying glass
However, it would be best if you focused on finding where the crack starts, and having magnification tools will provide you with more information.
How important is the preservation of failed parts?
It’s essential since it offers information on experienced failure. So, create a culture of repairing and keeping failed parts. Also, be smart about how you keep that part so that when you need information on it, it’s still in good condition.
Other Mechanical failure modes
There are four different families of failure modes:
- Mechanical – ductile, brittle, fatigue
- Wear issues
- Corrosion issues
- High temperature – for parts experiencing high temperatures like boilers
Some of these modes need more complex equipment to examine, but you still get a significant amount of information from a visual examination.
How to become successful with Decoding Mechanical Failures
Never rush Fractography and examining a failed part. If you’re not sure about something, take a day or two to sleep on it before coming back to it. Examine the failure area and everything on it. Do not develop tunnel vision on some of the most prominent concerns. Also, take your time with the examination until you’re comfortable with the outcome.
Why isn’t Fractography included in the reliability engineering curriculum?
Strangely, people get trained to investigate failures without including the skill set of looking at the failed part or the fracture surface. These are questions that organizations like SMRP that train and certify reliability engineers need to look at. It could be because, in the past, there were no resources for examining failed parts.
How to learn more about Fractography from skilled professionals
People need to hold, examine, and learn by using failed parts. Steel Image offers a course that inundates those who attend with several failures. These help them get very good at looking at broken parts and doing mock failure analyses.
Eruditio Links:
Shane Turcott Links:
- Steel Image
- Shane Turcott LinkedIn
- Decoding Mechanical Failures
- Decoding Mechanical Failures Course
- SMRP.org
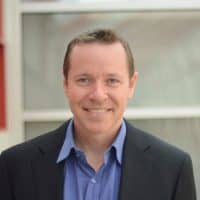
- Social:
- Link:
- Embed:
Rooted In Reliability podcast is a proud member of Reliability.fm network. We encourage you to please rate and review this podcast on iTunes and Stitcher. It ensures the podcast stays relevant and is easy to find by like-minded professionals. It is only with your ratings and reviews that the Rooted In Reliability podcast can continue to grow. Thank you for providing the small but critical support for the Rooted In Reliability podcast!
Leave a Reply