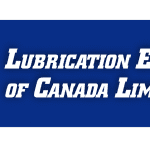
Understanding Oil Analysis with David Pedden
Oil analysis is a very important part of any lubrication program. Oil is an essential ingredient for your equipment and provides a strong bottom line. When there are contaminants in your oil, your equipment fails more often than it is supposed to. That means you have to get more spare parts, buy more lubricants and deal with increased downtime. When the condition of your oil is good—that is where the oil analysis comes in for making sure it is—your machines work properly. In a result, you save a lot of money by purchasing the right amount of oil.
Anyways, no company likes to welcome unseen failures when you can reduce them by performance condition-based monitoring. It not only reduces labor costs, it also increases your production and rid of you a lot of repairs that you were going to make. The only job a lubricant has is to protect the equipment and the only way to ensure that is through a good oil analysis program. When you are regularly checking your lubricant, it means you are aware of the internal and external condition of your equipment and that is the first step towards preventive maintenance.
You can start working on your oil analysis requirements by determining what sort of gear boxes are in place? Which ones are critical and to what sort of environment is your equipment disposed to. Once you have decided your monitoring goals, you can start taking samples. These samples should be taken carefully, preserved to not add more additives to it and then send them for testing in a timely manner. You can’t just take it from any valve, you need to take care of pressure issues, and know what sort of system you have in place.
You have to be consistent with the sample taking by knowing exactly when, how, and from where you are going to take an oil sample. It sets trends for everyone and they know which data to be collected and how the testing process is going to move forward. There are basically three levels for testing the cleanliness of oil. In the first level, you check for the additives in the oil which results in contamination within your system and with other connected systems as well. In the second you have to check for variation in the viscosity of your systems because it results in breakdowns. You need to check for particle counts, the concentration of different metals and coolant leaks as well in order to prevent a certain component failure in your equipment.
You don’t have to perform every test to check the integrity of your system. If you get the imminent results from level 1 tests, there is definitely no need to go to the next two levels. The last thing is to interpret the oil analysis report correctly because is going to affect your whole maintenance program as you go about making the decisions.
Eruditio Links:
- Eruditio, LLC
- A Smarter Way of Preventative Maintenance – Free eBook
- Maintenance Planning & Scheduling: Planning for Profitability Video Course
David Pedden Links:
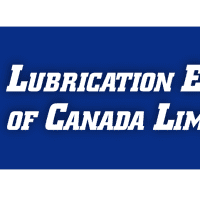
- Social:
- Link:
- Embed:
Rooted In Reliability podcast is a proud member of Reliability.fm network. We encourage you to please rate and review this podcast on iTunes and Stitcher. It ensures the podcast stays relevant and is easy to find by like-minded professionals. It is only with your ratings and reviews that the Rooted In Reliability podcast can continue to grow. Thank you for providing the small but critical support for the Rooted In Reliability podcast!
Leave a Reply