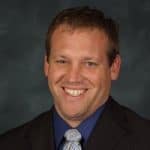
The Low Hanging Fruit of Lubrication Improvements with Devin Jarrett
It’s my pleasure to welcome Devin Jared to the podcast. Devin is a success manager at Noria.
He has worked as a processes guy, made a transition over into the technical team, managing projects, then I stepped into the technical consultant role, then now a success manager. He officiates football on the side as a hobby.
In this episode we covered:
- Where do we start with lubrication?
- What are some of those low hanging fruits you typically see that we need to address in organizations?
- Would you consider filtering oil before putting it in equipment low hanging or is that a little bit more advanced?
Where do we start with lubrication?
Create awareness that we’re doing something about lubrication.
What are some of those low hanging fruits you typically see that we need to address in organizations?
- Labeling equipment or labeling lubrication points
- Color-coding things
- Calibrating your grease gun. How much grease really comes out with a pump of grease.
- Create awareness; how many people have you talked to?
- How much grease do you put inside the bearing?
Would you consider filtering oil before putting it in equipment low hanging or is that a little bit more advanced?
Purchasing a bulk system; a storage system that does it all and re-circulates inside of a tank is an easy thing to do, but it’s very costly, upfront. Getting a filter card and hooking it up to a drum of oil is relatively inexpensive.
It totally depends on where you are, and how much you want to start with. You need to understand that clean oil coming in from a drum isn’t always clean enough for our equipment. Utilize some time to filter and remove solid contaminants, water, and find a good place to store it. Ensure it’s not getting rained on. Identify who is going to drive the program and really push for things to happen. Take your time to implement it and get one thing across the finish line. Ensure proper maintenance of the lube room.
Do we have to develop some sort of standards or processes to make sure that it’s sustainable, or does that come a little bit later?
As you’re putting things together, it’s great to have a standard. If we’re going to do calibrating grease guns, lets have a standard on how we’re going to do that.
- Make sure we have a postal scale and a sheet of paper we’re going to zero it out
- Determine how many pumps we’re going to put on that grease or on that piece of paper
- What’s that number?
- Have a solid process for that. Decide to dedicate a grease gun to a specific grease because obviously a grease with a 460 in it is going to pump different than a grease that has a 150 in it.
- Document the things that you’ve made and the changes
- Have periodic checks to make sure that we’re still doing what we were supposed to do
Do all these happen at once or is it little bit of phases?
On one hand, yes, you can implement a bunch of things. The one downside of that is making a very drastic change to a lot of people. If you’re going to just dive headfirst into all of it, you’ve got to remember that it’s not just about your equipment or writing down the documentation side of things. You’ve got to bring your people along with that. That’s sometimes a longer journey than what we think it should be but it’s worth it. If you can’t get people to buy in and follow it, it’s not going to be successful.
- Have a realistic plan
- Identify the things that you want to accomplish
- Put a timeline on it
- Break it up a little bit, focus on a particular machine type.
How do we quantify some of these improvements from the loop program so we can just define the next round or next evolution of the program?
Sometimes when we make a change to a piece of equipment, we’ll stick with 3d bull’s eyes. Before you put on that 3d bullseye, more than likely you were unscrewing a level plug.
- Do a 3d bulls-eye inspection
- Check oil level
- Check oil clarity
- Look for bubbles in the sight glass
- Does the oil Keller look the same?
- Checking in a sight glass every time someone walks by
It’s those little things that can make a huge difference. You’re not going to maybe see it right away. After a while you may realize that the gearbox that we used to change every five years has now been there for 15 years and we haven’t had any problems with it.
What do you want our listeners to take away from the conversation today?
- Don’t be afraid to step out there and do something. Even if it’s not right, at least you’ve tried
- If you don’t know the answer to something, there are tons of people out there that know the answers. And all you got to do is ask
Eruditio Links:
Devin Jarret Links:
- Noria.com
- Devin Jarrett LinkedIn
- Djarrett@noria.com
- Devin Jarrett Phone Number – 918-749-1400, 918-392-5070
- 3-D Bullseye Sight Glass
- Lubrication Awareness Training
- Machinery Lubrication Magazine
Rooted In Reliability podcast is a proud member of Reliability.fm network. We encourage you to please rate and review this podcast on iTunes and Stitcher. It ensures the podcast stays relevant and is easy to find by like-minded professionals. It is only with your ratings and reviews that the Rooted In Reliability podcast can continue to grow. Thank you for providing the small but critical support for the Rooted In Reliability podcast!
Leave a Reply