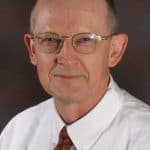
Reliability with Ron Moore
True enough, a reliable plant is a safe, cost-effective, and environmentally friendly plant. In compliance with safety laws and with workplace accidents becoming increasingly common, workplace safety is apparently one of the biggest challenge employers are facing today.
When an employee is injured during work, company has the moral and legal obligation to cover for medical and insurance costs, worker’s compensation, survivor benefits, lost wages, damaged equipment and materials, production delays, other workers’ time losses, selection and training costs for replacement workers, and accident reporting.
According to OHSA, each year, approximately 6,000 employees in this country die from workplace injuries while another 50,000 die from illnesses caused by exposure to workplace hazards. In addition, 6 million workers suffer non-fatal workplace injuries at an annual cost to U.S. businesses of more than $125 billion.
Furthermore, U.S. Bureau of Labor Statistics reported that in 2016, there were approximately 2.9 million nonfatal workplace injuries and illnesses reported by private industry, which occurred at a rate of 2.9 cases per 100 full-time equivalent (FTE) workers. Nearly one-third of nonfatal occupational injuries and illnesses were of a more serious nature and resulted in an average of 8 days away from work (DAFW).
Translated financially, the key figures above equate to businesses spending annually around $170 billion on costs associated with occupational injuries and illnesses and $60 billion from lost productivity from injuries and illnesses costs (OHSA); and the most serious workplace injuries cost U.S. Companies $59.9 billion per year, according to 2017 Liberty Mutual Workplace Safety Index. These do not even include the substantial penalties government imposed for employers who violate safety regulations who might also be liable to face criminal charges.
As you can see, implementing workplace safety may not be inexpensive, but with the right reliability programs and practices in place, injury-related costs can be mitigated and reduced. There’s ample online and offline literature that links reliability and safety. Needless to say, it doesn’t take rocket science to understand that safety provides a competitive advantage to the business. Sadly, most organizations would claim that workplace safety is their top priority. However, a closer look at their operational reliability reveals practices that are not at par with the required standard. For a few billion dollar companies, reliability constitutes only roughly 10% of their budget.
Although each organization needs to have a good maintenance program, reliability is not all about maintenance. “It requires a comprehensive approach, design procurement, operations maintenance. Expecting maintenance to deliver reliability is like expecting mechanic in garage to make your car reliable. If you don’t drive it, if you don’t do condition monitoring, it’s difficult for it to be reliable,” said Ron.
Furthermore, reliability is all about defect elimination in process or equipment. According to Ron, if you don’t have good reliability, then you are likely have good safety and less likely to have low cost and less likely to have better quality and less likely have good environmental performance. So, reliability is really the foundation of operational excellence and all these other good things come with it.
When asked if there’s any difference in global or regional practices, Ron sees more similarities than differences across sites. In Asia, in tends to be more hierarchical and independent but may require communication across cross-functional boundaries. In Western Europe, it’s less structured. In the US, it’s not given that much esteem and therefore it receives less resource attention since when executive think of maintenance, they equate that with costs and downtimes and they don’t want any more of that. They simply think they get lower costs and better performance by simply cutting those costs when simply the solution is remove the defects and improve the process.
So, how do we convince executives to make the time and money available for process improvement? According to Ron, it takes a holistic approach, with the elements of change management, executive sponsorship, and employees’ involvement mixed in. Obviously, the most difficult part of change management is recognizing change, that’s why to get executive buy-in, you need to articulate your prospective business case. Strategies have to be articulated, commanded, and supported. Everyone needs to be involved, not just the maintenance. High reliability is production-led with maintenance having support functions. Executive should not just demand but should support as well with tools and resources.
Also, setting OEE percentage goal without doing anything on operating practice or design is a wrong approach. As mentioned previously, reliability should be geared towards defect elimination and loss management. If you manage the losses, the numbers will be at where you want it to be. Categorize and measure failures/defects/losses. Focus what the losses are and manage those losses. Operations and maintenance should own up to schedule maintenance compliance. Define properly roles and responsibilities and promote sense of shared responsibility across functional boundaries to facilitate cooperation and teamwork. Also, educate the workforce about RCM and failure mode may not be necessary. Their involvement and support will suffice.
As far as OEM recommendations are concerned, you don’t really have to follow everything. Just tweak and apply those recommendations that works for your organization based on your operating context.
In essence, reliability is not just about maintenance. Reliability is about procurement, operations, design, and maintenance working collectively towards common purpose with shared purpose with leadership that drives, demands, support, and collectively engages everyone towards common goal. Functional areas should work together to eliminate defects; so that overarching philosophy is paramount. It’s all about taking holistic approach to achieve a good reliability program.
Eruditio Links:
- Eruditio
- HP Reliability
- A Smarter Way of Preventative Maintenance Free eBook
- inspired Blended Learning (iBL®)
- James Kovacevic’s LinkedIn
Ron Moore Links:
- Phone: 865-765-7607
- Email: ronsrmgp@aol.com
- SIRF Roundtables
- Reliable Manufacturing
- Recommended Readings:
- Books by Ron Moore
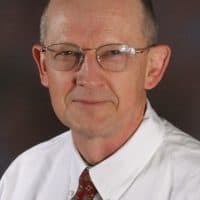
- Social:
- Link:
- Embed:
Rooted In Reliability podcast is a proud member of Reliability.fm network. We encourage you to please rate and review this podcast on iTunes and Stitcher. It ensures the podcast stays relevant and is easy to find by like-minded professionals. It is only with your ratings and reviews that the Rooted In Reliability podcast can continue to grow. Thank you for providing the small but critical support for the Rooted In Reliability podcast!
The great statement for a reliability is :” Reliability is about procurement, operations, design, and maintenance working collectively towards common purpose with shared purpose with leadership that drives, demands, support, and collectively engages everyone towards common goal.
Functional areas should work together to eliminate defects;
so that overarching philosophy is paramount.
Thank Ron Moore and James Kovacevic
I am one of the lucky ones to step into Reliability Engineering after joining his workshop in Fremantle in Western Australia in 1997. Thank you James for putting this article together.
He is the Guru in Reliability world.