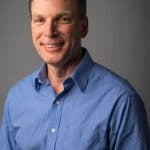
How Work Management Improves Reliability with Owe Forsberg
Work management directly impacts the reliability function within the organizations. Work management means to utilize your resources in the best way possible to drive improvement and performance. These resources may include spares, systems, and all the other tools that can help you maintain the equipment.
In this episode, we covered:
- What work management is
- How work management improves reliability
- What are the resources in work management
- What happens in an organisation without proper work management
- And much more!
It starts with having a predictive maintenance program. When you do regular PM compliance, you come to know of the issues that might occur later on. Once you have identified potential risks to your equipment, you can plan and schedule your work order so that the problem would not occur. Even if it does occur, you would be prepared for that. It is important to plan your work order on the basis of what you find during PMs. You need to know what you are dealing with and then you can plan your work-order to do the necessary maintenance. There should also be some sort of performance measurement mechanism based on the KPIs. When you plan your work, you know what time you are going to do specific tasks, who is going to do it, and how they are going to do it. The most important part is that you can set up an accountability measure.
When you know what went wrong, you can take precautionary measures to stop it in the future. You can measure your performance every once in a while and then, do things differently to improve your reliability from there. Leadership plays a huge role in driving the performance measurement. They can talk to their team members, get their suggestions, and train them when needed. They are the ones who really make the best use of resources and manage work by defining clear roles and responsibilities. These are some of the things that organizations can do to improve their reliability programs.
The work management starts with mapping out the business process and then make sure that everything is implemented in a planned way and time. The few steps of work order management are making a work request, making it a business process to be carried out, planning it, scheduling it, and then assigning it to someone who can get the job done as it should be done. You need to take care of the workflow in the organizations and anyone should be able to make a work request especially the operators who work with machines the most.
No matter how much you plan your work and schedule it, it won’t work if the leadership part is missing something. The management can plan work, prioritize it, and then give the instructions to get it done but it all falls apart if no one is going to follow the procedures and instructions. It all comes down to people and maintenance and only leadership can motivate people to do things the way they are supposed to be done. It is not an easy job to make people follow procedures. The focus should be on preventing the problems rather than fixing them.
See Related Episode:
Eruditio Links:
- Eruditio
- HP Reliability
- Building an Effective Work Management System
- The Importance of Work Management in the Maintenance Process
- James Kovacevic’s LinkedIn
Owe Forsberg Links:
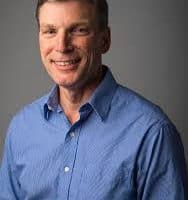
- Social:
- Link:
- Embed:
Rooted In Reliability podcast is a proud member of Reliability.fm network. We encourage you to please rate and review this podcast on iTunes and Stitcher. It ensures the podcast stays relevant and is easy to find by like-minded professionals. It is only with your ratings and reviews that the Rooted In Reliability podcast can continue to grow. Thank you for providing the small but critical support for the Rooted In Reliability podcast!
Leave a Reply