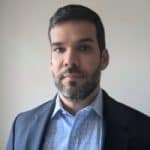
Risk Based Inspection with Ricardo Santos
It is my pleasure to welcome Ricardo Santos to the podcast, a Senior Manager at Deloitte.
In this episode we covered:
- What is RBI – Risk-Based Inspection?
- When would organizations want to leverage risk-based inspections over RCM or something else?
- Why do organizations want to go about implementing RBI process?
What is RBI – Risk-Based Inspection?
It’s basically a risk assessment and management process, where the risk is managed primarily through inspection. So it’s a bit similar to RCM. But the difference in my opinion, the eye is of inspection is where instead of managing the risk throughout the various methods that our CMA offers, you’re only focusing through inspection, but it’s a focus, but not completely excluding everything else. It’s just that the main way of managing the risk is through inspection.
When would organizations want to leverage risk-based inspections over RCM or something else?
RBI should be used always, so that the inspection program that the company has in place is supported by engineering principles. People should not be inspecting things just because regulations say so, or because of company procedure says so. It is better to start that process prior and prioritize on your inspections based on risk.
Why do organizations want to go about implementing RBI process?
RBI is often sold as a cost saving tool, that could be one of the outcomes, but the real reason why you wouldn’t want to use RBI is to ensure that you’re inspecting the right equipment. That right time is basically going back to the example of the RCM, where you can ensure you can follow all these instructions from the manufacturer or from the RCM. It allows us to prioritize our activities, reduce risks, cause we’re inspecting the right things at the right frequency and not inspecting things we really don’t need to all those different aspects of it.
What is included in an RBI program?
You could use it for any type of assets. We can use it for assets, that crowed assets that have a degradation mechanism in place.
Do we have to go through and define all the failure modes, the rates of failures, all this technical stuff, or is it a little bit more simplified than that?
Now people get caught up often with a probability and consequence calculation where that differentiation or offing is made of they offer three levels. RBI is a management process. So it can be used for any asset where the risk is managed primarily through inspection, but there are a few steps along the way. You need to assess the probabilities and consequence and how you calculate. Organize the company around how the inspection is planned, how do we execute them? How are you managing anomalies or concerns? How do you manage temporary repairs, with that asset class of pressure equipment?
If an organization wants to move into risk-based inspections, how do they go about doing that?
The first step I would recommend is to get first buy in from management. Explain to engineering, the maintenance, reliability planning teams, so that when they still start seeing these terms coming up, risk, probability, due dates, etc, they all know what it’s all about. Have a complete asset register, have a complete register. Collect technical data and that that beat can get a bit overblown with all the details that you can capture. Finally, you have the assessment part. When you define your correlation, the condition mechanisms, you collect your inspection history, then you start your assessments.
What is it ALARP? And how does that fit into risk-based inspection?
It’s really ALARP is just striking that balance and what the courts would see as you reasonably put forth due diligence and prevent this failure.
How do we go about setting up the frequencies?
Based on risk, you have the multiplication of probability times the consequences, and then you get your risk. The probability of failure increases over time as you have your workforce or your course, and as that probability of failure increases over time, you have your increasing risk. We estimate the frequency, or the next inspection date based on when those assets and the risk on those assets reaches that threshold value above the acceptable level. Every company has its own acceptable risk level. If the risk is very high, then that would call for a more extensive examination. And if the risk is connectively low, then you can afford to do other things.
What type of data do we need then?
In the case of thinning degradation mechanisms, you will go with Grogan rates. That would be number one data to have, but for cracking degradation mechanisms or the so-called environmental, then you will have other factors like process variables, temperature, pH to determine the iteration.
What happens if we’re missing some of those key data points, if we don’t have good Grogan data or other degradation data?
The recommendation will be to go to the latest data point. You’ll try to infer for any changes on the process conditions over that time. That will allow you to estimate a conservative corrosion rate and a conservative degradation or damage factor for the environmental factors in front of the environmental leadership mechanisms. Extrapolate that from the last known inspection to the present day and see the rescue.
Can we leverage subject matter expertise to supplement some missing data?
It’s not one person running the RBI software in the room. You need to have the process engineers in the room, a materials engineer, some metallurgists, uh, you have your inspectors, and then you look at all that data that I’ve described and then they make the call.
Do you have any words of wisdom to part with and provide to them to help them along this journey?
I would like to emphasize again on the complete asset register and to focus on the process. It’s very important to know how the inspections are planned. All that in my view is way, way more important than to be super precise with the probability and consequence, stipulations, whatever you calculate can fall apart.
What’s the one thing you want our listeners to take away from the conversation today?
I think it’s important to explain the methodology and the process to all the stakeholders and say that you’re rolling out a project, you’re studying a project. Engage all the stakeholders. Make sure that there is an understanding on the setup, the level of risk in the organization. It’s important to get an agreement with process safety. The other thing is on the methodology. When developing a methodology, it doesn’t have to be an advanced algorithm, but it has to be approved by a registered engineer.
Eruditio Links:
Ricardo Santos Links:
- Ricardo Santos Linkedin
- Deloitte Australia
- RBI API 580 API 580
- Inspectioneering.com
- Asset Integrity Intelligence
- RCM2 by John Moubray
- RCM3
- Normal Accidents: Living with High-Risk Technologies Revised Edition by Charles Perrow
- The Failure of Risk Management: Why It’s Broken and How to Fix It 2nd Edition by Douglas W. Hubbard
- Center for Chemical Process Safety
Rooted In Reliability podcast is a proud member of Reliability.fm network. We encourage you to please rate and review this podcast on iTunes and Stitcher. It ensures the podcast stays relevant and is easy to find by like-minded professionals. It is only with your ratings and reviews that the Rooted In Reliability podcast can continue to grow. Thank you for providing the small but critical support for the Rooted In Reliability podcast!
Leave a Reply