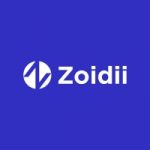
Moving from Paper to a CMMS with Jeff O’Brien
Welcome Jeff O’brien who is the cofounder of Zoidii CMMS
Jeff has worked with CMMS in manufacturing and consultancy for years and has currently launched their own application.
In this episode we covered:
- What prompted you to start your own CMMS?
- Why would organizations transition from a paper-based system to CMMS?
- How do organizations decide to make the transition?
What prompted you to start your own CMMS?
When the pandemic started in 2020 , consultancy work was affected. As an alternative, the team sought to create a cloud-based application that could host a range of tools with different functionalities.
Why would organizations transition from a paper-based system to CMMS?
The reasons include:
- They need a single source of information for ease of tracking issues
- A single point where everyone can come for knowledge (facility knowledge transfer)
- Records management to reduce reliance on human memory
- Organizational data protection
- Issues being fully tracked to completion
- Credibility for auditing purposes.
- Ease of measuring KPIs to determine actual value for resources invested.
How do organizations decide to make the transition?
- Some organizations naturally reach a point where they need the system to assist in maintenance management.
- Others come about as a result of trigger events e.g. audit failure or safety event.
- New management.
However, it is advisable not to wait for a trigger event. Start early by making your data ready for a CMMS.
What are the key factors to consider for a successful transition?
- Enough resources i.e. dedicate expert users of the equipment and create the time for them to be fully involved.
- A detailed implementation plan; discovery, configuration, training, go live, post-go-live, support and review.
- Data availability if none then can they create one? – data include: list of assets, checklists, PMs, intervals etc.
- Staff commitment; it is crucial to involve the team from the beginning,
What are the common mistakes during the transition?
- Failure to involve the team; you have to get the buy-in from the team.
- Choosing an overly complicated system.
- Organizations underestimating the importance of training in the implementation of a CMMS. Ensure that you dedicate enough time and resources in training. Involve the vendor in customizing the training to your organizational training needs.
How much effort should be put up front (in training, data preparation, choosing a system)?
Intending to get everything right at once rarely works. Instead, start by making small steps and build up from there.
Get the critical assets onto the system. Add their PMs, and encourage the team to be processing the assets’ work orders from the system. After noticing success, you can replicate the process on other machines and functionalities.
How do we get the staff onboard?
The strategies include:
- Help them come to the CMMS solution by themselves by perhaps asking how to prevent a work order being skipped, missing records etc.
- Explain the “why” we need a CMMS. Reasons could be high maintenance budget, skipped work orders etc.
- Get the team involved in the evaluation of the CMMS at the selection stage.
- Select CMMS champions for training and let them show others that It is practical and beneficial
- Make the use of CMMS a daily routine for certain processes. E.g. only accept work orders coming from the system.
- As a leader set a good example by always using the system.
How do we expand the use from pilot assets to the entire facility?
- Repeat the process in other functions of the facility
- Get the vendor to help in replication in other functions
What piece of advice is there for those struggling with CMMS implementation?
- Do not try to do it all at once; take small incremental steps.
- Start with basic functions such as work order creation then improve
What makes the biggest difference?
- Only choose a system based on your needs; decide on what you want to achieve and only focus on those.
Key takeaway
- Implementing CMMS shouldn’t be complicated.
- Assign dedicated resources
- Ensure staff are involved
Eruditio Links:
Jeff O’Brien Links:
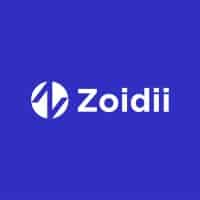
- Social:
- Link:
- Embed:
Rooted In Reliability podcast is a proud member of Reliability.fm network. We encourage you to please rate and review this podcast on iTunes and Stitcher. It ensures the podcast stays relevant and is easy to find by like-minded professionals. It is only with your ratings and reviews that the Rooted In Reliability podcast can continue to grow. Thank you for providing the small but critical support for the Rooted In Reliability podcast!
Leave a Reply