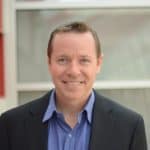
275 – Decoding Mechanical Failures: A class experience with Shane Turcott
Welcome Shane who is the author of Decoding Mechanical Failures. More about Shane and Steel Image:
Shane is a mechanical engineer who founded Steel Image, whose primary business is analyzing information on broken parts: how it failed, mechanisms of failure, and whether the part was built correctly or not.
They avail all this information to aid those conducting RCAs.
In this episode we covered:
- What is Mechanical Failure?
- What is the process of diagnosing the failures?
- How do the “boxes” work for fractures e.g. brittle?
So all the information is available for those at the site level?
Yes. The basic information in conducting such analysis is learnt at apprenticeship yet it is not well disseminated across the other engineering disciplines. I resorted to disseminate this knowledge to other industries.
You made the shift from in-person to virtual training. Were there challenges in the conversion?
Yes, there was. In-person training uses 40-60 broken parts physically present and being examined by learners, which is engaging. Doing this online is a challenge and people are easily bored thus affecting retention.
To avert this, we prepared a workbook with 36 fracture surface images to teach what to look for, finding initiation sites, and commenting on the loading level. Etc.
What is Mechanical Failure?
They are fractures as a result of mechanical loading; cyclic loading, impact loading and overloading (without the contribution of corrosion, high temperature damage mechanisms)- entirely applied load.
It is essential as it is the first place you look at without specialized equipment and obtain the most information regarding the failure.
What is the process of diagnosing the failures?
- Diagnose the failure mode
- Find how to use the diagnosis in the next steps for instance, did it fail due to fatigue as a result of stress concentrators. Perhaps the cyclic loading was greater than the material strength.
Investigate if the loading was too high and was it expected or not.
How do the “boxes” work for fractures e.g. brittle?
Once the diagnosis is done, we give a series of factors to consider e.g. if diagnosed as a brittle fracture then it could be ductile; consider the following:
- Temperature- changes can take a ductile steel into transition
- Rate of loading; if slowly loaded versus letting the load drop with a high impact. Also the presence of stress concentrators
- Material flaws: brittle or have sharp corners.
The training outlines how to identify the causes of failures.
Yes, it does. You have to test for both fatigue (Strength-based) and toughness. Differentiating the two helps in RCAs.
Why do most people find it difficult to study the fractures?
Most people do not know that they can do it. It can be difficult but learning the basics makes a big difference.
People often resort to switching from one tool or part to another without finding the actual cause of mechanical failures.
The only way to be sure of why the failure happened is by analyzing all the data around the fractured part. Reliability managers could use this analysis as a key tool in finding reasons for failures.
Why do you think this information is limited?
Enough effort and time was not spent in preparing enough material to communicate. To communicate the concept, you have to collect a lot of failure data to create a good package to disseminate.
It is inarguably a big step in improving RCAs in a reliability and maintenance engineering
The tool does not replace those available but shall only make them better.
If the failure has been identified as fatigue; where did it start from? Should the area be loaded or not? Are there unexpected stress concentrators or material flaws? Will the damage be introduced on a new part?
Without answering these questions then, it is often guess work
Carrying it out is essential because it needs to be done at the beginning of the failure analysis. It forms the foundation of all that follows in RCA.
It eliminates guess work in critical matters such as safety and product loss.
It is impressive because you do not need specialized equipment.
Define the threshold upon which you move from a basic visualization to a laboratory analysis. However, most of what happens in a lab is equally visual (which is critical) albeit the use of a microscope or a magnifying glass.
Challenge is the storage of a broken part; most people leave them to build up junk
Basic: Put it in a plastic bag, label it and date it.
Key takeaway
- To understand why it failed you must understand how it happened.
Eruditio Links:
Shane Turcott Links:
- Past Episodes with Shane
- Steel Image
- Shane Turcott LinkedIn
- Decoding Mechanical Failures
- Next Online Decoding Mechanical Failures Course – October 22, 2021
- Decoding Mechanical Failures Course
- Decoding Mechanical Failures Book
Rooted In Reliability podcast is a proud member of Reliability.fm network. We encourage you to please rate and review this podcast on iTunes and Stitcher. It ensures the podcast stays relevant and is easy to find by like-minded professionals. It is only with your ratings and reviews that the Rooted In Reliability podcast can continue to grow. Thank you for providing the small but critical support for the Rooted In Reliability podcast!
Leave a Reply