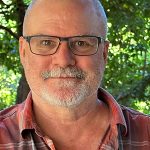
Calculating the ROI with Fred Schenkelberg
The reliability and maintenance process is never static in the organizations. There’s always something going on around and there are many activities being performed in the company. Now, these activities take time and need money to be done successfully. There are many activities in this list that will cost you millions sometimes. So, how do we get that kind of investment from our financiers? Some of the stakeholders can be convinced by merely good talks and promises of great success but the technical personnel who have spent all their lives running businesses, they can’t be persuaded by such means.
You need to get them the estimates and detailed goals list for even getting their attention. You will be asked to justify the money you are asking them to invest in the project and they will need numbers and strong figures in the presence of finance experts of your organization. This is where certain and precise calculations are needed to get people to invest in the reliability related work. You have to make decisions and be creative about it. Money isn’t always the answer but you the end result is always the Revenue and there are alternative ways to get that ROI.
Most of the time, companies invest in the tasks that will reduce the downtime they are always facing and the only way to do that is to invest in training your employees, improving your systems, and doing PM-Optimization. There are different standards of success in the eyes of different investors but the end goal is always getting that Return on Investment. If you have a good and experienced team after training them and getting those resources for them, they will lead you to save a lot of money and increase uptime of your machinery. That is certainly a good enough output to get all the future investment you will need.
There comes a time when you don’t have solid estimates but if you get together everyone in the same room and you are able to convey the technical assumptions that you made in the right way, there are still chances, you will get the funds for the task. It is very important to have the support of management because they believe in it if you do. It is surely a good practice to have some rough percentages of inputs and outputs but overall, if you work together as a team, you will get there.
Whether an activity gets funded or not, also depends on the culture of the organization. Some organizations prefer learning, educating, and training employees more than anything else because they know the true worth of that long-term investment. As a reliability engineer, you should always ask yourself, is it worth it? All the effort and money that we are going to invest in this task. If it is, then you must believe in it and get your company those improvements that are beneficial for every single employee in the end.
Eruditio Links:
- Eruditio, LLC
- A Smarter Way of Preventative Maintenance – Free eBook
- Maintenance Planning & Scheduling: Planning for Profitability Video Course
Fred Schenkelberg Links:
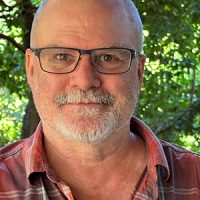
- Social:
- Link:
- Embed:
Rooted In Reliability podcast is a proud member of Reliability.fm network. We encourage you to please rate and review this podcast on iTunes and Stitcher. It ensures the podcast stays relevant and is easy to find by like-minded professionals. It is only with your ratings and reviews that the Rooted In Reliability podcast can continue to grow. Thank you for providing the small but critical support for the Rooted In Reliability podcast!
Leave a Reply