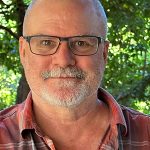
270 – Where to Start with DfM & DfR with Fred Schenkelberg
Welcome Fred back to the podcast. Clients are starting to realize that they have to design their systems properly while paying attention to certain tradeoffs. However, tell us where they should start; whether to design for reliability or maintainability.
Before starting, the team has to look at their business goals and decide whether the acquisition of any system or a piece of equipment assists to that end. It has to be a business decision.
Pay attention to:
- The environment of usage
- The cost of ownership; is it going to be profitable?
- The usage rate of the tool
- Type and quality of the tool
In this episode we covered:
- Understanding the tradeoffs is essential while keeping the important things in mind. Where do we place time and resources? Reliability or maintainability?
- Once they have chosen to rely on data and experience? Where do they start in designing for maintenance or reliability?
- Create basic standards. Otherwise, the advanced things like the right model shall not matter. Basic aspects such as a complete bill of material that can be uploaded on to the CMMS, documentation should be taken into account.
The one thing I have noted in many cases is the inadequate control of a tool’s specifications. It is necessary to ask what tool is needed and why. Do we need it for repeatability and what is its maintenance schedule? Asking this would completely change the decision making process.
If high volumes are demanded, then the tool or process should be designed for resilience and redundancy.
Understanding the tradeoffs is essential while keeping the important things in mind. Where do we place time and resources? Reliability or maintainability?
In making such decisions, most people resort to the theory of constraints: focusing on bottlenecks and ignoring the rest. For instance, I came by a process where the team paid attention to a bottler that can fill 450 bottles per minute and a labeler that can label 1000 in as much time. They diverted all their time and resources on the bottler yet the labeler could be down from time to time for 6 hours since it was ignored. They were missing on an opportunity by ignoring it.
They needed to rely on data and experience in making such decisions.
Once they have chosen to rely on data and experience? Where do they start in designing for maintenance or reliability?
Let’s say you have properly designed your reliability or maintenance program properly. You also have the capability to collect and analyze data.
What you shouldn’t do is bring in a piece of equipment that you do not have the tools or the expertise to maintain. Use what you already have to find an equipment that fits perfectly.
Pay attention to basics such as the brand. Involve the engineering team in finding what fits perfectly.
Create basic standards. Otherwise, the advanced things like the right model shall not matter. Basic aspects such as a complete bill of material that can be uploaded on to the CMMS, documentation should be taken into account.
The decision making team needs to include the engineering people and not the vendor. The vendor has no idea about the usage and the working environment for the equipment.
The operating context needs to be specified, right?
Yes. Also define what you are already good at or the need to learn. Perhaps add new staff with a different set of skills.
Note that buying from the lowest bidder does not necessarily mean a low cost of ownership.
Just because the standards demand that you always purchase from the lowest bidder does not mean that you fail to pay attention to the cost of maintenance.
Think about the specifications, your operational requirements and storage of parts. For instance, there is no need in purchasing motors from different companies. Buying from different suppliers would mean purchasing and storing different spares. Stick to one brand to optimize the usage of parts.
Thinking about the long-term costs of maintenance is critical.
The best place to start is perhaps to read James’ book “Design for Maintainability”.
A lot of basics such as paying attention to equipment specifications and operational context are in the book. There are other books by the same lead authors such as “Design for Reliability”.
The language in which you receive specifications and other documents is also essential. However, such are decisions that you need to make early before making the purchase.
Eruditio Links:
Fred Schenkelberg Links:
- Fred Schenkelberg Linkedin
- Book: Design for Maintainability by Louis Gallo, Jack Dixon, James Kovacevic
- Accendo Reliability
- Speaking of Reliability Podcast
- Past Fred Schenkelberg Episodes
Rooted In Reliability podcast is a proud member of Reliability.fm network. We encourage you to please rate and review this podcast on iTunes and Stitcher. It ensures the podcast stays relevant and is easy to find by like-minded professionals. It is only with your ratings and reviews that the Rooted In Reliability podcast can continue to grow. Thank you for providing the small but critical support for the Rooted In Reliability podcast!
Leave a Reply